[0001] This invention relates to processes for bonding non-woven webs of organic fibers
to form nonwoven fabrics. More specifically, the invention relates to such processes
wherein the web is preferentially bonded in spaced, discrete areas.
[0002] Nonwoven fabrics and numerous uses thereof are well known to those skilled in the
art. Such fabrics are prepared by forming a web of continuous filament and/or staple
fibers and bonding the fibers at points of fiber-to-fiber contact to provide a fabric
of requisite strength.
[0003] Depending on the intended use of the non- woven web, satisfactory bonding in some
instances be accomplished mechanically, e.g., by needle punching or interlacing of
the fibers or by application of adhesives to the fibrous web. However, in a number
of applications nonwoven fabrics bonded by autogenous fiber-to-fiber fusion are desired.
Bonding of this type is in some instances obtained by the application of heat to soften
or plasticize the fibers and render them cohesive. In such thermal bonding techniques
the web can be subjected to mechanical compression to increase contact of the thermally
softened fibers and provide bonds of required strength. When web fibers are bonded
at essentially all points of fiber-to-fiber contact, for example, by overall compression
of the web in the presence of heat, the resultant nonwoven fabric tends to be stiff
and boardy and characterized by low elongation and tear resistance. That is, such
overall bonded fabrics are frequently more similar to paper than to conventional textile
fabrics. In order to more closely simulate the properties of conventional textiles,
nonwoven "point-bonded" fabrics have been prepared by processes tending to effect
preferential bonding in spaced, discrete areas (primary bond sites). In order to provide
point-bonded nonwoven fabrics of adequate strength, it is generally necessary that
bonding of the web in the primary bond sites be accompanied by mechanical compression.
This is generally accomplished by compressing the nonwoven web between mechanical
compression means such as a pair of rollers or platens at least one of which carries
bosses sized and spaced to provide the desired pattern of primary bond sites or both
of which carry land and groove designs interacting to provide the desired pattern.
The compression means are generally heated sufficiently to effect thermal bonding.
By a proper selection of sizing and spacing of the bosses or lands and grooves, control
of the bonding conditions (temperature and compressive force), it is possible to obtain
non- woven point-bonded fabrics having acceptable strength and improved tactile properties
such as softness. However, even point-bonded fabrics are frequently less soft than
conventional fabrics of comparable strength. This is probably due, at least in part,
to "tack" bonding. When the bonding conditions are controlled to provide fabrics having
good strength and durability during washing, bonding is not limited to the primary
bond sites produced in the areas compressed. Varying degrees of secondary or "tack"
bonding are generally observed between the primary bond sites. Such "tack" bonding
probably results from the fact that techniques employed for preparing point-bonded
non- woven fabrics expose areas of the web between the areas being compressed to heat
sufficient to effect some softening and tack bonding of fibers at points of contact.
The strength and number of the tack bonds formed may vary widely with the properties
of the fiber utilized in the web as well as the conditions employed for effecting
bonding in the primary bond sites. Desired fabric properties such as softness are
progressively impaired as the degree of tack bonding is increased. There is, therefore,
a need in the art for processes capable of providing softer non- woven fabrics.
Summary of the invention
[0004] The process of the invention is one for making point-bonded nonwoven fabrics by simultaneously
heating and compressing spaced discrete areas of a nonwoven web to effect thermal
bonding of fibers in such areas, there being incorporated in said web an attenuating
liquid in sufficient quantity that under the conditions of heat and compression employed,
a point-bonded fabric is obtained which has a bending modulus at least 20% lower than
that of a fabric prepared without the use of said attenuating liquid under otherwise
equivalent conditions.
[0005] The practice of the invention will be understood from the following description of
the preferred embodiments.
Description of the preferred embodiments
[0006] The process of this invention can be utilized for making point-bonded fabrics from
non- woven webs of thermally bondable organic fibers. The phrase "thermally bondable
organic fibers" is used herein in the specification and claims to denote fibers which
can be bonded at points of fiber-to-fiber contact by the application of heat and compression.
Thus, essentially any thermoplastic polymer can be utilized. The fibers may be in
the form of continuous filaments or staples or mixtures thereof.
[0007] Examples of bondable fibers suitable for use in the practice of this invention include
polyamide fibers such as nylon 6 and nylon 66; and polyester polymer fibers. Composite
fibers such as fibers having a sheath of one polymer and a core of another polymer
or side-by-side poly- component fibers can be utilized. In the case of multicomponent
fibers it is not essential that all polymer components thereof be bondable under the
process conditions hereinafter described. It is sufficient that such multicomponent
fibers have bondable surface portions. If desired, the fibers can be crimped or textured
to provide elasticity or other desired characteristics to the finished fabric.
[0008] In accordance with the present invention, the thermally bondable fibers are processed
in the form of nonwoven webs. The nonwoven webs of bondable organic fibers may be
composed entirely of bondable fibers or, alternatively, may consist of bondable fibers
interspersed with other fibers. The art of preparing nonwoven webs is well understood
and the manner of web formation is not critical. Generally webs are formed by deposition
of fibers on a moving belt in either random or aligned orientation to provide a web
having a weight of from 4 to 400 grams per square meter, preferably 10 to 150 grams
per square meter. Particularly useful methods for web formation are disclosed in United
States Patent No. 3,542,615.
[0009] In accordance with the present invention a selected quantity of attenuating liquid
is applied to the web and the web is simultaneously heated and compressed in spaced
discrete areas to effect bonding of the fibers in such areas.
[0010] The attenuating liquid can be any liquid whose presence in the web in quantities
of 1000% or less of the web weight does not, under the bonding conditions employed,
provide a fabric having higher strip tenacity (strength) than would be obtained in
the absence of such liquid under otherwise equivalent conditions and which provides
a fabric having at least a 20% lower bending modulus than that of a fabric obtained
in the absence of such liquid under otherwise identical conditions.
[0011] A key element of the present invention is this unexpected discovery that utilization
of an attenuating liquid in sufficient quantity will provide a reduction in fabric
bending modulus (i.e., an increase in fabric "softness") as compared to that of fabrics
prepared using no liquid under otherwise equivalent conditions. In accordance with
the present invention a quantity is employed to reduce bending modulus by at least
20%. The actual amount of attenuating liquid used may be any quantity sufficient to
effect such reduction. Generally, there is no theoretical objection to use of very
large quantities of liquid.
[0012] However, it will be observed that after a determinable quantity is added, the use
of additional liquid will not provide substantial additional improvements in softness
and, in some instances, may tend to reduce fabric strength, probably by cooling the
heating means employed. Of course, excessive amounts of liquid beyond that contributing
to improvement of fabric properties will present unnecessary process problems with
respect to liquid handling, recovery, etc. It is preferred that the amount of liquid
be chosen such that in addition to reducing bending modulus by at least 20% a higher
ratio of strip tenacity to bending modulus (as compared to that obtained using no
liquid) is obtained. That is, the maximum quantity utilized is preferably chosen so
as not to reduce fabric strength disproportionately to improvements in softness obtained.
[0013] Whether or not a particular liquid will function as an attenuating bonding liquid
will depend on the nature of the nonwoven web to be bonded, the properties of the
fibers constituting the web and the manner in which the web is heated and compressed.
Therefore, it is not practical to exhaustively list all combinations of liquids, fibrous
webs and conditions of temperature and compression suitable for the practice of the
present invention. For example, water will effectively improve the bonding of a web
of nylon fibers highly compressed in spaced discrete areas at temperatures below that
required to cohesively soften an otherwise identical dry web. Thus, under such conditions
water is considered a bonding agent rather than an attenuating liquid. However, under
low compressive force and temperatures sufficiently high to effect thermal bonding,
water may function as an attenuating liquid. The effectiveness of a particular liquid
as an attenuating liquid under given bonding conditions can readily be determined
by routine tests.
[0014] It is believed that attenuating liquids provide softening by limiting (for example
by evaporative cooling, heat capacity, etc.) the temperatures attained in the web
in areas not being simultaneously heated and compressed as hereinafter described.
The heat attenuation provided by the liquid is believed to limit or prevent tack bonding
outside the discrete, spaced areas which are heated and compressed, thereby providing
a softer fabric. Thus in selecting liquids for testing, preference may be given to
those which have relatively low boiling points as compared to fiber softening points
and/or those having high heat capacities. In general, any liquid which is not a bonding
agent and has a boiling point below the fiber softening point will be an effective
attenuating liquid. It is further contemplated that a number of liquids having boiling
points higher than the fiber softening point will be effective attenuating liquids,
presumably due to heat attenuation resulting from heat capacity, vaporization, etc.
preventing the web fibers from reaching bonding temperatures in the uncompressed areas
when sufficient liquid is employed.
[0015] Under properly correlated simultaneous application of heat and compression to appropriate
nonwoven webs, examples of liquids contemplated to be suitable attenuating liquids
for polyamide fibers include water and hexane; examples of suitable attenuating liquids
for polyester fibers include water and carbon tetrachloride.
[0016] In accordance with this invention, the non- woven web containing the attenuating
liquid is simultaneously heated and compressed in spaced, discrete areas (points)
to effect fiber bonding in such areas thereby forming the web into a point-bonded
fabric.
[0017] Simultaneous heating and compression of the web in spaced, discrete areas can readily
be accomplished by compressing the webs between a pair of compressing means such as
rolls or platens at least one of which compression means is heated. Further, one or
both of the compression means wi!! have bosses or a land and groove design or combinations
thereof such that compression of the web will be effected in spaced discrete areas
rather than overall. In order to provide adequate overall physical properties it is
generally desirable that from 2% to 80%, preferably 3% to 50%, most preferably 5%
to 30%, of the total surface area of the web be subjected to compression. Further,
the number of spaced, discrete bond sites per square centimeter generally should be
from 1 to 250, preferably from 16 to 64.
[0018] The compressive force, the temperature, and the time of exposure of the web to compression
and heating will depend on the nature and quantity of the attenuating liquid utilized
and the nature of the fibers being processed. Therefore, for a particular nonwoven
web and a particular attenuating liquid, the compressive force, the temperature, and
the time of exposure of the web to the compressive force and heating will be correlated
to effect bonding of the web fibers in the heated, compressed areas.
[0019] Preferably, the heating and compression will be correlated to effect a degree of
bonding sufficient to provide a wash stable fabric as hereinafter defined. In general,
increases in bonding will be observed with increased temperature until a temperature
is attained beyond which further increases will have little, if any, beneficial effect.
If the operation is conducted at too high a temperature, the heat attenuation characteristics
of the liquid may not be adequate to provide requisite improvements in fabric softness.
The use of increasing quantities of attenuating liquid may require increased compressive
force and/or temperature to provide wash stable fabrics. The optimum correlation of
temperature and compressive force can, of course, be empirically determined by routine
tests.
[0020] The following examples will facilitate a better understanding of the invention and
the desirable properties of fabrics produced thereby. The tests described below are
used to determine fabric properties as reported in the examples or otherwise referred
to in the specification and claims:
Strip Tenacity
[0021] Strip Tenacity is used as an indicator of fabric strength and is determined by dividing
the breaking load of cut fabric strip (as determined by American Society of Testing
Materials procedure D-1682-84) by the fabric basis weight. Strip Tenacity is expressed
as g/cm/g/m
2. Values reported are an average of tenacities in the machine and transverse directions
of the fabric. (The machine direction corresponds to the direction of feed to the
heating -and compressing means and the transverse direction is the planar direction
at a right angle thereto).
Bending Modulus
[0022] Bending Modulus is used as a measure of fabric softness and is determined in accordance
with techniques as described in U.S. Patent 3,613,445. In accordance with such disclosure
a test fabric is forced vertically downward through a slot at a constant speed. A
signal is generated in proportional response to the load incurred in moving the fabric
into and through the slot. A load-extension curve is generated by plotting the signal
as a function of the distance. Hand, drape and bending modulus are determined by analyzing
the load-extension curve. Hand is represented by the maximum point on the load-extension
curve. Drape is represented by the slope of the load-deflection curve and bending
modulus is determined by dividing the drape value by the cube of fabric thickness.
Bending Modulus, as determined on a 10.6x 10.6 cm sample, is expressed in gm/cm
4 and values reported are an average of fabric face up and face down machine and transverse
direction measurements.
[0023] With respect to both Strip Tenacity and Bending Modulus, the requirements of the
present invention are defined in terms of relative (percent change; ratios) rather
than absolute values. Accordingly, apparatus calibrations and choice of test techniques
are not critical so long as reasonable consistency is maintained in a given series
of comparative tests.
[0024] Since individual measurements are affected by variations in fabric uniformity and
inherent limitations in the precision of various measuring technniques, it is important
to conduct and average sufficient measurements to statistically assure that the differences
in values of bending modulus and strip tenacities being compared fairly reflect differences
in fabric properties as opposed to imprecisions in measurements of imperfect fabric
uniformity.
Wash stability
[0025] Wash stability is determined as follows: Non- woven fabric samples are mixed with
at least 10 pieces of hemmed cotton sheeting each measuring about 91 cmx91 cm. The
number and size of the nonwoven fabric samples are subject to the following constraints:
1. Total area of the nonwoven samples is less than 6.5 m2,
2. Each sample is at least 465 cm2 in area with a minimum dimension of 15 cm.
3. No sample is larger than 01929 m2 in area or more than 0.305 m in its maximum dimension.
[0026] In addition, the total weight of the cotton sheeting plus the nonwoven samples should
not exceed about 1.8 kg. (These constraints assure comparable results).
[0027] The load is washed in a Kenmore Model 76431100 washing machine (marketed by Sears
Roebuck Et Co.) using the "normal" cycle (14 min.) "Hi" water level (55 !), Hot Wash,
Warm Rinse (water temperatures of 60°C.±3°, 49°C.±3°) and 90 g of American Association
of Textile Colorists and Chemists Standard Detergent 124.
[0028] The wash load is then dried in a Kenmore electric dryer, Model 6308603 (marketed
by Sears, Roebuck and Co.) for at least 30 minutes (or longer if required to dry the
entire load). The test specimens are then evaluated by visual observation to determine
the number of pills formed. A pill is a visually discernible (usually roughly spherical)
tangle of fiber, or fiber plus extraneous material, extending above the surface of
a fabric and connected to the body of the fabric by one or more filaments. A fabric
is considered to fail the test when 5 or more pills are observed in any 929 square
centimeters surface area or when more severe physical deterioration is visually discernible.
Fabrics passing the above test are considered "wash-stable". In the test described,
the pills are predominantly formed by fibers which were not bonded in the process
of which, in test procedure, were freed from bond sites. Thus the degree of pilling
provides a measure of the efficacy of the process for forming bonds and a measure
of the resulting bond integrity. In instances of very poor bonding more severe fabric
deviation than pilling, e.g., complete disintegration, may be observed. As a practical
matter, fabrics which do not pass the test (even if not totally or partially disintegrated
in the test) will not withstand substantial physical stress or repeated washings without
excessive deterioration.
Example I
[0029] Nonwoven webs composed of continuous filament, 24% crystalline polyethylenetereph-
thalate fibers and having web weights of 5 gms/meter
2 and wetted with water to the add-on percentages
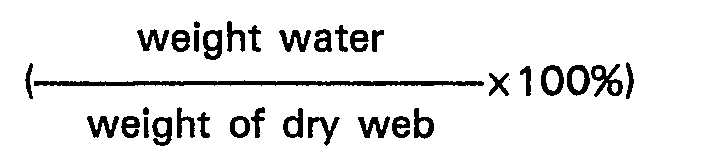
shown in Table 1 below are simultaneously heated and compressed in spaced discrete
areas by passage at a speed of .6 meters/minute between a pair of metal rolls. One
roll is smooth while the other has 28 square boss sites/cm
2 aligned in a square pattern covering about 18% of the surface area of the roll. The
pressure at the roll nip is calculated as 65.0 kg/cm (assuming all pressure to be
applied only to the boss sites). Both rolls are heated to a temperature of 230°C.
Properties of the fabrics obtained are shown in Table 1 below.
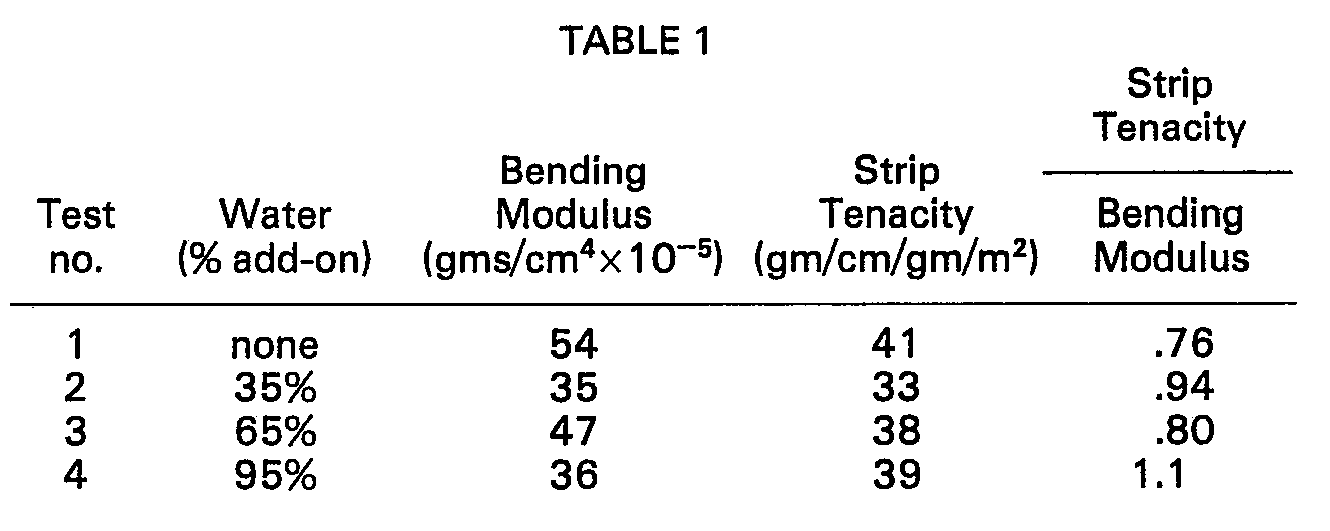
[0030] The above tests in general (test 3 is anamolous and may reflect inaccurate measuring
or sampling) show that the use of water as described enables the preparation of point-bonded
polyester fabrics of improved softness.
Example II
[0031] Nonwoven webs composed of continuous filament crystalline polyethylene terephthalate
fibers are passed (either wet with about 1000% add-on carbon tetrachloride or dry)
through the nip of a pair of rolls at a speed of 6 meters/min. Each roll bears a helical
land and groove pattern (508 micron land width; 1270 micron groove width) with the
lands and grooves disposed at 45° angles to the roll axis and cooperating to produce
a pattern of diamond shaped depressions covering about 8% of the web surface. The
rolls exert a nip pressure of 130 kg/cm (calculated as in Example 1). Processing of
webs having fiber crystallinities of 19%, 24% and 36% demonstrated that the use of
carbon tetrachloride provided in fabrics having bending moduli substantially more
than 20% lower and ratios of strip tenacity to bending modulus substantially higher
than that of webs processed dry under similar conditions.
Example III
[0032] Nonwoven webs of continuous filament nylon 6,6 were processed at 225°C. with and
without about 700% add-on hexane using the same roll pattern and presusre as in Example
II. The use of hexane provided a fabric having about a 40% lower bending modulus and
a substantially higher ratio of strip tenacity to bending modulus than that obtained
without the use of hexane.
[0033] The foregoing description of the preferred embodiments and examples will enable those
skilled in the art to practice these and all other embodiments of the invention within
the scope of the appended claims.
1. A process for making point-bonded non- woven fabrics by simultaneously heating
and compressing spaced discrete areas of a non- woven web to effect thermal bonding
of fibers in such areas, there being incorporated in said web an attenuating liquid
in sufficient quantity that under the conditions of heat and compression employed,
a point-bonded fabric is obtained which has a bending modulus at least 20% lower than
that of a fabric prepared without the use of said attenuating liquid under otherwise
equivalent conditions.
2. A process of Claim 1, in which the attenuating liquid is a liquid that is not a
bonding agent for the fibers under the said conditions and has a boiling point below
the fiber softening point.
3. A process of Claim 1 or Claim 2, in which the quantity of the attenuating liquid
is selected to provide a nonwoven fabric having a higher ratio of strip tenacity to
bending modulus than that of a fabric prepared using no liquid under otherwise equivalent
conditions.
4. A process of any of Claims 1 to 3, in which the quantity of the liquid, the temperature,
the compressive force and the time of exposure of the web thereto are correlated to
provide a wash-stable, point-bonded, nonwoven fabric.
5. A process of any of Claims 1 to 4, in which simultaneous heating and compression
of the web is effected by passing the web through and compressing the web in the nip
of a pair of rolls at least one of which is heated and at least one of which has a
pattern of raised surface portions which, in combination with the opposing surface
of the other roll, effects compression of the web in spaced, discrete areas.
6. A process of Claim 5, in which the surfaces of the rolls are designed to effect
compression providing a point-bonded, non- woven fabric having a pattern of from 16
to 64 discrete bond sites per square centimeter covering from 3% to 50% of the fabric
surface area.
7. A process of Claim 6, in which one of the rolls is provided with boss points sized
and disposed to provide a fabric having the said pattern.
8. A process of Claim 6, in which each roll has a helical land and groove surface
design interacting with the land and groove design of the opposing roll to provide
a fabric having the said pattern.
9. A process of any of Claims 1-8, in which the web comprises continuous filament
polyester fibers and the attenuating liquid is water.
1. Procédé pour traiter des tissus non tissés liés par points en chauffant et en comprimant
simultanément des surfaces séparées espacées d'une nappe non tissée pour effectuer
une liaison thermique des fibers dans ces surfaces, en incorporant dans la nappe un
liquide d'atténuation en quantité suffisante pour que, dans les conditions de chaleur
et de compression employées, on obtienne un tissu lié par points qui a un module de
flexion d'au moins 20% inférieur à celui d'un tissu préparé sans l'utilisation du
liquide d'atténuation, dans des conditions autrement équivalentes.
2. Procédé selon la revendication 1, dans lequel le liquide d'atténuation est un liquide
qui n'est pas un agent de liaison pour les fibres dans les conditions indiquées et
a un point d'ébullition en-dessous du point de ramollissement des fibres.
3. Procédé selon la revendication 1 ou la revendication 2, dans lequel la quantité
de liquide d'atténuation est choisie pour fournir un tissu non tissé ayant un rapport
ténacité de bande/module de flexion supérieur à celui d'un tissu préparé en n'utilisant
pas de liquide, dans des conditions autrement équivalentes.
4. Procédé selon l'une quelconque des revendications 1 à 3, dans lequel la quantité
du liquide, la température, la force de compression et le temps d'exposition de la
nappe sont en corrélation pour fournir un tissu non tissé, lié par points, stable
au lavage.
5. Procédé selon l'une quelconque des revendications 1 à 4, dans lequel un chauffage
et une compression simultanés de la nappe sont effectués en faisant passer la nappe
à travers, et en comprimant la nappe dans l'intervalle de deux rouleaux dont au moins
un est chauffé et dont au moins un a une configuration de parties en surface en élévation
qui, en combinaison avec les surfaces opposées d'un autre rouleau, effectue la compression
de la nappe dans des surfaces séparées, espacées.
6. Procédé selon la revendication 5, dans lequel les surfaces des rouleaux sont conçues
pour effectuer la compression en fournissant un tissu non tissé lié par points ayant
une configuration de 16 à 64 emplacements de liaison séparés par centimètre carré
couvrant 3% à 50% de la surface spécifique du tissu.
7. Procédé selon la revendication 6, dans lequel un des rouleaux est pourvu de points
de bossage dimensionnés et disposés pour fournir un tissu ayant cette configuration.
8. Procédé selon la revendication 6, dans lequel chaque rouleau a une construction
hélicoïdale en surface de rainures et de plats, agissant avec la construction de rainures
et de plats du rouleau opposé pour fournir un tissu ayant cette configuration.
9. Procédé selon l'une quelconque des revendications 1 à 8, dans lequel la nappe comprend
des fibres de polyester à filaments continus et le liquide d'atténuation est l'eau.
1. Verfahren zum Herstellen von punktweise gebundenen, nichtgewebten Stoffen durch
gleichzeitiges Erhitzen und Pressen diskreter Bereiche einer nichtgewebten Gutbahn
zum Herbeiführen einer thermischen Bindung von Fasern in solchen Bereichen, bei welchem
eine abschwächende Flüssigkeit in einer solchen Menge in der Gutbahn enthalten ist,
daß man unter den angewendeten Bedingungen von Hitze und Druck einen punktweise gebundenen
Stoff erhält, dessen Beigemodul um wenigstens 20% niedriger ist als der eines ohne
die Verwendung der abschwächenden Flüssigkeit unter sonst gleichartigen Bedingungen
hergestellten Stoffs.
2. Verfahren nach Anspruch 1, in welchem die abschwächende Flüssigkeit eine Flüssigkeit
ist, welche unter den gegebenen Bedingungen kein Bindemittel für die Fasern darstellt
und deren Siedepunkt unterhalb des Erweichungspunkts der Fasern liegt.
3. Verfahren nach Anspruch 1 oder 2, in welchem die Menge der abschwächenden Flüssigkeit
so gewählt ist, daß der hergestellte nichtgewebte Stoff ein höheres Verhältnis von
Stripfestigkeit zu Biegemodul hat als ein ohne die Verwendung von Flüssigkeit unter
sonst gleichartigien Bedingungen hergestellter Stoff.
4. Verfahren nach einem der Ansprüche 1 bis 3, in welchem die Menge der Flüssigkeit,
die Temperatur, die Preßkraft und die Zeitspanne, während welcher die Gutbahn diesen
ausgesetzt ist, derart aufeinander abgestimmt sind, daß man einen waschfesten, punktweise
gebundenen, nichtgewebten Stoff erhält.
5. Verfahren nach einem der Ansprüche 1 bis 4, in welchem das gleichzeitige Erhitzen
und Pressen der Gutbahn erfolgt, indem man die Gutbahn unter Kompression durch den
Spalt zwischen zwei Walzen hindurchführt, von denen wenigstens eine beheizt ist und
von denen wenigstens eine ein Muster von Oberflächenerhebungen hat, welches im Zusammenwirken
mit der gegenüberliegenden Oberfläche der anderen Walze eine Pressung der Gutbahn
in einzelnen, diskreten Bereichen bewirkt.
6. Verfahren nach Anspruch 5, in welchem die Oberflächen der Walzen so ausgebildet
sind, daß der durch das Pressen hergestellte, punktweise gebundene Stoff ein Muster
von etwa 16 bis 64 diskreten Bindungspunkten pro Quadratzentimeter aufweist, welche
zwischen 3% und 50% der Oberfläche des Stoffs abdecken.
7. Verfahren nach Anspruch 6, in welchem eine der Walzen mit punktförmigen Erhebungen
versehen ist, welche so bemessen und angeordnet sind, daß ein Stoff mit dem genannten
Muster entsteht.
8. Verfahren nach Anspruch 6, in welchem jede Walze ein Oberflächenmuster aus entlang
Schraubenlinien verlaufenden Erhebungen und Rillen aufweist, welches mit dem aus Erhebungen
und Rillen gebildeten Oberflächenmuster der gegenüberliegenden Walze zusammenwirkt,
so daß ein Stoff mit dem genannten Muster entsteht.
9. Verfahren nach einem der Ansprüche 1 bis 8, in welchem die Gutbahn fortlaufende
Polyester-Elementarfasern enthält und die abschwächende Flüssigkeit Wasser ist.