[0001] This invention relates to a tracking system. More particularly, this invention relates
to a tracking system which can be used in the manufacture of containers, such as glass
bottles.
[0002] As is known, when manufacturing containers, for example made of glass, molds are
frequently provided in groups at a hot station to form the containers and various
types of conveyors are employed to move the containers to a cooling station for cooling
purposes and for shipment to an end user. It has also been known that various types
of inspection stations can be provided between the hot station and the cold station
in order to inspect each container for defects.
[0003] In some cases, each inspection station has been provided with a reject mechanism
which can be activated by a suitable defect sensor so as to remove a defective container
once detected. However, should a defect be caused by one particular mold in a mold
group, several defective containers can be made before a determination is made that
there is a defective mold.
[0004] It has also been commonplace in the construction of multi-station inspection machines
to inspect for many defects and to save all rejects until the containers have passed
through all the stations. It has also been known to correlate certain information
regarding the mold in which a container was made, i.e. the "cavity number" with the
reject information. To this end, use has been made of cavity tracking methods wherein
a cavity number can be electronically assigned to a given container and tracked with
the container through the various inspection stations. In such cases, after the containers
have passed through all the inspection stations, the rejects can be eliminated and
the corresponding cavity numbers can be investigated to determine if, for example,
certain mold cavities are producing certain defects so as to permit repair or replacement
of such mold cavities.
[0005] For example, it has been known to use a so-called open conveyor tracking technique
wherein an encoder is used to gauge the travel of a conveyor while one proximity detector
is placed at the beginning of an area through which containers are to be tracked and
a second proximity detector is placed at the end of the tracking area. As a container
passes the first detector, a cavity number is received from an upstream cavity indentification
system or tracking device. Simultaneously, a count value from the encoder is recorded.
Thereafter, when the container passes the second proximity detector a second count
value is recorded from the encoder and compared against a range of counts which correspond
to the distance travelled by the conveyor between the two proximity detectors. Presuming
the container has not moved relative to the conveyor the cavity number of the container
is then passed to a downstream tracking device or other downstream system.
[0006] However, it has been found that if the sequence of containers passing through the
inspection station changes or if the spacing between the containers changes accidentally
or otherwise, the final results of the cavity tracking system may be in error.
[0007] Further, inspection machines are frequently provided with inlet stations, for example,
employing a rotatable screw, for the individual inlet of a container. In such cases,
a series of containers may stack up behind the screw such that the conveyor moves
relative to the containers. In such cases. open conveyor tracking will not give efficient
results.
[0008] Accordingly, it is an object of the invention to provide a reliable tracking system
for containers which tend to stack up on a conveyor belt.
[0009] It is another object of the invention to maintain a one-to-one correspondence between
a container and its electronic label as the container passes through an area where
containers stack up or change speed and undergo relative movement.
[0010] It is another object of the invention to provide a relatively simple system for tracking
containers moving through a stacked region of a conveyor.
[0011] A preferred embodiment of the invention provides a tracking system which comprises
a conveyor belt for conveying a series of containers, such as glass bottles, through
a series of inspection stations, an identification station disposed along the conveyor
belt and having means for generating an identification signal in the form of a "cavity
number" corresponding to a container passing thereby, an encoder for generating count
pulses corresponding to the travel of the conveyor belt, a tracking station disposed
along the conveyor belt adjacent to an area where containers stack up or change speed
and undergo relative motion, a screw infeed being an example, with the tracking station
including a plurality of closely spaced sensors each of which is disposed to generate
a "present" signal in response to a container passing thereby and a programmer means
connected to the identification station, encoder and tracking station.
[0012] The programmer means is provided with a store or memory to sequentially receive and
store each "cavity number" generated at the identification station as well as a plurality
of zones for sequentially receiving each cavity number from the store. In addition,
means are provided which are responsive to a "present" signal from a first of the
sensors and a corresponding "count" signal from the encoder in order to pass a first
of the "cavity numbers" in the store (memory) to a first of these zones. Means are
also provided which are responsive to a "present" signal from a second sensor to pass
the "cavity number" in the first zone to a second zone.
[0013] In other words, as a bottle passes the first sensor, the cavity number associated
with the container is placed in the store of the programmer means. When the container
passes the second sensor, the cavity number is destructively read from the store and
passed into a memory in the first zone. Since there are no time constraints on when
the bottle must pass the second sensor, the bottle may slide or hesitate on the conveyor
belt. Further, if the container is removed from the area between the sensors, the
bottle does not pass the second sensor. Hence, its cavity number is not passed down
the line. Furthermore, the next bottle which does pass the second sensor will overwrite
the memory with its own cavity number and that correct number will be passed down
the line when this bottle passes the next sensor.
[0014] As long as the bottle is moving smoothly through the array of sensors its associated
cavity number will be shifted from one zone to the next in proper sequence. When a
cavity number is passed from one zone to the next, a message can be left behind indicating
"empty". This "empty" message can then be used to instruct the programmer means not
to pass a cavity number into the next zone in response to a "present" signal from
the sensor array. Hence, if a bottle is placed between two others in the stream, the
next sensor it passes sends the "empty" message ahead. Thus, the system recognizes
that this container was inserted and applies "unknown cavity number" to this bottle.
[0015] The tracking system may also employ a read-out means which is connected to the programmer
means in order to receive and read-out the "cavity number" from a last of the zones
associated with the sensor array in response to a "present" signal from a last of
the sensor in the array.
[0016] The above tracking technique may employ a single-element first in-first out memory
in the form of a set of flip-flop switches in each zone to accomplish the array tracking
task. For example, in response to a bottle passing the first sensor, the cavity number
is delivered from the store and shifted into the set of flip-flop switches in the
first zone. When the bottle passes the second sensor, the cavity number is destructively
read from the first zone, i.e., by being erased from the switches and passed to the
set of flip-flop switches in the next zone.
[0017] In the case of glass bottles of cylindrical cross section the sensors of the sensor
array are placed less than one bottle diameter apart along the length of the conveyor
belt. In this case, each sensor may be an optical proximity detector comprised of
a high intensity infrared-emitting diode and a photosensor. In addition, the diode
is positioned to emit light at a first angle onto a surface of a glass bottle passing
thereby while the photosensor is positioned to receive light reflected from the bottle
surface at a second angle. By placing the diode and photosensor at a slight angle
to the horizontal, spurious reflections from other nearby objects can be eliminated.
In addition, a short focal length lens can be positioned in front of each diode and
each photosensor in order to sharply limit the field of view of each.
[0018] The encoder for generating a signal representative of the travel of the conveyor
belt can be coupled to the conveyor belt by a rubber tired wheel which is mounted
on a shaft of the encoder to be driven by frictional engagement with the conveyor
belt.
[0019] The tracking system may be employed wherever a series of containers, such as glass
bottles, are conveyed past various inspection stations and wherein a stacking-up of
the containers may occur, for example at a feed screw. In this respect, the tracking
system would be connected between tracking devices in order to receive and convey
a "cavity number" signal associated with a conveyed container. To this end, the upstream
tracking device would be connected to the store of the programmer means in order to
deliver the "cavity number" signal when the associated container has entered the tracking
system. As the container thereafter moves along the conveyor, the "cavity number"
signal can be relayed from switch to switch, i.e., zone to zone in the programmer
means until the container leaves the tracking system. At this time, the "cavity number"
signal would be passed from the last flip-flop switch to the downstream tracking device
or to the read-out means for subsequent processing.
[0020] These and other objects and advantages of the invention will become more apparent
from the following description taken in conjunction with the accompanying drawings
wherein:
Fig. 1 illustrates a diagrammatic view of a tracking system constructed in accordance
with the invention;
Fig. 2 illustrates a tracking sensor array used in the system of Fig. 1 in accordance
with the invention;
Fig. 3 illustrates a plan view of the tracking sensor array in Fig. 2;
Fig. 4 illustrates the angular position of the elements of an optical proximity detector
disposed in accordance with the invention; and
Fig. 5 graphically illustrates an algorithm for an array tracking method in accordance
with the invention.
[0021] Referring to Fig. 1, the tracking system 10 includes a single line conveyor 11, such
as a conveyor belt, for conveying a series of containers, such as glass bottles 12
through a cavity identification system 13, an on-line thickness selector 14, a screw
feed 15 of an inspection apparatus and a tracking station 16 adjacent the screw feed
15. In additon, an encoder 17 is positioned between the on-line thickness selector
14 and the tracking station 16.
[0022] The conveyor belt is of any suitable construction, for example, the belt may be made
up of a plurality of interconnected links which provide a continuous flat surface
on which the bottle 12 may stand and be conveyed.
[0023] The cavity identification system 13 is of known construction and is available from
American Glass Research of Bulter, Pennsylvania. In this regard, the cavity identification
system may be constructed with a read module which is attached to the conveyor and
provides the handling necessary to bring the bottles 12 off-line over a camera 18
while returning the bottles 12 to the original conveyor. With each bottle provided
with a single ring binary code molded into the bottom, each bottle is passed through
the read module and a strobe transmits light through the bottle. The camera 18 images
the code so that the read module transmits the image to a decode module which processes
the data so as to produce a cavity number for each bottle which passes through.
[0024] The cavity identification system 13 is provided with suitable sensors 18, 19' for
tracking of a bottle through the system 13; the upstream sensor 19 determining the
presence of a bottle entering the identification system and the downstream sensor
19' determining the presence of the bottle at the outlet of the identification system.
[0025] The on-line thickness selector 14 is an inspection device of conventional structure
and is available from America Glass Research, inc., of Bulter, Pennsylvania. This
selector 14 operates so as to measure the thickness of a single bottle 12 passing
therethrough. In this respect, the on-line thickness selector 14 operates on only
a single bottle at a time. Thus, the individual bottles are accelerated upon entering
the selector 14 so as to provide individual attention. During this time, the individual
bottles are lifted from the conveyor belt 11.
[0026] The thickness selector 14 is also provided with a pair of sensors 20, 21 for tracking
of a bottle therethrough, the upstream sensor 20 determining the presence of a bottle
at the entry to the thickness sensor (not shown) within the selector 14 and a downstream
sensor 21 which determines the presence of a bottle at the output of the selector
14.
[0027] In addition, the thickness selector 14 includes a microprocessor (not shown) in an
information interface cabinet (not shown) which accepts cavity numbers, encoder counts
and inputs from the sensors 19, 20, 21 and "tracks" the cavity number through the
thickness selector 14. Then that microprocessor passes the cavity number, etc. to
another microprocessor 31 in an information interface cabinet (not shown) associated
with the inspection apparatus having the screw feed 15.
[0028] The screw feed 15 is also of conventional structure. To this end, the screw feed
includes a screw 22 which receives and spaces individual bottles for input to other
systems or devices.
[0029] The tracking station 16 includes a plurality of closely spaced sensors 23 each of
which is disposed to generate a "present" signal in response to a bottle 12 passing
thereby. Referring to Figs. 2 and 3, the sensors 23 are spaced apart a distance less
than the diameter of a bottle 12 for reasons as explained below. In addition, the
sensors 23 are disposed in a housing module 24 of elongated shape.
[0030] As indicated in Fig. 4, each sensor 23 includes a pair of electro-optical devices,
one of which is a high intensity infrared-emitting diode 25 for emitting a light across
the conveyor belt 11, and the other of which is a photosensor 26 for receiving light
reflected from a container 12 on the conveyor belt 11. As indicated, the light emitting
diode 25 and the photosensor 26 of each sensor are disposed on opposite sides of a
common horizontal plane. The diode 25 is positioned below the horizontal plane to
direct light at an upwardly directed angle onto the surface of a passing bottle 12
while the photosensor 26 is positioned above the horizontal plane to receive reflected
light at an angle from the surface of the bottle 12. In addition, a short focal length
lens 27 is disposed in front of each of the diode 25 and the photosensor 26 in order
to sharply limit the field of view of each. As indicated in Fig. 4, the field of view
of the diode 25 and the photosensor 26 overlap each other within a common area F.
Thus, the illuminated area and the field of view may overlap significantly for a relatively
large range of reflecting surface positions. The use of the angular arrangement of
the diode 25 and the photosensor 26 and the lenses provide a good signal-to-noise
ratio which can be attained over a range of one-half inch to one inch distances between
the detectors 22 and the reflecting surface of a bottle 12.
[0031] The encoder 17 is associated with the conveyor belt 11 in order to generate a signal
formed of a sequence of pulses corresponding to the travel of the conveyor belt 11.
As indicated, the encoder 17 includes a shaft 28 and a rubber-tired wheel 29 which
is mounted on the shaft and which is in frictional engagement with the conveyor belt
so as to be driven thereby under frictional contact. Upon rotation of the wheel 29
and the shaft 28, the encoder 17 generates a sequence of counts. The operation of
the encoder 17 is otherwise of conventional structure.
[0032] During normal operation of the system 10, a series of bottles 12 are passed through
the cavity identification system 13 and the camera 18 forms an image of the code on
the bottom of the bottle as each bottle passes over the camera which is located between
the conveyor belt 11 and a delivery conveyor belt 30 to the identification sytem 13.
Upon passing out of the identification system onto the conveyor belt 11, each bottle
passes the sensor 19 so that a "present" signal is generated in associattion with
the cavity number signal generated by the identification system. Subsequently, the
series of bottles are individually passed through the selector 14 in known manner.
During this time, each bottle is tracked between the sensors 20, 21 in known manner.
Thereafter, the bottles are conveyed past the tracking station 16 and fed into the
screw feed 15. Should the speed of the screw feed 15 be less than the speed of the
conveyor belt 11, the bottles begin to stack-up at the screw feed 15 while sliding
relative to the conveyor belt 11.
[0033] The tracking system also includes the microprocessor 31 which is in the form of a
programmer means and is connected to the on-line thickness selector 14, the downstream
sensor 21, the encoder 17 and the tracking station 16. In addition, a readout means
32 is connected to the programmer means 31 and is located, for example adjacent to
the screw feed 15 for ease of viewing.
[0034] Referring to Fig. 5, the programmer means 31 includes a store 33 to sequentially
receive and store each "cavity number" from the means in the immediately upstream
inspection device 14 and a corresponding "present" signal from the downstream sensor
21 for each bottle 12. Also, input to the programmer means 31 is a series of "count"
signals from the encoder 17, each signal corresponding to a known amount of distance
of conveyor belt 11 travel. The programmer means 31 also includes an arithmetic and
logic unit 33A. The programmer means 31 further includes a plurality of zones for
sequentially receiving each "cavity number" from the store 33. Still further, means
is provided in the arithmetic and logic unit 33A to perform the algorithm:
When sensor
n is passed:
TEST DATA FLAG
n
IF FLAS IS CLEAR
RETURN
ELSE
GET CAVITY NUMBER FROM ZONE
n
CLEAR DATA FLAG
n
WRITE CAVITY NUMBER IN ZONE
n-1
SET DATA FLAG
n-1
RETURN
[0035] The read-out means 32 may be connected to the programmer means 31 in order to receive
the cavity number from a last of the zones in response to a "present" signal from
a last of sensors 23 of the tracking station 16.
[0036] The read-out means 32 may be in the form of a data collection means such as a computer
which correlates the cavity number with reject data and presents the data in tabular
form such as:
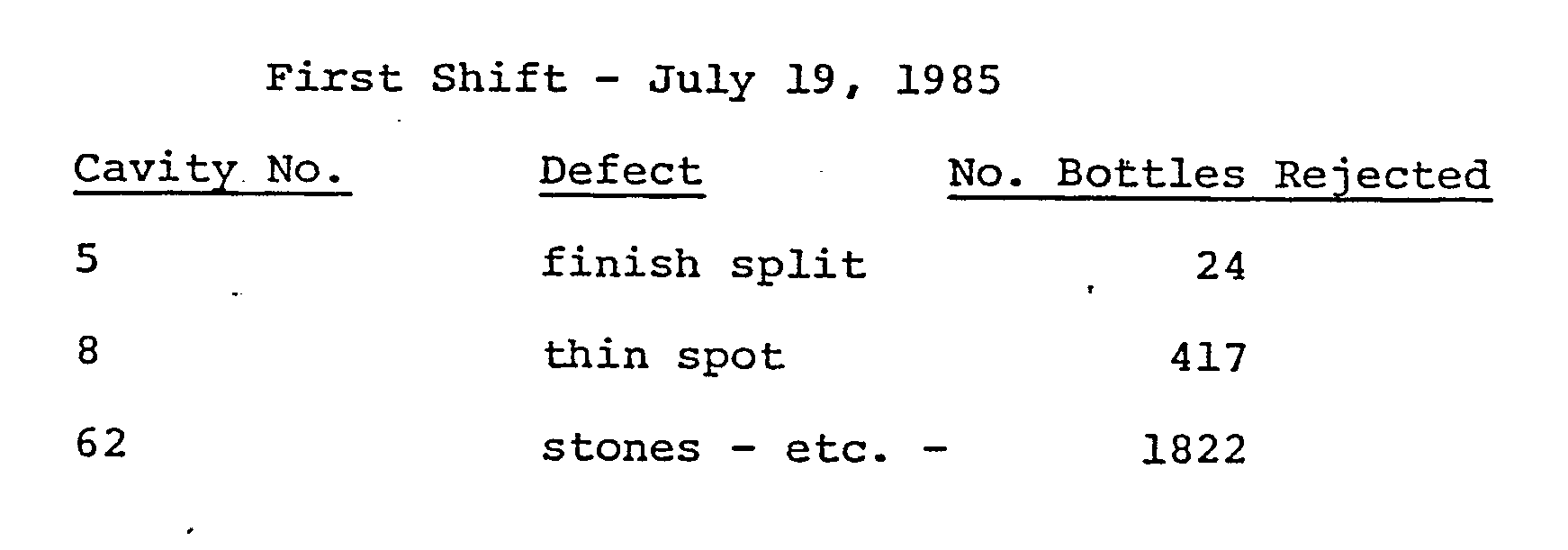
[0037] Basically, the tracking station 16 is connected with the programming means 31 so
as to effect an "array tracking". This technique relies on the assumption that two
bottles cannot occupy the same physical space. Thus, the spacing between the sensors
23 is dependent upon the diameter of the conveyed bottles 12. That is, the sensors
23 are placed at a spacing which is less than the diameter of the bottle 12. With
the sensores 23 placed as specified above, there can be no confusion as to which cavity
number is attached to which bottle 12. This is true as long as the bottle 12 move
forward at any rate or even stop. This style of tracking also allows bottles to stop,
start and bounce back while still identifying each bottle. If bottles are added or
removed in the bottle progression, the identification of known bottles is uneffected
and the added bottles are known to be unidentified.
[0038] Referring to Fig. 5, after the first bottle passes the first sensor (PD n+1) of the
tracking station 16, the cavity number of the bottle is entered into the first zone
(n+1) while a data flag is set. This assumes that the correct bottle has been received
in the tracking station 16.
[0039] Next, when the bottle passes the second sensor (PD n+1), a "present" signal is sent
to the programmer means 31. In response, the cavity number from the first zone (n+1)
is sent into the next zone (n) while the data flag in the first zone (n+1) is cleared
and the data flag in the second zone (n) is set.
[0040] Next, as the bottle passes the third sensor (PD n), the same sequence is carried
out. When the bottle passes the same sequence (PD n-2) of the tracking station 16,
the "present" signal causes the programmer means 31 to deliver the cavity number to
the read-out means 32. At this point, the cavity number can be visually displayed
as the bottle passes through the screw feed 15 and/or otherwise utilized by a data
collection means.
[0041] If the data flag in a zone is clear when tested in response to the transit of a bottle
past a sensor 23, no cavity number is passed from that zone to the next zone. This
occurs, for example, if a bottle has been inserted in the series. For example, once
a bottle has been tracked properly, the cavity number is erased from one zone while
being entered into the next zone. Thus, when an inserted bottle passes by the associated
sensor, there is no cavity number in the upstream zone. Thus, there is no cavity number
to be passed on. Instead, a message saying "empty" may be emitted via the programmer
means to the read-out means 32 when this spurious bottle passes into the feed screw
15. Alternatively, a designation that the cavity number is unknown may also be used.
[0042] Basically, the array tracking operates on the principle that a bottle must arrive
at the first sensor before arriving at the next sensor and that the first bottle must
arrive at the second sensor before the next bottle (in the progression) arrives at
the first sensor. The advantages of the array tracking techniques are that it can
deal with starts, stops, slips, and limited bounce-back.
[0043] With respect to the bounce-back, the following example is given:
[0044] If a bottle is moving smoothly through an array of sensors 23, the bottle passes
one sensor (PD n+1) and its cavity number is shifted into the zone (n) after passing
the next sensor (PDn), the cavity number is shifted into the next zone (n-1). If the
bottle slows down or stops but eventually passes the next sensor (PD n-1) the cavity
number is shifted into the zone (n-z). However, if the bottle hits another bottle
and bounces back past sensor (PD n-1) so long as the following bottle has not passed
sensor (PDn), no harm is done. That is, there is no cavity number in the zone (n-1)
but the correct cavity number appears in zone (n-2). Thus, when the bottle passes
the sensor (PD n-2) for the third time, there is no cavity number to be passed from
zone (n-1) so that the cavity number of the bottle remains in zone (n-2).
[0045] Of note, tracking can be carried out in the screw feed in a known manner.
[0046] The invention thus provides a relatively simple technique for tracking containers
in an area which is prone to stacking up of the containers, for example, at a screw
feed. Thus, should a stacking up or jam occur, the tracking system is self-starting.
That is, as soon as the jam clears to a point where the containers are able to move
freely on the conveyor belt 11, tracking begins anew.
[0047] The programming means 31 and read-out means 32 can be constructed so as to provide
useful information concerning glass container defects. Specifically, since many glass
bottle defects are correlated with the cavity in which they are blown, it is helpful
to know which cavities are producing defects. It is also useful to know what the defect
is that is being found in bottles from a given cavity. Thus, a suitable print-out
means can be provided in the tracking system to give a read-out of defects and cavity
numbers of bottles which have been inspected.
[0048] Further, the tracking system is able to perform reliably even if the bottles have
been removed during conveyance or bottles inserted on the conveyor belt.