[0001] This invention relates to the scouring of raw wool, ie wool which contains large
quantities of wool grease, which wool is usually subjected to the scouring process
before a carding operation.
[0002] Raw wool contaminants consist mainly of grease, suint and particulate soil. Suint
is mostly a mixture of inorganic salts from evaporation of sheep sweat. The grease
component is a very complex mixture containing fats, fatty acids and triglycerides.
The particulate soil is, for example, dust, dirt and skin debris. The contaminants
tend to divide themselves into "easy-to-remove" and "hard-to-remove" contaminants;
see B.O. Bateup, Proceedings of the CSIRO Division of Textile Industry, Symposium
on Wool Scouring and and Worsted Carding: New Approaches (1986), page 8.
[0003] Typically, the aim of wool scouring is to reduce the "extractables" (contaminants
that can be extracted into dichloromethane, DCM) to a level between 0.3-0.5% and at
the same time provide a wool having good whiteness, ie a low degree of yellowness.
[0004] Very low levels of extractables are not required as a small amount of residual wool
grease helps in the subsequent processing of the wool through the mill; very clean
wool is brittle and will tend to break if processed at high speeds, thus reducing
total output rate.
[0005] Raw wool is generally scoured by washing it in a hot solution of detergent to remove
the contaminants followed by rinsing in slightly cooler water. The clean wool is then
dried by passing it through a hot air dryer before being passed onto the next processing
stage.
[0006] This scouring process is preferably carried out continuously by passing the wool
through a series of "bowls". Preferably, wool passes from bowl to bowl in one direction,
and liquor is pumped in the opposite direction. The raw wool enters the first bowl,
and becomes cleaner as it moves towards the last. Clean water enters the last bowl
and becomes dirtier as it moves towards the first. The quantities and nature of the
chemicals added to the various bowls have been the subject of much work over the last
few years. Raw wool has a high level of contaminants (up to 30% by weight) and this
raises significant effluent disposable problems. Much of the recent work, especially
in Australia, has concentrated on producing more easily treated effluent rather than
on improving the efficiency of the scouring process itself. A review of this work
has been published by J.R. Christoe and B.O. Bateup, Wool Science Review (1987),
64, 25.
[0007] A conventional scouring system consists of two or three scouring bowls, followed
by two or three rinse bowls, depending upon the numbers of bowls, typically 46, in
the range. The rate of water addition depends on the volume and type of wool being
processed.
Introduction of clean water dilutes the active material in the bowls, so addition
of fresh detergent and any other chemicals present (see below) are made discontinuously
by hand (for example, every half hour), or continuously by means of an automatic dosing
pump. The amount of detergent added to the various scouring bowls varies from high
levels in bowl 1 to very low levels in bowl 3. This is because, as the wool becomes
cleaner, less detergent is required to solubilise the contaminants. Wool grease melts
at around 40-45°C, so in the conventional scouring system, a typical temperature for
bowl 1 is in the region 65-70°C, so that the hot first bowl softens the grease and
allows penetration of the grease droplets by the detergent. The temperature can then
be gradually decreased on progression from bowl 3 (about 60°C) dropping to about 55°C
for bowls 4 and 5.
[0008] In the simplest system, the only added chemical is the detergent. However, several
workers have proposed the addition of so-called "builders" to the above system. Builders
are compounds, usually inorganic salts, added to increase the effectiveness of the
detergent (see the article by Bateup, supra). Thus, scour liquor often contains free
calcium and/or magnesium originally present in any of the water used for scouring,
the suint salts and possibly lime deposited on the wool itself. In particular, the
wool may be so called "slipe" wool, or may be a blend containing such wool, this being
wool removed from the hide of a dead sheep using lime. Often, a wool scourer will
not know whether a particular batch to be scoured contains such slipe wool. The builders
assist in removal of such unwanted calcium and/or magnesium from the scour liquor,
and from the surface of the wool. Sodium sulphate is often used as a builder, but
its value remains questionable where, as is usual, the detergents used are exclusively
non-ionic.
[0009] Another builder which is often used is sodium carbonate, often in the form of soda
ash. This does effectively remove calcium. However, its calcium binding capacity and
its rate of binding calcium is limited. Sodium silicate acts as a much better builder,
but is highly alkaline and may cause wool damage if present at too high a concentration.
Similarly, sodium hydroxide may be used as a builder, but with the same disadvantage;
see B.O. Bateup, Textile Research Journal (January 1985),
55, 50. The best calcium binders are sodium tripolyphosphate (STP) and zeolites, but
these are expensive in comparison with the builders mentioned above.
[0010] In addition to the detergents and builders, it is also possible to include, for example,
metal ion sequestrants (which can also be called "builders"), for example citrates,
ethylene diamine tetraacetic acid (EDTA) and nitrilotriacetic acid (NTA) in the final
rinse bowl to increase the whiteness of the scoured wool; see B.O. Bateup, Text. Res.
J. (1985),
55, 50.
[0011] A conventional wool scouring system may utilise five bowls in the order: detergent,
detergent, mild detergent (or rinse), rinse, rinse. However, there are several modifications
to this system, many of which are described in the abovementioned review by Christoe
and Bateup, Wool Science Review (1987)
64, 25. One such modification is known as multi-stage scouring in which, for a five
bowl system, the order of the bowls is: detergent, rinse, detergent, rinse, rinse.
The role of the first bowl is to remove the particulate salts and the more easily
removed grease and suint salts, while the second bowl, also at 65°C, continues to
soften the wool grease before the wool is reintroduced to a detergent solution to
effect removal of this grease. It is generally accepted that two rinse bowls are required
at the end of the cycle, so the system is in practice applicable only to five or six
bowl ranges.
[0012] Another modification is the use of a so-called "suint bowl". In one system, this
consists merely of cold, or slightly warm water at a temperature well below the melting
point of the wool grease; see for example, US-A-2552944. Here, the cold water which
contains no additives, merely removes suint, which itself has, in its own right, a
detergent effect and allows this to contribute to removal of wool grease in the subsequent
detergent stages. In order to improve the efficiency of dirt removal (by improving
dirt settling efficiency), it is known to include in the cold suint bowl a builder,
for example soda ash or sodium metasilicate, or a low concentration of a non-ionic,
anionic or cold water laundry detergent; see C.A. Anderson et al, Proc. 7th Int. Wool
Text Conf., Tokyo (1985)
5, 255, and B.O. Bateup and J.J. Warner, Text. Res. J. (1986),
56, 489.
[0013] In another modification, a hot suint bowl is used, which contains no chemicals. The
bowl order is thus: suint bowl, detergent, detergent, rinse, rinse. Here the hot suint
bowl is used to remove particulate soils and soluble suint salts. It also allows the
wool grease to be softened by the hot water before coming into contact with the detergent
in the main scouring bowl. As with the abovementioned multistage scouring, the requirement
for two rinse bowls usually means that this system requires five or six bowls in total.
[0014] Some scourers, especially those with six bowl ranges, have used a combination of
the above to give a bowl configuration of (cold) suint bowl, detergent, rinse, detergent,
rinse, rinse. It is considered that the late introduction of detergent into the system
allows for greater softening of the wool grease, especially wool grease containing
coloured impurities and so gives the scoured product a much better (ie less yellow)
colour.
[0015] Each of US-A-2655428 and US-A-2629723 describes a three-stage system in which the
suint alone is effectively employed as scouring agent, and a neutral, polar, oxygen
containing organic compound and preferably a neutral electrolyte is added to enhance
the effectiveness of the suint in emulsifying the wool grease. Thus, for example,
wool is agitated in an aqueous solution containing 2% normal butanol and sodium chloride
while maintaining the temperature at 60°C. The wool is then squeezed free of the solution
and rewashed in a fresh batch of the same solution at the same temperature. The wool
is then again squeezed free of the solution, washed with water and dried. However,
the scouring efficiency of the suint above has not proved sufficient for the process
to achieve at least widespread commercial acceptance.
[0016] We have developed a scouring process which, as compared with conventional wool scouring
processes, is capable of providing an improved whiteness while maintaining acceptably
low values of residual wool grease.
[0017] Surprisingly, we have found that this improvement can be achieved by including, prior
to a detergent scouring step, a hot de-suinting step in which the de-suinting liquor
contains a builder.
[0018] Thus, the present invention provides a method of scouring raw wool comprising the
steps of (a) treating the wool with an aqueous medium containing a building agent
capable of reducing the level of free calcium and/or magnesium therein and having
a temperature of at least 45°C and thereafter (b) treating the wool with an aqueous
medium having a pH of at least 8, containing a detergent and having a temperature
of at least 45°C.
[0019] Preferably, the temperature of the aqueous medium in step (a), namely the hot de-suinting
liquor, lies between 45-75°C, more preferably 60-70°C.
[0020] The pH of the hot de-suinting liquor is preferably at least 8, more preferably from
8-10.5, especially 9-10.
[0021] Builders which may be used in a method embodying the invention may be inorganic or
organic builders.
[0022] Examples of inorganic detergency builders include water-soluble alkali metal carbonates,
bicarbonates, silicates and crystalline and amorphous aluminosilicates. Specific examples
include sodium carbonate (with or without calcite seeds), potassium carbonates, sodium
and potassium bicarbonates and silicates.
[0023] Examples of phosphorus-containing inorganic detergency builders in particular include
water-soluble salts, especially alkali metal pyrophosphates, orthophosphates and polyphosphates.
Specific examples of inorganic phosphate builders include sodium and potassium tripolyphosphates,
phosphates and hexametaphosphates.
[0024] Examples of organic detergency builders include the alkali metal, ammonium and substituted
ammonium polyacetates, carboxylates, polycarboxylates, polyacetal carboxylates and
polyhydroxysulphonates. Specific examples include sodium, potassium, lithium, ammonium
and substituted ammonium salts of ethylenediaminetetraacetic acid, nitrilotriacetic
acid, oxydissuccinic acid, melitic acid, benezene polycarboxylic acids and citric
acid.
[0025] Typical examples of the above are ethylene diamine tetraacetic acid (EDTA), nitrilotriacetic
acid (NTA), citrates, zeolites, sodium tripolyphosphate, sodium carbonate and sodium
silicate, though for those builders providing an acid pH, a compound capable of providing
a pH of at least 8 is preferably added.
[0026] However, a preferred builder, in addition to its role in removing free calcium and/or
magnesium from the aqueous medium, is preferably also capable of controlling the pH
of the de-suinting liquor to provide a pH of at least 8.
[0027] More preferably the builder comprises at least one inorganic ionic compound, especially
a mixture of inorganic ionic compounds, more especially a mixture of an alkali metal,
for example sodium, carbonate and an alkali metal, for example sodium, silicate, preferably
in a proportional amount such as to provide a sodium silicate:sodium carbonate weight
ratio of from 20:80 to 80:20, more preferably 30:70 to 50:50, especially about 40:60.
[0028] Preferably, the builder concentration in step (a) is at least 0.2g/l and more preferably
lies within the range from 0.5-10g/l, especially 1-5 g/l, more especially about 2
g/l.
[0029] A preferred liquor to fibre ratio is from 60:1 to 90:1, especially 75:1 to 85:1,
more especially about 80:1.
[0030] In a preferred method, the preliminary de-suinting step (a) is followed by a detergent
scouring step (b) in which the detergent composition contains the same builder as
that employed in the de-suinting step, though preferably at a lower concentration,
more preferably 0.1-1 g/l, especially 0.3-0.7 g/l, more especially 0.5 g/l.
[0031] Because of the oily mixture of wool grease, its removal is best effected by the use
of a non-ionic, rather than an anionic, surfactant.
[0032] Examples of suitable nonionic surfactants that can be included in the detergent active
system include:
1. The polyethylene oxide condensates of alkyl phenol, eg. the condensation products
of alkyl phenols having an alkyl group containing from 6 to 12 carbon atoms in either
a straight chain or branched chain configuration, with ethylene oxide, the said ethylene
oxide being present in amounts equal to 3 to 30, preferably 5 to 14 moles of ethylene
oxide per mole of alkyl phenol. The alkyl substituent in such compounds may be derived,
for example, from polymerised propylene, di-isobutylene, octene and nonene. Other
examples include dodecylphenol condensed with 9 moles of ethylene oxide per mole of
phenol; dinonylphenol condensed with 11 moles of ethylene oxide per mole of phenol;
and nonylphenol and diisooctylphenol condensed with 13 moles of ethylene oxide.
2. The condensation product of primary or secondary aliphatic alcohols having 8 to
24 carbon atoms, in either straight chain or branched chain configuration, with from
2 to about 40 moles, preferably 2 to about 9 moles of ethylene oxide per mole of alcohol.
Preferably, the aliphatic alcohol comprises between 9 and 18 carbon atoms and is ethoxylated
with between 2 and 9, desirably between 3 and 8, moles of ethylene oxide per mole
of aliphatic alcohol. The preferred surfactants are prepared from primary alcohols
which are either linear (such as those derived from natural fats) or prepared by the
Ziegler process from ethylene, eg. such as the Lutensols, Dobanols and Neodols which
have about 25% 2-methyl branching (Lutensol being a Trade Name of BASF, Dobanol and
Neodol being Trade Names of Shell), or Synperonics, which are understood to have about
50% 2-methyl branching (Synperonic is a Trade Name of ICI) or the primary alcohols
having more than 50% branched chain structure sold under the Trade Name Lial by Liquichimica.
Specific examples of nonionic surfactants falling within the scope of the invention
include Dobanol 45-4, Dobanol 45-7, Dobanol 45-9, Dobanol 91-2.5, Dobanol 91-3, Dobanol
91-4, Dobanol 91-6, Dobanol 91-8, Dobanol 23-6.5, Synperonic 6, Synperonic A7, Synperonic
14, the condensation products of coconut alcohol with an average of between 5 and
12 moles of ethylene oxide per mole of alcohol, the coconut alkyl portion having from
10 to 14 carbon atoms, and the condensation products of tallow alcohol with an average
of between 7 and 12 moles of ethylene oxide per mole of alcohol, the tallow portion
comprising essentially between 16 and 22 carbon atoms. Secondary linear alkyl ethoxylates
are also suitable in methods embodying the present invention, especially those ethoxylates
of the Tergitol series having from about 9 to 15 carbon atoms in the alkyl group and
up to about 11, especially from about 3 to 9, ethoxy residues per molecule.
3. The compound formed by condensing ethylene oxide with a hydrophobic base formed
by the condensation of propylene oxide with propylene glycol. The molecular weight
of the hydrophobic portion generally falls in the range of about 1500 to 1800. Such
synthetic nonionic detergents are available on the market under Trade Name of "Pluronic",
supplied by Wyandotte Chemicals Corporation.
[0033] The detergent active system may comprise a mixture of anionic and nonionic detergents,
in which case the preferred nonionic material or mixtures thereof will have an HLB
(hydrophilic-lipophilic balance) of not more than 10.5, preferably in the range of
from 6 to 10, most preferably in the range of 8 to 9.5. As explained, the detergent
active system can contain one or a mixture of more than one nonionic detergent-active
material. The mixture can contain one or more nonionic materials having an HLB of
more than 10.5, providing the average HLB of the mixture of nonionic materials is
not more than 10.5. The HLB scale is a known measure of hydrophilic-lipophilic balance
in any compound. It is fully defined in the literature, for example in "Nonionic Surfactants",
Volume 1, edited by M J Schick. A method of determining the HLB of a mixture of nonionic
materials is also defined in this reference.
[0034] Preferred nonionic materials are the alkoxylate adducts of fatty compounds selected
from fatty alcohols, fatty acids, fatty esters, fatty amides and fatty amines. The
fatty compound contains at least 10 carbon atoms and the nonionic material contains
an average of less than 8 alkylene oxide groups per molecule.
[0035] Alkylene oxide adducts of fatty alcohols useful in methods embodying the present
invention preferably have the general formula:
R¹⁰-O-(C
nH
2nO)
yH
wherein R¹⁰ is an alkyl or alkenyl group having at least 10 carbon atoms, most preferably
from 10 to 22 carbon atoms, y is preferably not more than 10, such as from 0.5 to
about 3.5, and n is 2 or 3. Examples of such materials include Synperonic A3(ex ICI),
which is a C₁₃- C₁₅ alcohol with about three ethylene oxide groups per molecule, and
Empilan KB3 (ex Marchon) which is lauric alcohol 3EO.
[0036] Alkylene oxide adducts of fatty acids useful in methods embodying the present invention
preferably have the general formula:
R¹⁰-C-O (C
nH
2nO)
yH,
wherein R¹⁰, n and y are as given above. Suitable examples include ESONAL 0334 ( ex
Diamond Shamrock ), which is a tallow fatty acid with about 2.4 ethylene oxide groups
per molecule.
[0037] Alkylene oxide adducts of fatty esters useful in methods embodying the present invention
include adducts of mono-, di- or triesters of polyhydric alcohols containing 1 to
4 carbon atoms; such as coconut or tallow oil (triglyceride) 3EO (ex Stearine Dubois).
[0038] Alyklene oxide adducts of fatty amides useful in methods embodying the present invention
preferably have the general formula:

wherein R¹⁰ is an alkyl or alkenyl group having at least 10 carbon atoms, most preferably
from 10 to 22 carbon atoms, n is 2 or 3 and x and z in total are not more than 4.0,
preferably from about 0.5 to about 3.5, while one of x and z can be zero. Examples
of such materials include tallow monoethanolamide and diethanolamide, and the corresponding
coconut and soya compounds.
[0039] Alkylene oxide adducts of fatty amines useful in methods embodying the present invention
preferably have the general formula:
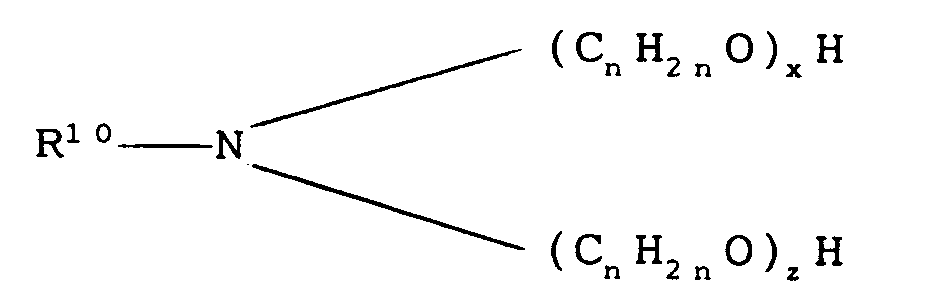
wherein R¹⁰ and n are as given above, and x and z in total are preferably not more
than 4.0, most preferably from about 0.5 to about 3.5. Examples of such materials
include Ethomeen T12 (tallow amine 2EO, available from AKZO), Optameet PC5 (coconut
alkyl amine 5EO) and Crodamet 1.02 (oleylamine 2EO, available from Croda Chemical).
[0040] Cationic detergent-active materials suitable for use herein include quaternary ammonium
surfactants and surfactants of a semi-polar nature, for example amine oxides.
[0041] Amounts of amphoteric or zwitterionic detergent compounds can also be used in a method
embodying the invention, but this is not normally desired owing to their relatively
high cost. If any amphoteric or zwitterionic detergent compounds are used, it is generally
in small quantities relative to the much more commonly used anionic and/or nonionic
detergent-active compounds.
[0042] The detergent is preferably present in a concentration of 0.5 to 10 g/l, especially
1-5 g/l, more especially about 2 g/l.
[0043] A preferred method is carried out continuously, more preferably with the wool and
water travelling in countercurrent flow.
[0044] An especially preferred scouring system includes an additional subsequent detergent
treatment (c), using an aqueous medium at a temperature of at least 45°C, though using
a lower concentration of detergent, preferably 0.1-1, more preferably 0.3-0.7, especially
about 0.5 g/l. Steps (a) to (c) may be carried out successively, though preferably
excess liquor in the wool is removed between the successive stages.
[0045] Typically, a method embodying the invention comprises the successive steps of
(a) treating the wool with an aqueous medium containing a building agent capable of
reducing the level of free calcium and/or magnesium in the aqueous medium, having
a pH of at least 8 and having a temperature of at least 60°C,
(b) treating the wool from step (a) with an aqueous medium having a pH of at least
8 and a temperature of at least 60°C and containing a detergent,
(c) treating the wool from step (b) with an aqueous medium having a temperature of
at least 55°C and containing a detergent,
(d) treating the wool from step (c) with an aqueous medium having a temperature of
at least 50°C to provide a first rinse and
(e) treating the wool from step (d) with an aqueous medium having a temperature of
at least 50°C to provide a second rinse.
[0046] A preferred continuous system for carrying out a method embodying the invention will
now be described with reference to the accompanying drawing, which is a schematic
representation of a continuous countercurrent flow system.
[0047] Thus, the system preferably contains four to six, especially five bowls, indicated
as 1-5 in the drawing. Arrows A and B represent entry of raw wool into and exit of
wool out of the system and arrow E represents the direction of travel of the wool.
Arrow C represents the water inlet and arrow D the water outlet, arrow F representing
the direction of travel of the water. After all of the bowls have been filled with
water and the appropriate detergents and chemicals added, the raw wool is introduced
into bowl 1 and moved along the bowl by a series of rakes suspended above the bowl.
At the end of the bowl, the wool passes up a ramp onto a pair of squeeze rollers which
removes most of the liquor entrained between the wool fibers and so prevents conveyance
of contaminants removed in bowl 1 into bowl 2. At the same time as the wool moves
down the line of bowls, clean water is introduced into bowl 5 and a countercurrent
flow system is used to pump this water back down the line of the bowls.
[0048] The de-suinting operation takes place in bowl 1, preferably at a temperature from
60-70°C, more especially 65°C, and a builder concentration of about 2 g/l. Typically
the builder is a mixture of sodium silicate/sodium carbonate in a ratio of 40/60.
Such a builder is commercially available from Crosfield Textile Chemicals, Warrington,
England, as Croscour P100.
[0049] A first detergent scouring operation is carried out in bowl 2, preferably at a temperature
of from 60-70°C, more especially 65°C, using a non-ionic detergent, typically at a
concentration of 2 g/l and the same builder as that used in bowl 1, but at a lower
concentration of about 0.5 g/l.
[0050] A subsequent detergent treatment is carried out in bowl 3, which contains the same
detergent as bowl 2, but at a lower concentration of about 0.5 g/l and no builder.
The scouring temperature is preferably 55-65, more preferably 60°C.
[0051] In each of bowls 4 and 5, rinsing operations are carried out, using clean water at
a temperature preferably from 40-60°C, more preferably about 55°C.
[0052] Usually, the throughput of wool will be around 1,000 kilo/hour, with a residence
time in each bowl of about 2 mins.
Example
[0053] The following experiment was carried out in order to illustrate the advantages of
a method embodying the invention.
[0054] A 300g batch of English 56's Arran wool was hand blended to ensure an even distribution
of soiling. This 300g was divided into 6 x 50g lots which were then further divided
into 5 x 10g samples. To simulate an industrial scouring range 5 x 1 litre beakers
were used. Each beaker contained 800 ml of water giving a liquor to fibre ratio of
80:1. The temperature of the water in each beaker was as shown in Table 1 below.
[0055] Additions of builders and detergents were made to various beakers at outlined in
Table 1.
[0056] Run Nos. 1-4 and 6 represent comparative methods, while Run No. 5 represents a method
embodying the invention.
[0057] In this experiment, the samples of wool were treated consecutively as separate 10g
samples with a residence time of 2 minutes in each beaker/bowl. The wool was passed
through a laboratory mangle between each beaker to simulate the squeeze rollers used
on industrial scouring ranges.
[0058] The first 30g of each 50g sample was carded on a Shirley Miniature laboratory cotton
card to produce an evenly distributed array of aligned fibres from which reflectance
measurements could be made to assess the colour of wool. A Zeiss Elrepho Spectrometer
was used for this operating at 460 nm and using a Zeiss supplied white disc as a reflectance
standard. Data are presented as R460 values, ie reflectance at 460 nm on a scale of
1 to 100, where 100 represents a perfect "white". Measurements were made at ten different
places on the wool sample and results averaged.
[0059] The remaining 20g of each 50g sample was treated in a similar manner to provide a
measure of the change in the observed data as soil and other contaminants accumulated
in the beakers. Approximately 5g of this wool was accurately weighed, extracted with
dichloromethane for 2 hours and reweighed to assess the residual grease level on the
wool.
[0060] The results of the reflectance and residual grease level tests are shown in Table
2 below.
a) Colour (whiteness) of the Wool
[0061] The poorest result (Run 1) is found when using detergent only in Bowls 1 and 2. A
small improvement can be obtained by using a hot suint bowl (Run 3). If a mixed builder
system is included with the detergents in Bowls 1 and 2 then, as Run 2 shows, some
improvement in colour is obtained.
[0062] Run 4 shows that the use of a suint bowl in combination with detergent and builder
in Bowls 2 and 3 produces a further improvement in colour (whiteness). However, the
best colour is found for Run 5 where the major portion of the builder is included
in the first suint bowl. This improved whiteness is especially apparent for the results
from the last 20g of wool from the 50g sample. At this stage the scouring solutions
in the beakers have started to "mature" and scouring efficiency is becoming optimal.
Thus, it is recognised in the industry that after cleaning and refilling the bowls,
scouring efficiency is somewhat reduced for about the first 30 minutes until the bowls
begin to "mature". We believe that such maturation may be due to improved wetting
resulting from the formation of soaps of wool grease.
[0063] Run 6 shows the results for a prior art method of B.O. Bateup and J.J. Warner, Text.
Res. J. (1986),
56, 489, where a cold suint bowl is used with sodium carbonate as the builder. As discussed
above, this method is usually used to facilitate effluent disposal and not to optimise
the quality of the scour. The reflectance values show it to be inferior to the built
suint bowl used in the method embodying the invention
b) Residual Wool Grease
[0064] All six runs gave acceptably low values of residual wool grease. It is common practice
to try and optimise the wool scour process to give residual values in the range 0.35-0.45%
by weight. Lower residual levels than this can give problems in subsequent processing.
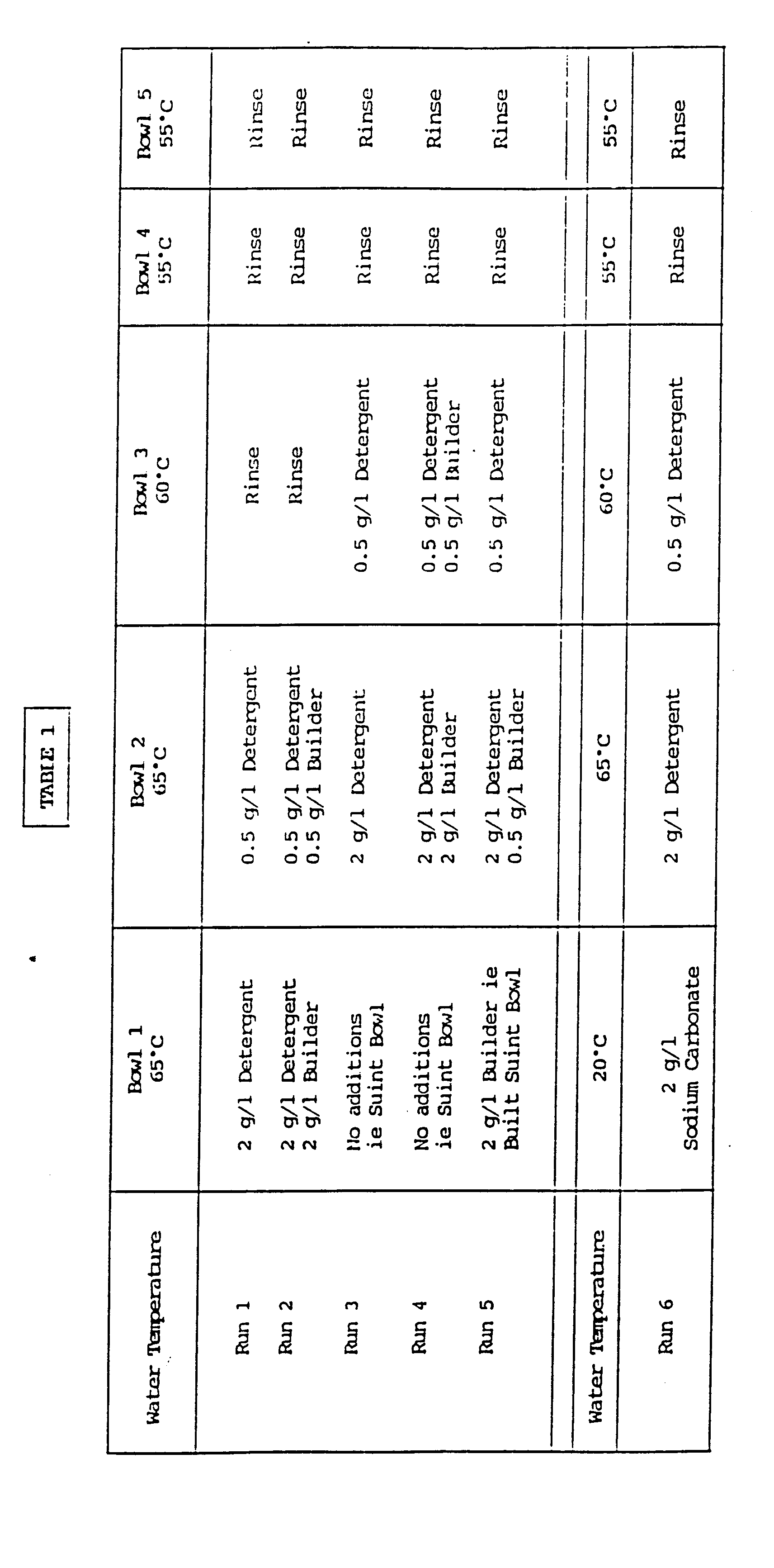
[0065] In the experiments set out in Table 1, the builder employed was a mixture of sodium
silicate and sodium carbonate in a 40:60 weight ratio.
[0066] The detergent employed had the following formulation:-
- 45.8% Synperonic NP9¹
- (ex ICI)
- 14.0% Synperonic NP4²
- (ex ICI)
- 14.5% Caflon DP848³
- (ex Cargo Fleet Chemicals)
- 3.5% Caflon SNA⁴
- (ex Cargo Fleet Chemicals)
- 1.2% NaOH 100°Tw
- (ex ICI)
- 14.0% Water
- 5.0% Dowanol TPM⁵
- (Dow Chemicals)
Notes:
- ¹ Synperonic NP9
- - nonyl phenol plus 9 moles ethylene oxide.
- ² Synperonic NP4
- - nonyl phenol plus 4 moles ethylene oxide.
- ³ Caflon DP848
- - 50:50 mixture of Synperonic 91/6 and Synperonic 91/8.
- Synperonic 91/6
- - C₉-C₁₁ linear alcohol ethoxylate (6 moles ethylene oxide)
- Synperonic 91/8
- - C₉-C₁₁ linear alcohol ethoxylate (8 moles ethylene oxide)
- ⁴ Caflon SNA
- - dodecyl benzene sulphonate as the Na salt
- ⁵ Dowanol TPM
- - tripropylene glycol mono ethyl ether

[0067] Although not wishing to be bound by theory, it is believed that the scouring method
embodying the invention exhibits the advantages illustrated above for the following
reasons.
1. By using a hot "built" suint bowl system in accordance with the invention, most
of the particulate soil and some of the greasy soils is removed in the first bowl
without the addition of extra detergents. The main detergent bowl (bowl 2) therefore
receives the wool in a much cleaner condition. This leads to more cost-effective use
of the (comparatively expensive) detergents. In particular, as a result of extended
bulk running trials, we have found that overall detergent usage is reduced and the
scouring range can be operated in continuous mode for longer periods before all bowls
have to be emptied for cleaning.
2. Because of the efficiency of sequestration of calcium and magnesium in the suint
bowl by the builder, problems of calcium and magnesium soap formation are avoided.
Thus, in conventional wool scouring processes, the formation of free fatty acids in
the warm wool grease tends to result in the formation of a hard "skin" of calcium
and magnesium soaps around the droplets of grease on the wool fibers. This skin is
extremely difficult to remove and is often not properly removed at all, resulting
in an undesirable grey colour being imparted to the wool.
3. This is especially so when using a mixture of sodium silicate/sodium carbonate,
which we find is a more effective builder than sodium carbonate alone.
4. The alkaline conditions created cause saponification of the fatty acids in the
wool grease, so creating detergent molecules from within the wool grease, thereby
yielding soaps in situ in the grease. Accordingly, the detergent action starts before
additional detergent is introduced. Thus, the system begins to self-emulsify before
the addition of any detergent.
5. The combination of silicate and carbonate provides excellent soil suspending properties,
thus giving efficient removal of particulate soils, with no tendency for redeposition.
1. A method of scouring raw wool comprising the steps of (a) treating the wool with an
aqueous medium containing a building agent capable of reducing the level of free calcium
and/or magnesium therein and thereafter (b) treating the wool with an aqueous medium
having a pH of at least 8, containing a detergent and having a temperature of at least
45°C characterised in that step (a) is carried out at a temperature of at least 45°C.
2. A method according to claim 1, wherein the aqueous medium in step (a) has a pH of
at least 8.
3. A method according to claim 1 or claim 2, wherein the pH of the aqueous medium in
step (a) is from 8 to 10.5 inclusive.
4. A method according to claim 1 or claim 2, wherein the said building agent in step
(a) is capable additionally of controlling pH so as to provide the said pH of at least
8.
5. A method according to claim 4, wherein the building agent comprises at least one inorganic
ionic compound.
6. A method according to claim 5, wherein the building agent is a mixture of inorganic
ionic compounds.
7. A method according to claim 6, wherein the said mixture comprises an alkali metal
silicate and an alkali metal carbonate.
8. A method according to claim 7, wherein the alkali metal is sodium.
9. A method according to claim 8, wherein the mixture comprises sodium silicate/sodium
carbonate in a proportional amount of from 30/70 to 50/50.
10. A method according to claim 9, wherein the proportional amount of sodium silicate/sodium
carbonate is about 40/60.
11. A method according to any preceding claim, wherein the building agent present in the
aqueous medium in step (a) is also present in the aqueous medium of step (b).
12. A method according to any preceding claim wherein the temperature of the aqueous medium
in step (a) is from 60 to 70°C inclusive.
13. A method according to any preceding claim, wherein the detergent present in the aqueous
medium in step (b) is a non-ionic detergent.
14. A method according to any preceding claim, which is a continuous process.
15. A method according to claim 14, wherein the wool is passed in one direction so as
to be immersed in (a) a first aqueous medium present in a first bowl, which first
aqueous medium contains a building agent capable of reducing the level of free calcium
and/or magnesium in the aqueous medium and having a temperature of at least 45°C,
thereby to effect the said step (a), and thereafter is immersed in (b) a second aqueous
medium present in a second bowl which second aqueous medium has a pH of least 8, contains
a detergent, and has a temperature of at least 45°C thereby to effect the step (b),
and water flows in the opposite direction so as to provide the aqueous medium for
step (b) and thereafter for step (a).
16. A method according to any preceding claim, which includes the step (c), carried out
subsequently to step (b), of treating the wool with an aqueous medium containing a
detergent and being at a temperature of at least 45°C.
17. A method according to claim 16, wherein steps (a), (b) and (c) are carried out successively.
18. A method according to any preceding claim, which includes at least one additional
rinsing step in which the wool is treated with an aqueous medium which is at a temperature
of at least 45°C.
19. A method of scouring wool comprising the successive steps of
(a) treating the wool with an aqueous medium containing a building agent capable of
reducing the level of free calcium and/or magnesium in the aqueous medium, having
a pH of at least 8 and having a temperature of at least 60°C,
(b) treating the wool from step (a) with an aqueous medium having a pH of at least
8 and a temperature of at least 60°C and containing a detergent,
(c) treating the wool from step (b) with an aqueous medium having a temperature of
at least 55°C and containing a detergent,
(d) treating the wool from step (c) with an aqueous medium having a temperature of
at least 50°C to provide a first rinse and
(e) treating the wool from step (d) with an aqueous medium having a temperature of
at least 50°C to provide a second rinse.