[0001] Die vorliegende Erfindung betrifft verbesserte Beschichtungsstoffe auf der Basis
von RMA-Systemen, welche mit Hilfe einer klassischen Michael-Addition vernetzen. Die
Erfindung betrifft auch die daraus herstellbaren Beschichtungen und Beschichtungssysteme
sowie beschichtete Bauteile, insbesondere Bauteile für Schienen- und Luftfahrzeuge
wie z.B. Eisenbahnwaggons oder Flugzeuge.
[0002] Beschichtungsstoffe, die in einer Michael-Additionsreaktion vernetzen, sind bekannt.
Die daraus hergestellten Beschichtungen weisen hohe Bewitterungsstabilitäten und chemische
Beständigkeiten auf. Die schnelle Aushärtung dieser Beschichtungsstoffe wird durch
den Einsatz hoher Katalysatorgehalte erreicht, wobei jedoch die Verarbeitungszeit
oder Topfzeit des Beschichtungsstoffes stark verkürzt wird.
[0003] Eine schnelle Aushärtung ist vor allem bei der Beschichtung oder Lackierung von großen
Bauteilen wie zum Beispiel in Flugzeugen oder Eisenbahnwaggons besonders vorteilhaft.
Doch allein durch die Größe der Flächen wird zur Beschichtung des gesamten Bauteils
relativ viel Zeit benötigt, so dass die eingesetzten Beschichtungsstoffe lange Topfzeiten
und lange Offenzeiten aufweisen müssen. Als Topfzeit wird im Folgenden die Zeitspanne
zwischen dem Vermischen aller Komponenten eines Beschichtungsstoffs und dem Zeitpunkt,
an dem die Vernetzungsreaktion im Beschichtungsstoff soweit fortgeschritten ist, dass
der Beschichtungsstoff nicht mehr verarbeitet werden kann, bezeichnet. Als Offenzeit
wird im Folgenden die Zeitspanne bezeichnet, in der ein auf eine Oberfläche applizierter
Beschichtungsstoff-Film noch ohne Beeinträchtigung der Verlaufseigenschaften korrigiert
werden kann.
[0004] Während der Applikation des Beschichtungsstoffs müssen die bereits beschichteten
Flächen zusätzlich den Overspray, der bei der Lackierung der angrenzenden Flächen
entsteht, aufnehmen können, ohne dass es zu Oberflächenstörungen beispielsweise durch
einen schlechten Verlauf kommt. Als Overspray wird im Folgenden der beim Spritzlackieren
verursachte Materialverlust des Beschichtungsstoffs bezeichnet. Der Materialverlust
kann verursacht werden durch Vorbeispritzen aufgrund ungünstiger Orientierung der
Spritzpistole zum Werkstück oder bei stark durchbrochenen Werkstücken wie Gittern.
Overspray kann auch durch seitlich vor den Werkstückoberflächen abströmende Beschichtungsstoff-Tröpfchen
auftreten. Overspray-Aufnahme ist dabei die Eigenschaft eines applizierten Beschichtungsstoffs,
Material aus einem Overspray so aufzunehmen, dass die gewünschte glatte Oberfläche
des Films oder der Schicht erhalten bleibt.
[0005] Nach der Applikation des Beschichtungsstoffs als Film oder Schicht auf einer Substratoberfläche
ist eine möglichst schnelle Trocknung oder Aushärtung zur Beschichtung gewünscht.
Eine forcierte Trocknung bei erhöhter Temperatur ist bei großen Bauteilen in der Regel
nicht möglich, da hierzu entsprechend große Öfen erforderlich wären. Deshalb ist vor
allem bei der Beschichtung oder Lackierung von sehr großen Bauteilen eine bei Raumtemperatur
schnelle Trocknung besonders wünschenswert.
[0006] WO 2013/050623 offenbart eine vernetzbare Zusammensetzung, enthaltend eine Komponente mit mindestens
zwei CH-aciden Protonen in aktivierten Methylen- oder Methingruppen, eine Komponente
mit mindestens zwei aktivierten ungesättigten Gruppen und ein Katalysatorsystem, das
einen basischen Michael-Additionskatalysator enthält oder generieren kann.
[0007] Aus
EP 2374836 A1 sind in einer Michael-Addition vernetzende Bindemittelsysteme, im Folgenden als RMA-Systeme
bezeichnet, bekannt, die ein günstiges Verhältnis von Topfzeit zu Trocknungszeit haben.
Die beschriebenen Bindemittelsysteme zeigen bei langen Topfzeiten auch bei Raumtemperatur
kurze Trocknungszeiten. Auf
EP 2374836 A1 wird hiermit ausdrücklich als Bestandteil der Beschreibung Bezug genommen. Nachteil
der bekannten RMA-Systeme ist, dass die daraus hergestellten Beschichtungsstoffe und
Beschichtungen nicht die erforderlichen und üblichen Eigenschaften zeigen.
[0008] Es ist daher Aufgabe der vorliegenden Erfindung verbesserte Beschichtungsstoffe,
Beschichtungen und Beschichtungssysteme auf Basis vom RMA-Systemen zur Verfügung zu
stellen, die insbesondere zur Beschichtung von Bauteilen von Luft- und Schienenfahrzeugen
geeignet sind.
[0009] Diese Aufgabe wird gelöst durch Beschichtungsstoffe zur Herstellung einer Beschichtung
gemäß Hauptanspruch. Weitere Ausführungsformen werden in den Neben- und Unteransprüchen
sowie der Beschreibung offenbart,
[0010] Die erfindungsgemäßen Beschichtungsstoffe umfassen zumindest ein RMA-System, welches
ein oder mehrere CH-acide Verbindungen A, ein oder mehrere vinyloge Carbonylverbindungen
B und einen oder mehrere latent-basische Katalysatoren C aufweist, sowie ein oder
mehrere Lichtschutzmittel, ein oder mehrere Topfzeit-Verlängerer und ein oder mehrere
Offenzeit-Verlängerer.
[0011] Im Folgenden werden unter dem Begriff Lichtschutzmittel Additive und Hilfsstoffe
verstanden, die Beschichtungen gegen den Einfluss von UV-Licht schützen, insbesondere
einen durch UV-Strahlung verursachten Polymerabbau verhindern oder zumindest deutlich
verzögern. Unter dem Begriff Topfzeit-Verlängerer werden Additive und Hilfsstoffe
verstanden, die als Bestandteil des verarbeitungsfertig angemischten Beschichtungsstoffs
die Aushärtung des Beschichtungsstoffs vor der Applikation verzögern. Sie verdampfen
während der Applikation, so dass die Härtung des applizierten Beschichtungsstoffs
nicht beeinträchtigt, insbesondere nicht verlängert, wird. Unter dem Begriff Offenzeit-Verlängerer
werden Additive und Hilfsstoffe verstanden, die auch nach der Applikation im Beschichtungsstoff
verbleiben und dessen Aushärtung zur Beschichtung verzögern.
[0012] Die erfindungsgemäßen Beschichtungsstoffe enthalten zumindest
- 15 bis 70, bevorzugt 20 bis 60, besonders bevorzugt 25 bis 55 Gew.-%, ein oder mehrere
CH-acide Verbindungen A, ausgewählt aus Verbindungen der Formel
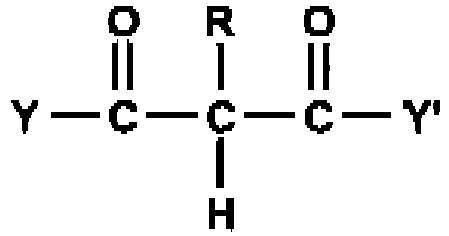
wobei
- R
- Wasserstoff, ein Alkyl- oder Arylrest,
- Y
- ein Alkyl-, Aralkyl-, Aryl-, Alkoxy-Rest oder eine Aminogruppe und,
- Y'
- ein Alkyl-, Aralkyl-, Aryl-, Alkoxy-Rest oder eine Aminogruppe ist,
- 4 bis 40, bevorzugt 8 bis 35, besonders bevorzugt 10 bis 30 Gew.-%, ein oder mehrere
vinyloge Carbonylverbindungen B aus gewählt aus Acrylaten und Maleaten,
- 0,1 bis 15, bevorzugt 0,2 bis 10, besonders bevorzugt 0,3 bis 5 Gew.-%, ein oder mehrere
latent-basische Katalysatoren C,
- 0,00001 bis 10, bevorzugt 0,5 bis 5, besonders bevorzugt 1 bis 3 Gew.-%, ein oder
mehrere Lichtschutzmittel, welche ausgewählt sind aus der Gruppe enthaltend Radikalfänger,
UV-Absorber, Quencher und Peroxidzersetzer,
- 0,00001 bis 20, bevorzugt 0,01 bis 10, besonders bevorzugt 0,1 bis 5 Gew.-%, ein oder
mehrere Offenzeit-Verlängerer, welche ausgewählt sind aus der Gruppe enthaltend basische
NH-funktionelle Verbindungen mit pKa-Werten zwischen 4 und 14, und,
- 0,00001 bis 20, bevorzugt 0,01 bis 15, besonders bevorzugt 0,1 bis 10 Gew.-%, ein
oder mehrere Topfzeit-Verlängerer, welche ausgewählt sind aus der Gruppe enthaltend
Alkohole mit bis zu 6 Kohlenstoffatomen und Verdunstungszahlen unter 35,
jeweils bezogen auf die Gesamtmenge des Beschichtungsstoffs.
[0013] Weiterhin können die erfindungsgemäßen Beschichtunsstoffe
- 0 bis 70, bevorzugt 0,00001 bis 65, besonders bevorzugt 0,00001 bis 40 Gew.-%, Pigmente,
- 0 bis 25, bevorzugt 0,00001 bis 8, besonders bevorzugt 0,00001 bis 5 Gew.-%, Dispergieradditive,
- 0 bis 60, bevorzugt 0,00001 bis 40, besonders bevorzugt 0,00001 bis 30 Gew.-%, funktionale
Füllstoffe und
- 0 bis 50, bevorzugt 0,00001 bis 40, besonders bevorzugt 0,00001 bis 30 Gew.-%, aprotische
Lösemittel enthalten,
wobei sich die Mengenangaben jeweils auf die Gesamtmenge des Beschichtungsstoffs beziehen.
[0014] Erfindungsgemäß werden die Verbindungen A und B in einem Stoffmengenverhältnis A:B
von 0,5:1 bis 2:1, bevorzugt von 0,75:1 bis 1,6:1, besonders bevorzugt von 0,9:1 bis
1,3:1, ganz besonders bevorzugt von 0,95:1 bis 1,1:1 eingesetzt, wobei die Stoffmengen
auf die aciden Protonen der Verbindungen A und auf die vinylogen Carbonylgruppen der
Verbindungen B bezogen sind,
[0015] Erfindungsgemäß werden die Katalysatoren C und Verbindungen A in einem Stoffmengenverhältnis
C:A von 0,8:1 bis 2,5:1, bevorzugt 1,1:1 bis 1,9:1, besonders bevorzugt 1,3:1 bis
1,7:1 eingesetzt, wobei die Stoffmengen auf das Kation X
+ des Katalysators C und die aciden Protonen der Verbindungen A bezogen sind.
[0016] Erfindungsgemäß geeignete CH-acide Verbindungen A sind Malonsäureester, Acetessigsäureester
oder deren Gemische eingesetzt. Besonders bevorzugt sind Malonsäureester mit oligomeren
und polymeren Substituenten beispielsweise auf der Basis von Polyestern, Polyurethanen,
Polyacrylaten, Epoxidharzen, Polyamiden oder Polycarbonaten. Besonders bevorzugt sind
Malonsäureester mit oligomeren und polymeren Substituenten auf Basis von Polyestern,
Polyurethanen und/oder Polycarbonaten. Die eingesetzten Acetessigsäureester enthalten
bevorzugt oligomere und polymere Substituenten beispielsweise auf der Basis von Polyalkoholen,
Polyvinylalkoholen, Epoxidharzen, hydroxyfunktionellen Polyethern, Polyestern oder
Polyacrylaten. Besonders bevorzugt sind Acetessigsäureester mit oligomeren und polymeren
Substituenten auf Basis von Polyestern und/oder Polyacrylaten. Ganz besonders bevorzugt
sind Verbindungen ausgewählt aus der Gruppe enthaltend Malonsäureester mit oligomeren
und polymeren Substituenten auf der Basis von Polyestern, die aus der Umsetzung von
zumindest Malonsäure, Malonsäuredimethylester und/oder Malonsäurediethylester mit
Hexahydrophthalsäure und/oder deren Anhydrid und Neopentylglycol erhalten werden,
sowie Acetessigsäureester mit oligomeren und polymeren Substituenten auf der Basis
Polyestern, die aus der Umsetzung von zumindest Acetessigsäure, Acetessigsäuremethylester
und/oder Acetessigsäureethylester mit Hexahydrophthalsäure und/oder deren Anhydrid
und Neopentylglycol erhalten werden.
[0017] Erfindungsgemäß geeignete vinyloge Carbonylverbindungen B sind beispielsweise ungesättigte
acryloyl-funktionale Acrylate und/oder Maleate. Erfindungsgemäß bevorzugt sind Acrylester
aus Verbindungen enthaltend 1 bis 20 Kohlenstoffatome und zumindest 2, bevorzugt 2
bis 6, Hydroxylgruppen. Erfindungsgemäß bevorzugt sind weiterhin Polyester aus Maleinsäure,
Fumarsäure und/oder Itaconsäure oder deren Anhydride umgesetzt mit di- oder polyvalenten
Hydroxylverbindungen, die eine monovalente Hydroxyl- oder Carboxylverbindung enthalten
können. Weiterhin bevorzugt sind Harze wie Polyester, Polyurethane, Polyether und/oder
Alkydharze, welche entsprechend aktivierte ungesättigte Gruppen enthalten wie beispielsweise
Urethanacrylate, Polyetheracrylate, polyfunktionelle Polyacrylate, Polyalkylmaleate
und Polyacrylate, die aus der Umsetzung von Acrylsäure mit Epoxidharzen erhalten werden.
Erfindungsgemäß besonders bevorzugt sind Butandioldiacrylat, Hexandioldiacrylat, Trimethylolpropantriacrylat,
Pentaerythritoltetraacrylat und Ditrimethylolpropantetraacrylat und Dipentaerithritol-hexa-acrylat
sowie Dipropylenglykoldiacrylat und Tripropylenglykoldiacrylat.
[0018] Geeignete latent-basische Verbindungen für die Katalysatoren C sind beispielsweise
substituierte Carbonsäuresalze der Formel II:

worin
- R
- Wasserstoff, Alkyl- oder Aralkyl- (Ar-R) oder ein Polymer ist,
- X+
- ein Alkali- oder Erdalkalimetall-Kation, insbesondere Lithium, Natrium oder Kalium
ist, oder ein quaternäres Ammonium- oder Phosphoniumsalz der Formel (R')4Y+ ist, worin Y
Y Stickstoff oder Phosphor ist,
R' gleich oder verschieden, Wasserstoff, Alkyl-, Aral- oder Aralkyl- oder ein Polymer
ist
und worin
R und R' eine Ringstruktur bilden können oder
R und R' ein Polymer sein können.
[0019] Erfindungsgemäß bevorzugt ist R eine Alkylgruppe oder eine Aralkylgruppe, besonders
bevorzugt eine Alkylgruppe mit 1 bis 4 Kohlenstoffatomen. Die Carbonatgruppe und das
Kation X
+ können darüber hinaus auch an einem Molekül mit der entsprechenden Struktur vorhanden
sein. Weiterhin bevorzugt ist R' eine Alkylgruppe, besonders bevorzugt eine Alkylgruppe
mit 1 bis 4 Kohlenstoffatomen, besonders bevorzugt mit 3 bis 4 Kohlenstoffatomen.
Erfindungsgemäß bevorzugt werden Ammonium- und/oder Phosphoniumcarbonate eingesetzt.
Geeignete Ammoniumcarbonate sind beispielsweise Tetrahexylammoniummethylcarbonat,
Tetrahexylammoniumhydrogencarbonat, Tetradecanyltrihexylammoniummethylcarbonat, Tetradecylammoniummethylcarbonat,
Tetrabutylammoniummethylcarbonat, Tetrabutylammoniumethylcarbonat, Tetrabutylammoniumhydrogencarbonat,
Tetrapropylammoniummethylcarbonat, Tetrapropylammoniumethylcarbonat, Tetrapropylammoniumhydrogencarbonat,
Benzyltrimethylammoniummethylcarbonat, Trihexylmethylammoniummethylcarbonat oder Trioctylmethylammoniummethylcarbonat.
Besonders bevorzugt werden Tetrabutylammoniummethylcarbonat, Tetrabutylammoniumethylcarbonat,
Tetrabutylammoniumhydrogencarbonat, Tetrapropylammoniummethylcarbonat, Tetrapropylammoniumethylcarbonat,
Tetrapropylammoniumhydrogencarbonat und deren Gemische eingesetzt.
[0020] Geeignete Lichtschutzmittel sind Radikalfänger wie sterisch gehinderte aliphatische
Amine z.B. auf Basis substituierter 2,2,6,6-Tetramethylpiperidine, UV-Absorber wie
2-Hydroxyphenylbenztriazole, 2-Hydroxybenzophenone, 2-Hydroxyphenyltriazine oder Oxalanilide,
sowie Quencher wie organische Nickelverbindungen und Peroxidzersetzer wie Thioether
oder Phosphite. Bevorzugt eingesetzt werden Radikalfänger beispielsweise sterisch
gehinderte aliphatische Amine auf Basis substituierter 2,2,6,6-Tetramethylpiperidine,
und/oder UV-Absorber beispielsweise 2-Hydroxyphenylbenztriazole, 2-Hydroxybenzophenone,
2-Hydroxyphenyltriazine und Oxalanilide. Besonders bevorzugt eingesetzt werden substituierte
2,2,6,6-Tetramethylpiperidine, 2-Hydroxyphenyltriazine, 2-Hydroxybenzophenone und
deren Gemische.
[0021] Geeignete Topfzeit-Verlängerer sind Alkohole mit bis zu 6, bevorzugt bis zu 4, besonders
bevorzugt bis zu 3 Kohlenstoffatomen, die eine Verdunstungszahl unter 35, bevorzugt
unter 20 aufweisen. So können erfindungsgemäß beispielsweise Methanol, Ethanol, n-Propanol,
i-Propanol, n-Butanol, i-Butanol und deren Gemische eingesetzt werden.
[0022] Geeignete Offenzeit-Verlängerer sind basische NH-funktionelle Verbindungen mit einem
pK
a-Wert zwischen 4 und 14. Bevorzugt sind Succinimide, 1,2,4,-Triazole, 1,2,3,-Benzotriazole,
5,5-Diphenylhydantoine, Hydantoine, (RS)-3-Ethyl-3-methylpyrrolidin-2,5-dion und deren
Gemische. Besonders bevorzugt sind Succinimide, 1,2,4,-Triazole, 1,2,3,-Benzotriazole
und deren Gemischen.
[0023] In einer weiteren Ausführungsform der vorliegenden Erfindung können den Beschichtungsstoffen
zur Herstellung einer farbgebenden Beschichtung anorganische und/oder organische Pigmente
zugesetzt werden. Auch weitere Additive wie Dispergieradditive und funktionale Füllstoffe
können zugesetzt werden, um die erforderlichen Eigenschaften des Beschichtungsstoffes
und/oder der Beschichtung zu verbessern.
[0024] Anorganische und/oder organische Pigmente können den erfindungsgemäßen Beschichtungsstoffen
in Mengen bis zu 70, bevorzugt 0,00001 bis 65, besonders bevorzugt 0,00001 bis 40
Gew.-% zugegeben werden, wobei sich die Mengenangaben jeweils auf die Gesamtmenge
des Beschichtungsstoffs beziehen. Geeignete anorganische Pigmente sind beispielsweise
Titandioxid, Eisenoxide, Chromoxide, Chromtitanate, Bismutvanadat, Cobaltblau und
Ruße. Bevorzugt eingesetzte anorganische Pigmente sind Titandioxid, Eisenoxide und
Ruße. Geeignete organische Pigmente sind beispielsweise Pigment Yellow 151, Pigment
Yellow 213, Pigment Yellow 83, Pigment Orange 67, Pigment Orange 62, Pigment Orange
36, Pigment Red 170, Pigment Violet 19, Pigment Violet 23, Pigment Blue 15:3, Pigment
Blue 15:6, Pigment Green 7. Bevorzugt eingesetzte Pigmente sind Pigment Yellow 151,
Pigment Orange 67, Pigment Red 170, Pigment Violet 19, Pigment Blue 15:3, Pigment
Green 7.
[0025] In einer weiteren Ausführungsform können die Beschichtungsstoffe zusätzlich bis zu
25, bevorzugt 0,00001 bis 8, besonders bevorzugt 0,00001 bis 5 Gew.-% Dispergieradditive
enthalten, wobei sich die Mengenangaben jeweils auf die Gesamtmenge des Beschichtungsstoffes
beziehen. Geeignete Dispergieradditive sind beispielsweise hochmolekulare Blockcopolymere
mit pigmentaffinen Gruppen, hochverzweigte Polyester, Acrylat-Polyester-Copolymere
mit pigmentaffinen Gruppen. Bevorzugt eingesetzte Dispergieradditive sind hochmolekulare
Blockcopolymere mit pigmentaffinen Gruppen.
[0026] In einer weiteren Ausführungsform können die Beschichtungsstoffe zusätzlich bis zu
60, bevorzugt 0,00001 bis 50, besonders bevorzugt 0,00001 bis 40 Gew.-% funktionale
Füllstoffe enthalten, wobei sich die Mengenangaben jeweils auf die Gesamtmenge des
Beschichtungsstoffs beziehen. Geeignete Füllstoffe sind beispielsweise Carbonate wie
Kreide, Kalksteinmehl, Calcit, gefälltes Calciumcarbonat, Dolomit, Bariumcarbonat,
Sulfate wie Baryt, Blanc fixe, Calciumsulfat, Silikate wie Talk, Pyrophyllit, Chlorit,
Hornblende, Glimmer, Kaolin, Wollastonit, Schiefermehl, gefällte Calciumsilikate,
gefällte Aluminiumsilikate, gefällte Calcium-Aluminiumsilikate, gefällte Natrium-Aluminiumsilikate,
Feldspäte, Mullit, Kieselsäuren wie Quarz, Quarzgut, Cristobalit, Kieselgur, Kieselerde,
gefällte Kieselsäure, Bimsmehl, Perlit, Calcium-Metasilikate, Fasern aus Schmelzen
von Glas oder Basalten, Glasmehl, Glaskugeln und Schlacken. Bevorzugt eingesetzte
Füllstoffe sind Bariumsulfat und/oder Talkum.
[0027] In weiteren erfindungsgemäßen Ausführungsformen enthalten die Beschichtungsstoffe
darüber hinaus bis zu 50, bevorzugt 0,00001 bis 40, besonders bevorzugt 0,00001 bis
30 Gew.-% aprotische Lösemittel, wobei sich die Mengenangaben jeweils auf die Gesamtmenge
des Beschichtungsstoffes beziehen. Unter dem Begriff aprotische Lösemittel werden
im Folgenden Lösemittel verstanden, die kein ionisierbares Proton im Molekül enthalten.
Geeignete aprotische Lösemittel sind beispielsweise aliphatische Kohlenwasserstoffe,
cycloaliphatische Kohlenwasserstoffe, aromatische Kohlenwasserstoffe, Ketone, Ester,
Ether, Etherester insbesondere Ethylacetat, Butylacetat, Aceton, n-Butanon, Methylisobutylketon,
Methoxypropylacetat sowie Dimethylsulfoxid. Bevorzugt eingesetzte Lösungsmittel sind
Ethylacetat, Butylacetat, Aceton, n-Butanon, Methylisobutylketon, Methoxypropylacetat
und deren Gemische.
[0028] Die als erfindungsgemäße Katalysatoren C eingesetzten Verbindungen sind latente Base,
da das Carbonatsalz gemäß Formel II im Gleichgewicht mit seinen Dissoziationsprodukten
Kohlendioxid und der entsprechenden Hydroxid- oder Alkoxy-Base steht. Solange Kohlendioxid
aus dem System nicht entweichen kann, liegt das Gleichgewicht auf der Seite des Carbonatsalzes.
Erst wenn Kohlendioxid entfernt wird und somit eine hinreichende Menge an Base vorliegt,
startet die Vernetzung mittels Michael-Addition. Bei einer Lagerung der erfindungsgemäßen
Beschichtungsstoffe in geschlossen Behältern, aus denen Kohlendioxid nicht entweichen
kann, kann der Beschichtungsstoff grundsätzlich als ein Einkomponentensystem formuliert
werden. Die Lagerstabilität kann jedoch erhöht werden, wenn die einzelnen Bestandteile
des erfindungsgemäßen Beschichtungsstoffs in Mehrkomponentensystemen formuliert werden.
So kann beispielsweise eine Katalysatorkomponente, welche die Katalysatoren C enthält,
erst kurz vor der Verarbeitung mit den Bindemittelkomponenten, welche die CH-aciden
Verbindungen A und die vinylogen Carbonylverbindungen B enthalten, vermischt werden.
[0029] Erfindungsgemäß können die CH-acide Verbindungen A und die vinylogen Carbonylverbindungen
B zusammen mit den eingesetzten Lichtschutzmitteln, Offenzeit-Verlängerern und Topfzeit-Verlängerern
in einer Bindemittelkomponente enthalten sein. Diese Bindemittelkomponente kann weiterhin
Pigmente, zusätzliche weitere Additive sowie Lösemittel enthalten. Die Katalysatoren
C sowie gegebenenfalls weitere Lösemittel und Topfzeit-Verlängerer können in einer
Katalysatorkomponente enthalten sein. In einer bevorzugten Ausführungsform können
die CH-acide Verbindungen A in einer ersten Bindemittelkomponente, die vinylogen Carbonylverbindungen
B in einer zweiten Bindemittelkomponente und die Katalysatoren C in einer Katalysatorkomponente
vorliegen. In einem solchen Dreikomponenten-System sind bevorzugt die CH-aciden Verbindungen
A zusammen mit den Offenzeit-Verlängerern und Lichtschutzmitteln in der ersten Bindemittelkomponente
enthalten. Gegebenenfalls kann diese erste Bindemittelkomponente weiterhin Pigmente
und Füllstoffe sowie zusätzliche Additive enthalten. In der zweiten Bindemittelkomponente
sind bevorzugt die vinylogen Carbonylverbindungen B enthalten. Weiterhin kann auch
die zweite Bindemittelkomponente Pigmente, Füllstoffe und zusätzliche Additive enthalten.
In der Katalysatorkomponente sind die Katalysatoren C enthalten. Weiterhin kann die
Katalysatorkomponente Lösemittel und Topfzeit-Verlängerer enthalten.
[0030] Es ist bekannt, dass die Zugabe weiterer Bestandteile, die zur Herstellung einer
Beschichtung üblich sind, die Lagerstabilität der RMA-Systeme verringert. Die erfindungsgemäßen
Beschichtungsstoffe mit ihrer besonderen Auswahl an Lichtschutzmitteln, Offenzeit-Verlängern,
Topfzeit-Verlängern, Pigmenten, Dispergieradditiven, funktionalen Füllstoffen und
aprotischen Lösemitteln weisen im Vergleich zu bisher bekannten Beschichtungsstoffen
auf Basis von RMA-Systemen eine unerwartete hohe Lagerstabilität auf.
[0031] Weiterhin werden auch die Eigenschaften von Beschichtungen, welche aus Beschichtungsstoffen
auf Basis von RMA-Systemen hergestellt sind, im Unterschied zu Beschichtungen, welche
aus Beschichtungstoffen auf Basis üblicher Bindemitteln wie beispielsweise Epoxidharzen
oder Polyurethanen hergestellt sind, stark vom Vorhandensein weiterer Bestandteile
des Beschichtungstoffs negativ beeinflusst. Es hat sich überraschenderweise gezeigt,
dass die erfindungsgmäßen Beschichtungsstoffe Beschichtungen ergeben, welche die für
eine Verwendung bei Bauteilen von Schienen- und Luftfahrzeugen erforderlichen Eigenschaften,
insbesondere Glanzhaltung, mechanische Stabilität und Lichtstabilität, aufweisen.
[0032] In einer besonders bevorzugten Ausführungsform umfassen die erfindungsgemäßen Beschichtungsstoffe
zumindest
- 15 bis 70, bevorzugt 20 bis 60, besonders bevorzugt 25 bis 55 Gew.-% Malonsäureester
mit oligomeren und Polymeren Substituenten auf der Basis von Polyestern, die aus der
Umsetzung von zumindest Malonsäure, Malonsäuredimethylester und/oder Malonsäurediethylester
mit Hexahydrophthalsäure und/oder deren Anhydrid und Neopentylglycol erhalten werden,
sowie Acetessigsäureester mit oligomeren und polymeren Substituenten auf der Basis
Polyestern, die aus der Umsetzung von zumindest Acetessigsäure, Acetessigsäuremethylester
und/oder Acetessigsäureethylester mit Hexahydrophthalsäure und/oder deren Anhydrid
und Neopentylglycol erhalten werden, als CH-acide Verbindungen A
- 4 bis 40, bevorzugt 8 bis 35, besonders bevorzugt 10 bis 30 Gew.-% Butandioldiacrylat,
Hexandioldiacrylat, Trimethylolpropantriacrylat, Pentaerythritoltetraacrylat, Ditrimethylolpropantetraacrylat
und/oder Dipentaerithritolhexaacrylat als vinyloge Carbonylverbindungen B,
- 0,1 bis 15, bevorzugt 0,2 bis 10, besonders bevorzugt 0,3 bis 5 Gew.-% Tetrabutylammoniummethylcarbonat,
Tetrabutylammoniumethylcarbonat, Tetrabutylammoniumhydrogencarbonat, Tetrapropylammoniummethylcarbonat,
Tetrapropylammoniumethylcarbonat, Tetrapropylammoniumhydrogencarbonat oder deren Gemische
als latent-basische Katalysatoren C,
- 0,00001 bis 10, bevorzugt 0,5 bis 5, besonders bevorzugt 1 bis 3 Gew.-% substituierte
2,2,6,6-Tetramethylpiperidine, 2-Hydroxyphenyltriazine, 2-Hydroxybenzophenone oder
deren Gemische als Lichtschutzmittel,
- 0,00001 bis 20, bevorzugt 0,01 bis 10, besonders bevorzugt 0,1 bis 5 Gew.-% Succinimide,
1,2,4,-Triazole, 1,2,3,-Benzotriazole oder deren Gemische als Offenzeit-Verlängerer,
- 0,00001 bis 20, bevorzugt 0,01 bis 15, besonders bevorzugt 0,1 bis 10 Gew.-% Methanol,
Ethanol, n-Propanol, i-Propanol, n-Butanol, i-Butanol oder deren Gemische als Topfzeit-Verlängerer,
- 0 bis 50, bevorzugt 0,00001 bis 40, besonders bevorzugt 0,00001 bis 30 Gew.-% Ethylacetat,
Butylacetat, Aceton, n-Butanon, Methylisobutylketon, Methoxypropylacetat oder deren
Gemische als aprotische Lösemittel,
wobei sich die Mengenangaben jeweils auf die Gesamtmenge des Beschichtungsstoffes
beziehen.
[0033] In einer weiteren besonders bevorzugten Ausführungsform weisen die erfindungsgemäßen
Beschichtungsstoffe zumindest
- 15 bis 70, bevorzugt 20 bis 60, besonders bevorzugt 20 bis 55 Gew.-% Malonsäureester
mit oligomeren und polymeren Substituenten auf der Basis von Polyestern, die aus der
Umsetzung von zumindest Malonsäure, Malonsäuredimethylester und/oder Malonsäurediethylester
mit Hexahydrophthalsäure und/oder deren Anhydrid und Neopentylglycol erhalten werden,
sowie Acetessigsäureester mit oligomeren und polymeren Substituenten auf der Basis
Polyestern, die aus der Umsetzung von zumindest Acetessigsäure, Acetessigsäuremethylester
und/oder Acetessigsäureethylester mit Hexahydrophthalsäure und/oder deren Anhydrid
und Neopentylglycol erhalten werden, als CH-acide Verbindungen A,
- 4 bis 40, bevorzugt 8 bis 35, besonders bevorzugt 10 bis 30 Gew.-% Butandioldiacrylat,
Hexandioldiacrylat, Trimethylolpropantriacrylat, Pentaerythritoltetraacrylat, Ditrimethylolpropantetraacrylat
und/oder Dipentaerithritolhexaacrylat als vinyloge Carbonylverbindungen B,
- 0,1 bis 15, bevorzugt 0,2 bis 10, besonders bevorzugt 0,3 bis 5 Gew.-% Tetrabutylammoniummethylcarbonat,
Tetrabutylammoniumethylcarbonat, Tetrabutylammoniumhydrogencarbonat, Tetrapropylammoniummethylcarbonat,
Tetrapropylammoniumethylcarbonat, Tetrapropylammoniumhydrogencarbonat oder deren Gemische
als vinyloge Carbonylverbindungen B,
- 0,00001 bis 10, bevorzugt 0,5 bis 5, besonders bevorzugt 1 bis 3 Gew.-% substituierte
2,2,6,6-Tetramethylpiperidine, 2-Hydroxyphenyltriazine, 2-Hydroxybenzophenone oder
deren Gemische als Lichtschutzmittel,
- 0,00001 bis 20, bevorzugt 0,01 bis 10, besonders bevorzugt 0,1 bis 5 Gew.-% Succinimide,
1,2,4,-Triazole, 1,2,3,-Benzotriazole oder deren Gemische als Offenzeit-Verlängerer,
- 0,00001 bis 20, bevorzugt 0,01 bis 15, besonders bevorzugt 0,1 bis 10 Gew.-% Methanol,
Ethanol, n-Propanol, i-Propanol, n-Butanol, i-Butanol oder deren Gemische als Topfzeit-Verlängerer,
- 0 bis 70, bevorzugt 0,00001 bis 65, besonders bevorzugt 0,00001 bis 40 Gew.-% Titandioxid,
Eisenoxide, Ruße, Pigment Yellow 151, Pigment Orange 67, Pigment Red 170, Pigment
Violet 19, Pigment Blue 15:3, Pigment Green 7 oder deren Gemische als Pigmente,
- 0 bis 25, bevorzugt 0,00001 bis 8, besonders bevorzugt 0,00001 bis 5 Gew.-% hochmolekulare
Blockcopolymere mit pigmentaffinen Gruppen als Dispergieradditive,
- 0 bis 60, bevorzugt 0,00001 bis 40, besonders bevorzugt 0,00001 bis 30 Gew.-% Bariumsulfat
und/oder Talkum als funktionale Füllstoffe und
- 0 bis 50, bevorzugt 0,00001 bis 40, besonders bevorzugt 0,00001 bis 30 Gew,-% Ethylacetat,
Butylacetat, Aceton, n-Butanon, Methylisobutylketon, Methoxypropylacetat oder deren
Gemische als aprotische Lösemittel,
wobei sich die Mengenangaben jeweils auf die Gesamtmenge des Beschichtungsstoffes
beziehen.
[0034] Die erfindungsgemäßen Beschichtungsstoffe können zur Herstellung von Beschichtungssystemen
verwendet werden, welche einen Aufbau aus zwei oder mehr Beschichtungen aufweisen.
Die erfindungsgemäßen Beschichtungsstoffe können dabei zur Herstellung zumindest einer
Schicht oder Beschichtung eingesetzt werden. In einer bevorzugten Ausführungsform
werden die Beschichtungsstoffe zur Herstellung eines Zweischichtaufbaus eingesetzt,
besonders bevorzugt werden sie zum Aufbau eines Basislack-Klarlack-Systems eingesetzt.
Als Klarlacke werden im Folgenden Beschichtungsstoffe und Beschichtungen bezeichnet,
welche keine Farbmittel enthalten. Als Basislacke werden im Folgenden Beschichtungsstoffe
und Beschichtungen bezeichnet, welche Farbmittel wie beispielsweise Farbstoffe oder
Pigmente enthalten. Basislack-Klarlack-Systeme werden häufig auch bei Luft- und Schienenfahrzeugen
eingesetzt, da sie sehr witterungsbeständig sind, vor allem in Bezug auf den Glanzerhalt.
[0035] Die erfindungsgemäßen Beschichtungsstoffe und Beschichtungen weisen gegenüber den
bisher bekannten RMA-Beschichtungsstoffen und -Beschichtungen überraschenderweise
eine deutlich höhere Lagerstabilität auf. Auch zeigen sie ein verbessertes Trockungsverhalten.
Die aus den erfindungsgemäßen Beschichtungsstoffen erhaltenen Beschichtungen weisen
darüber hinaus eine verbesserte Lichtstabilität auf, insbesondere weniger Vergilbung
und höhere Glanzhaltung.
[0036] Die erfindungsgemäßen Beschichtungsstoffe weisen Topfzeiten größer gleich 1 Stunde,
bevorzugt größer gleich 2 Stunden, besonders bevorzugt zwischen 2 und 4 Stunden auf.
Üblicherweise wird die Topfzeit über die Auslaufzeit aus einem Auslaufbecher bestimmt.
Das Ende der Topfzeit ist festgelegt, als der Zeitpunkt in dem die Auslaufzeit den
doppelten Wert der Start-Auslaufzeit zeigt. Die Prüfmethode wird unten in den Beispielen
ausführlich beschrieben. Weiterhin zeigen die erfindungsgemäßen Beschichtungsstoffe
Offenzeiten von größer gleich 15 Minuten, bevorzugt größer 20 Minuten, besonders bevorzugt
größer gleich 25 Minuten. Neben den langen Topf- und Offenzeiten zeigen die erfindungsgemäßen
Beschichtungsstoffe überraschenderweise ein ungewöhnlich breites Klimafenster, in
dem sie ohne Beeinträchtigung verarbeitet werden können. Sie sind beispielsweise bei
Temperaturen bis zu 45 C und bei relativer Luftfeuchte bis zu 99 % verarbeitbar. Darüber
hinaus zeigen sie eine lange Overspray-Aufnahme, beispielsweise über einen Zeitraum
von mehr als 25 Minuten.
[0037] Im Unterschied zu üblicherweise eingesetzten Beschichtungsstoffen auf Polyurethan-Basis
weisen die erfindungsgemäßen Beschichtungsstoffe deutlich verkürzte Trocknungszeiten
auf. Darüber hinaus sind die erfindungsgemäßen Beschichtungen schneller abklebbar,
d.h. sie sind bei Raumtemperatur bereits 1 bis 4 Stunden nach der Applikation so weit
ausgehärtet, dass z.B. Musterschablonen aufgeklebt werden können, die nach der Auflackierung
des Musters ohne Beschädigung der Beschichtung wieder entfernt werden können. Aufgeklebte
Schablonen werden üblicherweise zur Anbringung farblicher Dekore und Muster auf einer
Beschichtung eingesetzt.
[0038] Mit ihren Eigenschaften sind die erfindungsgemäßen Beschichtungsstoffe vor allem
für eine Verwendung zur Beschichtung großer Bauteile geeignet. Sie sind insbesondere
zur Beschichtung großflächiger Bauteile geeignet wie sie beispielsweise im Waggon-
und Flugzeugbau verwendet werden.
[0039] Die vorliegenden Erfindung betrifft auch Verfahren zur Beschichtung von Bauteilen.
Die erfindungsgemäßen Verfahren umfassen dabei die Schritte (a) Applizieren des erfindungsgemäßen
Beschichtungsstoffs auf der Oberfläche eines Substrats und (b) Aushärten des applizierten
Beschichtungsstoffes für 1 bis 12, bevorzugt 1 bis 6, besonders bevorzugt 1 bis 4
Stunden bei Temperaturen zwischen 5 bis 45, bevorzugt 15 bis 40, besonders bevorzugt
20 bis 35 °C.
[0040] Die erfindungsgemäßen Beschichtungsstoffe weisen überdurchschnittlich hohe Festkörpergehalte
auf und enthalten dementsprechend geringe Anteile an leichtflüchten organischen Substanzen
wie beispielsweise Lösemitteln. Der Festkörpergehalt ist definiert als der Massenanteil
eines Beschichtungsstoffs, der beim Eindampfen bei 105 °C nach 30 Minuten als Rückstand
verbleibt. Im Wesentlichen besteht der Festkörper in der Regel aus Bindemittel, nicht
flüchtigen Additiven, Pigmenten und Füllstoffen. Die Festkörpergehalte der erfindungsgemäßen
Beschichtungsstoffe liegen zwischen 65 und 95, bevorzugt 70 und 90, besonders bevorzugt
zwischen 75 und 85 Gew.-%, bezogen auf das Gesamtgewicht des Beschichtungsstoffs.
[0041] Üblicherweise sind Beschichtungsstoffe mit hohen Festkörpergehalten mit den üblichen
Spritzverfahren schlecht verarbeitbar. Im Unterschied dazu können die erfindungsgemäßen
Beschichtungsstoffe ohne Weiteres mit Hilfe von hydraulischem Höchstdruckspritzen
(Airless), Airless-Spritzen mit Luftunterstützung (Airmix) sowie mit Hilfe von pneumatischen
Spritzen oder Druckluftspritzen appliziert werden. Auch bei diesen Applikationsverfahren
werden hier überraschenderweise Oberflächen hoher Güte erhalten. Erfindungsgemäß besonders
geeignet sind elektrostatisch unterstützte Airspray- oder Airmixverfahren.
[0042] Geeignete Substrate sind Metalle wie beispielsweise Aluminium, Aluminiumlegierungen,
Stähle und Eisenlegierungen, Kunststoffe sowie glas- und kohlefaserverstärkte Faserverbundwerkstoffe.
Die zu beschichtenden Bauteiloberflächen können mit einer Grundierung versehen sein
wie beispielsweise die üblichen, dem Fachmann bekannten Grundierungen auf Basis von
Epoxid-Harzen oder Polyurethanen.
[0043] Bei erfindungsgemäßen Beschichtungsstoffen, welche mehrere Komponenten aufweisen,
werden alle Komponenten vor der Applikation vermischt. Die Mischung kann dabei manuell
oder maschinell erfolgen. In einer weiteren Ausführungsform kann ein Beschichtungssystem
mit zumindest einer zusätzlichen Beschichtung hergestellt werden, indem auf der ersten
Beschichtung weitere Beschichtungsstoffe appliziert und ausgehärtet werden.
[0044] In einer bevorzugten Ausführungsform des erfindungsgemäßen Verfahrens wird ein Beschichtungssystem
in einem Zweischichtaufbau hergestellt. Zunächst wird ein Basislack appliziert und
ausgehärtet, auf diese Beschichtung wird dann ein Klarlack aufgebracht und ausgehärtet.
Dabei können Basislack oder Klarlack oder auch Basis- und Klarlack aus den erfindungsgemäßen
Beschichtungsstoffen hergestellt werden.
[0045] Die erfindungsgemäßen Beschichtungen weisen eine Trockenschichtdicke von 20 bis 150
µm auf. Geringe Trockenschichtdicken mit dennoch hoher Deckkraft sind insbesondere
bei Beschichtung von Bauteilen für die Luftfahrt geeignet, da so Gewicht eingespart
werden kann.
[0046] Da die erfindungsgemäßen Beschichtungsstoffe bei Raumtemperatur ausgehärtet werden
können, sind sie vor allem zur Beschichtung von großen Bauteilen, wie sie beispielsweise
zum Bau von Flugzeugen und Eisenbahnwagons verwendet werden, geeignet. Sie sind insbesondere
zur Beschichtung von Rumpfteilen, Flügeln, Radomen, Seitenleitwerken, Höhenleitwerken,
Triebwerksverkleidungen, Winglets und Landeklappen sowie für Triebköpfe, Waggonteile,
Dächer, Türen und Fahrwerksverkleidungen geeignet. Sie sind auch geeignet zur Beschichtung
von Interieurbauteilen von Schienen- und Luftfahrzeugen wie beispielsweise Deckenpanelen,
Wandverkleidungen, Fußbodenpanelen, Hatrack-Klappen und Türen.
Beispiele
[0047] Die Herstellung der Beschichtungsstoffe erfolgt nach den lacktechnischen Standards,
welche dem Fachmann bekannt und geläufig sind. Die in den Beispielrezepturen 1 und
2 eingesetzte Katalysatorlösung wird hergestellt indem zu einer Lösung von 17,1 g
Tetrabutylammoniumhydroxid in 14 g Wasser 42,8 g Diethylcarbonat und 26,1 g i-Propanol
gegeben werden.
Beispielrezeptur 1: Klarlack
Substanz |
Menge [Gew.-%] |
Bindemittelkomponente |
|
malonatfunktioneller Polyester mit einer Konzentration an aciden Protonen von 5,66
mol/kg bezogen auf den lösemittelfreien Polyester, 85%ig in Butylacetat |
52 |
Di-trimethylolpropantetraacrylat |
23 |
Hexandioldiacrylat |
5,5 |
Bis(1,2,2,6,6-pentamethyl-4-piperidinyl)-sebacat |
3 |
Succinimid |
1,5 |
Methylethylketon |
6 |
Katalysatorkomponente |
|
Katalysatorlösung |
6 |
Isopropanol |
3 |
Beispielrezeptur 2: Basislack
Substanz |
Menge [Gew.-%] |
Bindemittelkomponente 1 |
|
malonatfunktioneller Polyester mit einer Konzentration an aciden Protonen von 5,66
mol/kg bezogen auf den lösemittelfreien Polyester, 85%ig in Butylacetat |
31 |
Titandioxid |
35 |
hochmolekulares Blockcopolymer mit pigmentaffinen Gruppen |
1 |
Bis(1,2,2,6,6-pentamethyl-4-piperidinyl)-sebacat |
1 |
Succinimid |
1 |
Butylacetat |
4, 5 |
Bindemittelkomponente 2 |
|
Ditrimethylolpropantetraacrylat |
14 |
Hexandioldiacrylat |
3 |
Katalysatorkomponente |
|
Katalysatorlösung |
3, 5 |
Isopropanol |
2 |
Methylethylketon |
4 |
[0048] Für eine Beurteilung der Lagerstabilität der erfindungsgemäßen Beschichtungsstoffe
wurden Topfzeit und Trockungszeit der Beispielrezeptur 2 bestimmt. Dabei wurden jeweils
Proben nach 1 Tag Lagerung bei 23 °C, nach 28 Tage Lagerung bei 40 °C und nach 1 Jahr
Lagerung bei 20 bis 23 °C geprüft bzw. zur Herstellung einer Beschichtung eingesetzt.
[0049] Bestimmung der Topfzeit: Die Topfzeit wird mit Hilfe eines Auslaufbechers bestimmt.
Bei diesem Verfahren wird eine Flüssigkeit in einen Becher mit definiertem Volumen
gefüllt, der in seinem Boden eine definierte Düse aufweist. Der Beschichtungsstoff
läuft durch die Düse aus, wobei die Zeit vom Austritt an bis zum Abriss des Flüssigkeitsstrahls
gemessen als Auslaufzeit gemessen wird. Sämtliche Vorbereitung und Messungen werden
bei einer Temperatur von 23 °C durchgeführt. Zunächst werden alle Komponenten des
Beschichtungsstoffs vermischt und sofort die Auslaufzeit der Mischung gemessen (Start-Auslaufzeit).
Die Messung wird in regelmäßigen Zeitabständen wiederholt. Das Ende der Topfzeit ist
erreicht, wenn die Auslaufzeit das Doppelte der Startauslaufzeit aufweist.
[0050] Bestimmung der Trocknungszeit: Zur Bestimmung der Trocknungszeit wird ein Trocknungsrecorder,
Trocknungszeitmessgerät der Firma BYK Gardener, eingesetzt. Hierbei wird der zu untersuchende
Beschichtungsstoff mit Hilfe eines Filmziehers gleichmäßig auf Glasstreifen appliziert.
Die Glasstreifen werden anschließend in einen linearen Recorder gelegt. Dann werden
Nadeln auf die Beschichtung aufgesetzt und mit einer definierten, konstanten Geschwindigkeit
über den trocknenden Film gezogen. Dabei entsteht ein charakteristisches Trocknungsbild
der Beschichtung, in dem die einzelnen Zeitabschnitte die unterschiedlichen Härtungsstadien
zeigen: Verlauf oder Offenzeit, Grundspur, Filmaufriss und Oberflächenspur. Die Aushärtung
des Beschichtungsstoffs beginnt dabei mit dem Ende der Offenzeit, d.h. in dem Zeitpunkt,
an dem die durch die Nadel in den applizierten Film geritzte Spur sichtbar bleibt.
Sie endet mit der Oberflächenspur, d.h. in dem Zeitpunkt, an dem die Nadel keine sichtbar
Spur mehr im applizierten Film hinterlässt.
[0051] Zur Beurteilung Lagerstabilität des Beschichtungsstoffs wurden auch die Eigenschaften
der Beschichtungen, die aus unterschiedlich gelagerten Beschichtungsstoffen der Beispielrezeptur
2 hergestellt wurden, untersucht. Hierzu wurden Glanz und Bruchdehnung bestimmt. Es
wurden jeweils Proben nach 1 Tag Lagerung bei 23 °C, nach 28 Tagen Lagerung bei 40
°C und nach 1 Jahr Lagerung bei 20 bis 23 °C zur Herstellung einer Beschichtung eingesetzt.
Zur Herstellung der Probekörper wurde Beispielrezeptur 2 auf grundierte Aluminiumplatten
mittels Becherpistole appliziert und bei Raumtemperatur ausgehärtet.
[0052] Bestimmung des Oberflächenglanzes: Der Glanz der Beschichtungsoberfläche wird als
Reflektometerwert bestimmt. Der Reflektometerwert einer Probe ist definiert als das
Verhältnis der von der Probenoberfläche und einer Glasoberfläche mit der Brechzahl
1,567 in Spiegelrichtung reflektierten Lichtströme. Die Messwerte werden mit Hilfe
eines üblichen Reflektometers im Winkel 60° bestimmt.
[0053] Bestimmung der Bruchdehnung: Die Bruchdehnung wird über Dornbiegeversuch bestimmt.
Dazu werden die Probekörper, um einen Dorn gebogen. Je kleiner der Radius des Dorns,
um den die Platte ohne eine Beschädigung oder Bruch der Beschichtung gebogen werden
kann, desto größer ist die Bruchdehnung der Beschichtung. Als Messwert wird der Durchmesser
des Dorns angegeben.
Tabelle: Lagerstabilität Beispielrezeptur 2
Lagerung |
1 Tag, 24°C |
28 Tage, 40°C |
1 Jahr, 20 - 23 °C |
Topfzeit |
2,5 h |
2,5 h |
2,5 h |
Offenzeit |
59 min |
60 min |
56 min |
Ende Oberflächenspur |
136 min |
132 min |
128 min |
Bruchdehnung |
12 mm |
12 mm |
12 mm |
Glanz |
87 |
88 |
87 |
[0054] Wie die Tabelle zeigt, weisen die erfindungsgemäßen Beschichtungsstoffe eine hohe
Lagerstabilitität auf. Nach einer längeren Lagerung bei erhöhter Temperatur zeigen
die Beschichtungsstoffe selbst keine Verschlechterung ihrer Verarbeitbarkeit. Auch
die daraus hergestellten Beschichtungen zeigen keine Beeinträchtigungen ihrer Eigenschaften.
1. Beschichtungstoff zur Herstellung einer Beschichtung aufweisend zumindest
- 15 bis 70 Gew.-% ein oder mehrere CH-acide Verbindungen A, ausgewählt aus Verbindungen
der Formel
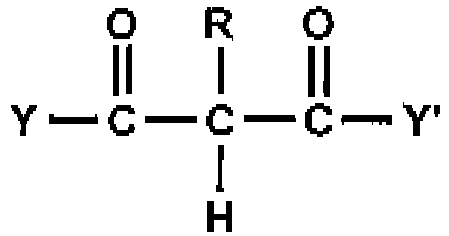
wobei
R Wasserstoff, ein Alkyl- oder Arylrest,
Y ein Alkyl-, Aralkyl-, Aryl-, Alkoxy-Rest oder eine Aminogruppe und,
Y' ein Alkyl-, Aralkyl-, Aryl-, Alkoxy-Rest oder eine Aminogruppe ist,
- 4 bis 40 Gew.-% ein oder mehrere vinyloge Carbonylverbindungen B aus gewählt aus
Acrylaten und Maleaten,
- 0,1 bis 15 Gew.-% ein oder mehrere latent-basische Katalysatoren C,
- 0,00001 bis 10 Gew.-% ein oder mehrere Lichtschutzmittel, welche ausgewählt sind
aus der Gruppe enthaltend Radikalfänger, UV-Absorber, Quencher und Peroxidzersetzer,
- 0,00001 bis 20 Gew.-% ein oder mehrere Offenzeit-Verlängerer, welche ausgewählt
sind aus der Gruppe enthaltend basische NH-funktionelle Verbindungen mit pKa-Werten
zwischen 4 und 14, und,
- 0,00001 bis 20 Gew.-% ein oder mehrere Topfzeit-Verlängerer, welche ausgewählt sind
aus der Gruppe enthaltend Alkohole mit bis zu 6 Kohlenstoffatomen und Verdunstungszahlen
unter 35 aufweisen.
jeweils bezogen auf die Gesamtmenge des Beschichtungsstoffs.
2. Beschichtungstoff nach Anspruch 1, dadurch gekennzeichnet, dass er weiterhin bis zu 70 Gew.-% ein oder mehrere anorganische und/oder organische Pigmente
aufweist.
3. Beschichtungsstoff nach Anspruch 2, dadurch gekennzeichnet, dass die Pigmente ausgewählt sind aus der Gruppe enthaltend Titandioxid, Eisenoxide, Chromoxide,
Chromtitanate, Bismutvanadat, Cobaltblau, Ruße, Pigment Yellow 151, Pigment Yellow
213, Pigment Yellow 83, Pigment Orange 67, Pigment Orange 62, Pigment Orange 36, Pigment
Red 170, Pigment Violet 19, Pigment Violet 23, Pigment Blue 15:3, Pigment Blue 15:6
und Pigment Green 7.
4. Beschichtungsstoff nach einem der voranstehenden Ansprüche,
dadurch gekennzeichnet, dass die Katalysatoren C substituierte Carbonsäuresalze der Formel

sind, worin
R Wasserstoff, Alkyl- oder Aralkyl- oder ein Polymer-Rest ist,
X+ ein Alkali- oder Erdalkalimetall-Kation, ein quaternäres Ammonium- oder Phosphoniumsalz
der Formel (R')4Y+ ist,
worin
Y Stickstoff oder Phosphor ist,
R' gleich oder verschieden, Wasserstoff, Alkyl-, Aral- oder Aralkyl- oder ein Polymer
ist
und worin R und R' eine Ringstruktur bilden oder ein Polymer sind.
5. Beschichtungsstoff nach einem der voranstehenden Ansprüche, dadurch gekennzeichnet, dass die Lichtschutzmittel substituierte 2,2,6,6-Tetramethylpiperidine, 2-Hydroxyphenylbenztriazole,
2-Hydroxybenzophenone, 2-Hydroxyphenyltriazine, Oxalanilide, organische Nickelverbindungen,
Thioether oder/oder Phosphite sind.
6. Beschichtungsstoff nach einem der voranstehenden Ansprüche, dadurch kennzeichnet, dass der Beschichtungsstoff 0,5 bis 5, bevorzugt 1 bis 3 Gew.-% Lichtschutzmittel bezogen
auf die Gesamtmenge des Beschichtungsstoffs aufweist.
7. Beschichtungsstoff nach einem der voranstehenden Ansprüche, dadurch gekennzeichnet, dass die Topfzeit-Verlängerer Alkohole mit bis zu 4 Kohlenstoffatomen sind.
8. Beschichtungsstoff nach einem der voranstehenden Ansprüche, dadurch kennzeichnet, dass der Beschichtungsstoff 0,01 bis 15, bevorzugt 0,1 bis 10 Gew.-% Topfzeit-Verlängerer
bezogen auf die Gesamtmenge des Beschichtungsstoffs aufweist.
9. Beschichtungsstoff nach einem der voranstehenden Ansprüche, dadurch gekennzeichnet, dass die Offenzeit-Verlängerer Succinimide, 1,2,4,-Triazole, 1,2,3,-Benzotriazole, 5,5-Diphenylhydantoine,
Hydantoine und/oder (RS)-3-Ethyl-3-methylpyrrolidin-2,5-dion sind.
10. Beschichtungsstoff nach einem der voranstehenden Ansprüche, dadurch kennzeichnet, dass der Beschichtungsstoff 0,01 bis 10, bevorzugt 0,1 bis 5 Gew.-% Offenzeit-Verlängerer
bezogen auf die Gesamtmenge des Beschichtungsstoffs aufweist.
11. Beschichtungsstoff nach einem der voranstehen Ansprüche, dadurch gekennzeichnet, dass der Beschichtungsstoff weiterhin bis zu 25 Gew.-% ein oder mehrere Dispergieradditive
aufweist.
12. Beschichtungsstoff nach einem der voranstehenden Ansprüche, dadurch gekennzeichnet, dass der Beschichtungsstoff weiterhin bis zu 60 Gew.-% ein oder mehrere funktionale Füllstoffe
aufweist.
13. Beschichtungsstoff nach einem der voranstehenden Ansprüche, dadurch gekennzeichnet, dass der Beschichtungsstoff weiterhin bis zu 50 Gew.-% ein oder mehrere aprotische Lösemittel
aufweist.
14. Verwendung des Beschichtungsstoffs nach einem der Ansprüche 1 bis 13 zur Herstellung
zumindest einer Beschichtung in einem Beschichtungssystem.
15. Verwendung nach Anspruch 14 dadurch gekennzeichnet, dass zumindest ein Basislack hergestellt ist aus einem Beschichtungsstoff nach einem der
Ansprüche 2 bis 13.
16. Verwendung nach Anspruch 14, dadurch gekennzeichnet, dass zumindest ein Klarlack hergestellt ist aus einem Beschichtungstoff nach einem der
Ansprüche 1 und 4 bis 13.
17. Verfahren zur Beschichtung eines Bauteils aufweisend die Schritte (a) Applizieren
eines Beschichtungsstoffs nach einem der Ansprüche 1 bis 13 auf ein Substrat und (b)
Aushärten der applizierten Schicht bei Temperaturen zwischen 5 und 45 °C über einen
Zeitraum von 1 bis 12 Stunden.
18. Verfahren nach Anspruch 17, dadurch gekennzeichnet, dass der Beschichtungsstoff in Schritt (a) mittels Sprühverfahren appliziert wird.
19. Bauteil beschichtet mit zumindest einer Beschichtung hergestellt aus einem Beschichtungsstoff
nach einem der Ansprüche 1 bis 13.
20. Bauteil nach Anspruch 19, dadurch gekennzeichnet, dass das Bauteil ein Schienenfahrzeugbauteil oder Luftfahrzeugbauteil ist.
1. Coating material for the production of a coating containing at least
- 15 to 70 % by weight of at least one CH-acidic compound A selected from compounds
of the formula

with
R being hydrogen, an alkyl group or aryl group,
Y being an alkyl group, aralkyl group, aryl group, alkoxy group or an amino group,
and with
Y' being an alkyl group, aralkyl group, aryl group, alkoxy group or an amino group,
- 4 to 40 % by weight of at least one vinylogous carbonyl compound B selected from
acrylates and maleates,
- 0.1 to 15 % by weight of at least one latent base catalyst C,
- 0.00001 to 10 % by weight of at least one light stabilizer selected from the group
comprising free-radical scavengers, UV absorbers, quenching agents and peroxide decomposers,
- 0.00001 to 20 % by weight of at least one open-time extender selected from the group
comprising basic NH functional compounds with a pKa value of between 4 and 14, and,
- 0.00001 to 20 % by weight of at least one pot life extender selected from the group
comprising alcohols with up to 6 carbon atoms, and showing an evaporation number of
below 35.
each based on the total quantity of the coating material.
2. Coating material as defined in claim 1, characterized in that it furthermore contains up to 70 % by weight of at least one inorganic and/or organic
pigment.
3. Coating material as defined in claim 2, characterized in that the pigments are selected from the group comprising titanium dioxide, iron oxides,
chromium oxides, chromium titanates, bismuth vanadate, cobalt blue, carbon blacks,
pigment yellow 151, pigment yellow 213, pigment yellow 83, pigment orange 67, pigment
orange 62, pigment orange 36, pigment red 170, pigment violet 19, pigment violet 23,
pigment blue 15:3, pigment blue 15:6 and pigment green 7.
4. Coating material as defined in one of the preceding claims,
characterized in that the catalysts C are substituted carboxylic acid salts of the formula
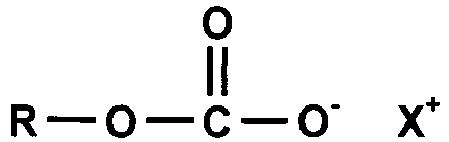
wherein
R is hydrogen, an alkyl group or aralkyl group or a polymer group,
X+ is an alkali metal cation, an alkaline earth metal cation or a quaternary ammonium
salt or phosphonium salt of the formula (R')4Y+,
wherein
Y is nitrogen or phosphorus,
R' is the same or different, is hydrogen, an alkyl group, an aryl group or an aralkyl
group or a polymer
and wherein R and R' form a ring structure or are a polymer.
5. Coating material as defined in one of the preceding claims, characterized in that the light stabilizers are substituted 2,2,6,6-tetramethylpiperidines, 2-hydroxyphenyl
benzotriazoles, 2-hydroxybenzophenones, 2-hydroxyphenyltriazines, oxalanilides, organic
nickel compounds, thioethers and/or phosphites.
6. Coating material as defined in one of the preceding claims, characterized in that the coating material contains 0.5 to 5 % by weight, preferably 1 to 3 % by weight,
of light stabilizers, based on the total quantity of the coating material.
7. Coating material as defined in one of the preceding claims, characterized in that the pot-life extenders are alcohols with up to 4 carbon atoms.
8. Coating material as defined in one of the preceding claims, characterized in that the coating material contains 0.01 to 15 % by weight, preferably 0.1 to 10 % by weight,
of pot-life extenders, based on the total quantity of the coating material.
9. Coating material as defined in one of the preceding claims, characterized in that the open-time extenders are succinimides, 1,2,4,-triazoles, 1,2,3,-benzotriazoles,
5,5-diphenylhydantoins, hydantoins and/or (RS)-3-ethyl-3-methylpyrrolidine-2,5-dione.
10. Coating material as defined in one of the preceding claims, characterized in that the coating material contains 0.01 to 10 % by weight, preferably 0,1 to 5 % by weight,
of open-time extenders, based on the total quantity of the coating material.
11. Coating material as defined in one of the preceding claims, characterized in that the coating material furthermore contains up to 25 % by weight of at least one dispersing
additive.
12. Coating material as defined in one of the preceding claims, characterized in that the coating material furthermore contains up to 60 % by weight of at least one functional
filler.
13. Coating material as defined in one of the preceding claims, characterized in that the coating material furthermore contains up to 50 % by weight of at least one aprotic
solvent.
14. Use of the coating material as defined in any one of claims 1 to 13 for the production
of at least one coating in a coating system.
15. Use as defined in claim 14, characterized in that at least one base coat is produced from a coating material as defined in any one
of claims 2 to 13.
16. Use as defined in claim 14, characterized in that at least one transparent lacquer is produced from a coating material as defined in
any one of claims 1 and 4 to 13.
17. Method for coating a component, the method comprising the steps a) applying the coating
material as defined in any one of claims 1 to 13 to a substrate and (b) curing the
applied layer for a duration of 1 to 12 hours at a temperature of between 5 and 45
°C.
18. Method as defined in claim 17, characterized in that the coating material in step (a) is applied by means of a spraying method.
19. Component coated with at least one coating produced from a coating material as defined
in any one of claims 1 to 13.
20. Component as defined in claim 19, characterized in that the component is a rail vehicle component or an aircraft component.
1. Matériau de revêtement pour la production d'un revêtement contenant au moins
- 15 à 70 % en poids d'un ou de plusieurs composés acides CH A étant choisis parmi
les composés de la formule

où
R représente l'hydrogène, un radical alkyle ou aryle,
Y représente un radical alkyle, aralkyle, aryle, alkoxy ou un groupe amino et,
Y' représente un radical alkyle, aralkyle, aryle, alkoxy ou un groupe amino,
- 4 à 40 % en poids d'un ou de plusieurs composés carbonyles vinylogues B étant choisis
parmi les acrylates et les maléates,
- 0,1 à 15 % en poids d'un ou de plusieurs catalyseurs basiques latents C,
- 0,00001 à 10 % en poids d'un ou de plusieurs stabilisants lumière étant choisis
dans le groupe comprenant les capteurs de radicaux libres, les absorbants de la lumière
UV, les quenchers et les agents décomposant les peroxydes,
- 0,00001 à 20 % en poids d'un ou de plusieurs agents prolongeant le temps ouvert
étant choisis dans le groupe comprenant les composés basiques à fonction NH ayant
une valeur de pKa entre 4 et 14, et,
- 0,00001 à 20 % d'un ou de plusieurs agents prolongeant la durée de vie en pot étant
choisis dans le groupe comprenant les alcools ayant jusqu'à 6 atomes de carbone et
ayant un indice d'évaporation inférieur à 35, chaque quantité étant exprimée par rapport
à la quantité totale du matériau de revêtement.
2. Matériau de revêtement selon la revendication 1, charactérisé en ce qu'il contient
en outre jusqu'à 70 % en poids d'un ou de plusieurs pigments inorganiques et/ou pigments
organiques.
3. Matériau de revêtement selon la revendication 2, charactérisé en ce que les pigments
sont choisis dans le groupe comprenant le dioxyde de titane, les oxydes de fer, les
oxydes de chrome, les titanates de chrome, le vanadate de bismuth, le bleu de cobalt,
les noirs de carbone, le Pigment Yellow 151, le Pigment Yellow 213, le Pigment Yellow
83, le Pigment Orange 67, le Pigment Orange 62, le Pigment Orange 36, le Pigment Red
170, le Pigment Violet 19, le Pigment Violet 23, le Pigment Blue 15:3, le Pigment
Blue 15:6 et le Pigment Green 7.
4. Matériau de revêtement selon l'une des revendications précédentes, charactérisé en
ce que les catalyseurs C sont des sels d'acides carboxyliques substitués de la formule
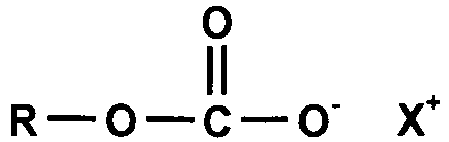
où
R représente l'hydrogène, un radical alkyle ou aralkyle ou un radical polymère,
X+ représente un cation de métal alcalin ou un cation de métal alcalino-terreux, un
sel d'ammonium quaternaire ou un sel de phosphonium quaternaire de la formule (R')4Y+,
où
Y représente l'azote ou le phosphore,
R' est identique ou différent, est l'hydrogène, un radical alkyle, aryle ou aralkyle
ou un polymère
et où R et R' forment une structure cyclique ou sont un polymère.
5. Matériau de revêtement selon l'une des revendications précédentes, charactérisé en
ce que les stabilisants lumière sont des 2,2,6,6-tétraméthylpipéridines substituées,
des 2-hydroxyphénylbenzotriazoles, des 2-hydroxybenzophénones, des 2-hydroxyphényltriazines,
des oxalanilides, des composés de nickel organiques, des thioéthers et/ou des phosphites.
6. Matériau de revêtement selon l'une des revendications précédentes, charactérisé en
ce que le matériau de revêtement contient 0,5 à 5 % en poids, de préférence 1 à 3
% en poids, de stabilisants de lumière, chaque quantité étant exprimée par rapport
à la quantité totale du matériau de revêtement.
7. Matériau de revêtement selon l'une des revendications précédentes, charactérisé en
ce que les agents prolongeant la durée de vie en pot sont des alcools ayant jusqu'à
4 atomes de carbone.
8. Matériau de revêtement selon l'une des revendications précédentes, charactérisé en
ce que le matériau de revêtement contient 0,01 à 15 % en poids, de préférence 0,1
à 10 % en poids, d'agents prolongeant la durée de vie en pot, chaque quantité étant
exprimée par rapport à la quantité totale du matériau de revêtement.
9. Matériau de revêtement selon l'une des revendications précédentes, charactérisé en
ce que les agents prolongeant le temps ouvert sont des succinimides, des 1,2,4,-triazoles,
des 1,2,3,-benzotriazoles, des 5,5-diphénylhydantoines, des hydantoines et/ou une(RS)-3-éthyl-3-méthylpyrrolidine-2,5-dione.
10. Matériau de revêtement selon l'une des revendications précédentes, charactérisé en
ce que le matériau de revêtement contient 0,01 à 10 % en poids, de préférence 0,1
à 5 % en poids, d'agents prolongeant le temps ouvert, chaque quantité étant exprimée
par rapport à la quantité totale du matériau de revêtement.
11. Matériau de revêtement selon l'une des revendications précédentes, charactérisé en
ce que le matériau de revêtement contient en outre jusqu'à 25 % en poids d'un ou de
plusieurs additifs de dispersion.
12. Matériau de revêtement selon l'une des revendications précédentes, charactérisé en
ce que le matériau de revêtement contient en outre jusqu'à 60 % en poids d'un ou de
plusieurs matières de charge fonctionnelles.
13. Matériau de revêtement selon l'une des revendications précédentes, charactérisé en
ce que le matériau de revêtement contient en outre jusqu'à 50 % en poids d'un ou de
plusieurs solvants aprotiques.
14. Utilisation du matériau de revêtement selon l'une quelconque des revendications 1
à 13 pour la production d'au moins un revêtement dans un système de revêtement.
15. Utilisation selon la revendication 14, charactérisée en ce qu'au moins une laque de
base est produite d'un matériau de revêtement selon l'une quelconque des revendications
2 à 13.
16. Utilisation selon la revendication 14, charactérisée en ce qu'au moins une laque transparente
est produite d'un matériau de revêtement selon l'une quelconque des revendications
1 et 4 à 13.
17. Procédé pour le revêtement d'un composant comprenant les étapes suivantes: (a) application
d'un matériau de revêtement selon l'une quelconque des revendications 1 à 13 sur un
substrat et (b) durcissement de la couche appliquée à une température comprise entre
5 et 45 °C pour une durée de 1 à 12 heures.
18. Procédé selon la revendication 17, charactérisé en ce que le matériau de revêtement
est appliqué par procédé de pulvérisation dans l'étape (a).
19. Composant revêtu d'au moins un revêtement produit d'un matériau de revêtement selon
l'une quelconque des revendications 1 à 13.
20. Composant selon la revendication 19, charactérisé en ce que le composant est un composant
d'une véhicule sur rails ou un composant d'un aéronef.