TECHNICAL FIELD
[0001] The present invention relates to a process for the continuous production of a nonwoven
highly water-absorbent complex used as a humor absorbent, including paper diapers
and sanitary articles.
BACKGROUND OF THE PRIOR ART
[0002] As a prior art of the present invention, an absorbent complex produced by irradiation
is disclosed in International Application No. PCT/US81/00601 (W081/03274). More specifically,
after applying an aqueous acrylic acid or methacrylate solution to a fibrous substrate,
an attempt is made to obtain an absorbent complex by applying electromagnetic radioactive
rays or fine-particulate ionization radioactive rays to this material so as to convert
the acrylic acid or methacrylate into a water-swelling polymer. Since a monomer can
be used directly, this method is epoch-making in comparison with the conventional
art in which powdered polymer is mixed with wood pulp and the like (see Japanese Patent
Publication No. 53-46199).
[0003] However, the aforementioned prior art has drawbacks in that (1) since a self-crosslinking
reaction is carried out, the water-absorption properties of a complex obtained are
inferior to those of a particulate water-absorbent polymer; (2) large- scale and highly
expensive apparatuses including an electron beam accelerator are required, and the
process thereof also becomes complicated, with the result that the amount of investment
needed becomes large; and (3) the amount of residual monomers is large.
[0004] The problem of the invention is, therefore, to overcome the drawbacks of the prior
art by providing a process for producing a nonwoven complex having excellent water-absorption
properties continuously at high speed.
BRIEF SUMMARY OF THE INVENTION
[0005] This problem is solved according to the present invention by adding in advance to
an aqueous monomer solution a crosslinking agent and an oxidizing radical polymerization
initiating agent having a latent activity, and after impregnating a continuous nonwoven
fibrous web with this solution, causing a rapid polymerization reaction by adding
an activator (i.e. an oxidizing agent or a reducing agent) to this web so as to form
a water-swelling polymer in the web, thereby continuously forming a nonwoven highly
water-absorbent complex.
BRIEF DESCRIPTION OF THE DRAWING
[0006] Fig.1 is a flow sheet briefly showing the process of the present invention.
DETAIELED DESCRIPTION OF THE INVENTION
[0007] More detailed description will be made hereinafter with reference to a flow sheet
shown in the attached drawing.
(1) Nonwoven Continuous Fibrous Web
[0008] In terms of properties, it is necessary for a nonwoven fibrous web to be bulky and
porous as well as outstanding in compression recovery. Accordingly, the nonwoven fibrous
web should desirably have an apparent density of 0.05 g/cm
3 or below (preferably 0.002 to 0.02 g/cm3 ) and a compression recovery rate
* of 80% or above. To obtain the web having such properties, polyester, polypropylene,
or polyethylene hydrophobic fibers having a fineness of 3d or above (preferably 4
to 10d) and a hollow and irregular-shaped cross section are used. To prepare a nonwoven
web from these fibers, a 20 to 60 g/m
2 parallel web and a random web are formed from a fibrous mixture by the use of the
card process, the air laid process, or other similar process. Subsequently, these
webs are treated in a cylindrical drier or other heat treatment apparatus at a temperature
of 150 to 250 C so as to couple the fibers.
*Compression Recovery Rate (R) :
[0009]
1VO.5 = the bulk (mm) of a sample web when it is treated for 10 minutes under a light
load of 0.5 g/cm2.
V1 = the bulk (mm) of a sample web when it is treated for 5 hours under a heavy load
of 50 g/cm2 .
2V0.5 = the bulk(mm) of a sample web when a light load of 0.5 g/cm2 is applied to it for 10 minutes after being left for 30 minutes as it is on measurement
of V1.
(2) Polymeric Monomer
[0010] A monomer used in the present invention is an acrylic acid or one essentially constituted
by the same, and 50% or more thereof is preferably neutralized by an alkali metallic
salt, e.g. a sodium salt or a potassium salt. In view of the subsequent dehydrating
process, the higher the concentration of the monomer, the greater the economic efficiency,
with the result that it is advantageous to set the concentration of the monomer to
the vicinity of saturation solubility in a working temperature.
(3) Crosslinking Agent
[0011] One of the characteristic features of the present invention is the use of a crosslinking
agent, which proves extremely advantageous in controlling the properties of the polymer
and makes it possible to widen the range of selection of reaction conditions in comparison
with the self-crosslinking type employed in the prior art.
[0012] The crosslinking agent is selected from compounds having properties of copolymerization
with an acrylic monomer, compounds having reactivity with a functional group of an
acrylic acid monomer, or compounds having the properties of both of these two types
of compounds. Typical examples of this crosslinking agent are ethylene glycol bis-acryiate,
N,N-methylene bis-acrylamide, ethylene glycol glycidyl ether and N-methylolacrylamide.
The amount of the crosslinking agent to be added is preferably 0.1% to 3% by weight
of the polymeric monomer. If the amount is too small, a problem arises in the stability
of the gel: if too large, the water-absorbing capability decreases.
(4) Oxidizing Radical Polymerization Initiator
[0013] The radical polymerization initiator employed in the present invention must be such
as to be capable of forming a redox system with an amine and a reducing agent which
have a certain degree of solubility with respect to a monomer or water and must exhibit
oxidizing properties. As radical polymerization initiators having such properties,
it is possible to use peroxides, e.g. hydrogen peroxide, persulfates such as ammonium
persulfate and potassium persulfate, and hydroperoxides such as t-butyl hydroperoxide
and cumene hydroperoxide.
[0014] For instance, a water soluble radical polymerization intiator of azo type, which
has no oxidizing properties, cannot form a redox system with an amine or reducing
agent; therefore, it cannot be used in the present invention.
[0015] Incidentally, the amount of the radical polymerizaiton initiator used is preferably
0.1 to 2% by weight of the monomer.
(5) Activator
[0016] An activator capable of causing polymerizaiton reaction rapidly in a predetermined
period of time should form a redox system with the aformentioned oxidizing radical
polymerization initiator. For instance, one or more of the following may be used:
amines, e.g. aniline, monoethanol amine, diethanol amine, triethanol amine and dimethyl
aniline; and water soluble reducing agents, e.g. sodium sulfite, sodium hydrogensulfite,
sodium thiosulfate, copper sulfate, ferrous sulfate, and L-ascorbic acid and salts
thereof, erysorbic acid (isoascorbic acid) and salts thereof, polyphenols, such as
gallic acid, and derivatives thereof. The amount of the activator added is preferably
0.01 to 4% by weight of the monomer.
(6) Conditions for Polymerization Reaction
[0017] As descriged above, the nonwoven fibrous web containing, the mixed solution of the
monomer, the crosslinking agent and the oxidizing radical polymerization initiator
causes a rapid polymerrisation reactiion with the addition of the activator. In view
of te fact that this is a continous process, the web containg the mixed solution should
be stable for a long time before the activator is added. After the addition of the
activating agent, the rapid polymerization reaction should take place and be completed
within a short time. In addition, a highly water-absorbent polymer having a sufficient
water-absorbing capability should be formed stably in the nonwoven fibrous web. Described
below are the desirable conditions for this polymerization reaction.
(i)
[0018] The Amount of Mixed Monomer Solution to be Adhered to the Nonwoven Web.
[0019] The mixed monomer solution is adhered to the nonwoven web by means of impregnation,
coating or spraying. The amount of the mixed monomer solution to be adhered and the
conditions of adhesion vary according to the complex to be obtained, but the rate
of pickup is normally 1 to 20 weight parts with respect to 1 weight part of the web.
(ii)
[0020] Conditions of Addition of Activator.
[0021] When adding the amine or the reducing agent, it is advantageous to use the same as
it is or in the form of an aqueous solution if it is a solution, or if it is a solid,
it should be used in the form of an aqueous solution containing it. It is effective
to spray a predetermined amount of it onto the monomer-containing web, and it is desirable
to spray it onto both sides of the web as uniformly as possible.
(iii)
[0022] Adjustment of Polymerization Reaction Time.
[0023] The adjustment of polymerization reaction time is depending on the following factors:
a. The concentration and temperature of the monomer to be mixed in the web.
b. The amount of polymerization heat generated.
c. The concentration and temperature of the activating agent.
d. The ambient temperature of a reaction tank at the time of polymerization reaction.
[0024] However, it is a general practice to adjust the polymerization time by controlling
the temperature of the reaction tank described in d above.
[0025] It is possible to control the polymerization reaction time between 5 sec. to 1 hour
by selecting the conditions a,b,c and d above. However, it is desirable to complete
the polymerization reaction within 20 sec., preferably 10 sec., by maintaining the
temperature of the reaction tank at 50 to 120 C.
(7) Post-treatment of the Complex
[0026] With respect to the web for which polymerization is completed, post-treatment, including
drying for controlling the residual moisture content, softining treatment, or lamination
bonding with wooden pulp layers by making use of the residual moisture content, is
carried out before effecting a final winding-up process so as to produce the nonwoven
highly water-absorbent complex. The complex thus obtained is cut into a predetermined
size, or folded, and can be used as the inner absorbent for disposable diapers for
infants, the absorbent for diapers for adults, or the absorbent for sanitary napkins,
or, in some cases, as the absorbent for construction material and the like.
[0027] As described above, according to the present invention, the following advantages
can be obtained: (1) since the polymerization speed is high, continuous production
can be effected easily, and it is possible to use compact apparatuses for produciton;
(2) since the reaction is carried out uniformly, it is possible to effect the production
under smooth and stable operating conditions, and (3) the degree of crosslinking and
the degree of polymerization can be controlled.
BEST MODE FOR CARRYING OUT THE INVENTION
[0028] The following examples describe the present inveniton, although these should not
be considered as a limitaiton to the object of the present invention.
Example 1
1) Preparation of Web
[0029] A 50 g/m
2 web was formed from 70% of 6d x 51 mm hollow polyester fibers (made by Teijin Co.,
Ltd.) and 30% of 3d x 51 mm heat-fusible polypropylene conjugated fibers (made by
Chisso Co., Ltd.) using a card. The web was subsequently led into a heat treatment
apparatus (made by Honeycomb Co., Ltd.) heated to 220 °C and a nonwoven fabric having
the following properties was produced.
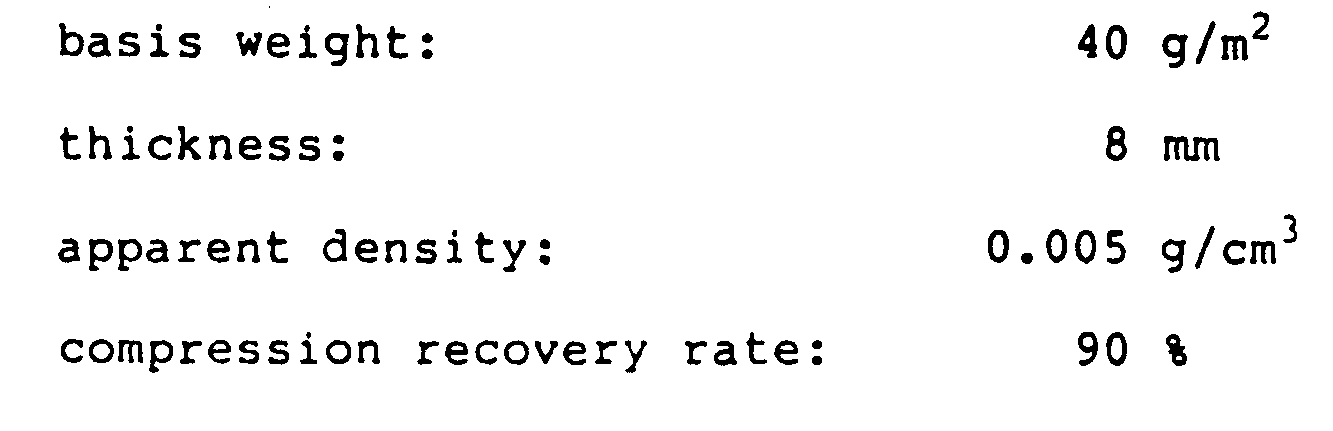
2) Preparation of Mixed Monomer Solution
[0030] A 40 % aqueous sodium hydroxide solution and pure acrylic acid (made by Sumitomo
Chemical Co., Ltd. and conforming to JIS) were mixed in a water- cooled tank having
a capacity of 40 litres, and sodium acrylate solution having a neutralization rate
of 80 % and a monomer concentration of 42 wt.% was prepared. N, N-methylene bis-acrylamide
was then dissolved in this solution in a proportion of 0.2 % by weight of the monomer.
Then, as the oxidizing radical polymerization initiator, potassium peroxide was dissolved
in said solution in a proporiton of 0.3 % by weight of the monomer. This mixed monomer
solution was adjusted at 60 C through a heat exchanger and was then introduced into
a roll coater.
3) Impregnation of Nonwoven Fabric with Mixed Monomer Solution
[0031] The aforementioned nonwoven fabric was impregnated with the mixed monomer solution
on both sides thereof by a double roll coater such that a pickup rate of 1000 wt.%
was achieved.
4) Polymerization Reaction
[0032] The above-described impregnated nonwoven fabric was let onto a stainless conveyor,
and as the reducing ahgent a 7 % aqueous sodium hydrogensulfite solution heated to
50 C was adhered uniformly to a sheet from above using a spray. This resulted in polymerization
reaction accrmpanying sudden generation of heat. The impregnated nonwoven fabric was
then passed in a falling state through the reaction tank in such a manner as to oppose
the flow of air heated to 120 C and the polymerization reaction was completed in approximately
10 seconds, and it was possible to obtain a complex containing a hihgly water-absorbent
polymer solidified in the nonwoven fabric. This complex was then passed through a
drier and dried to a moisture content of 10 %.
5) Performance of Complex
[0033] The physiological saline absorbing capacity of this complex was 55 and the residual
monomer was approximately 100 ppm. The weight of the complex was 200 g/
m2.
[0034] ** Physiological saline Absorbin Capacity; 1 g of the complex is placed in a 500 ml
beaker, 300 g of 0.9 wt.% physiological saline solution is added, and the mixture
is left as it is for 2 hours. After that the mixture is filtered by a 100-mesh filter,
and the physiological saline absorbing capacity is caluculated by the following formula;
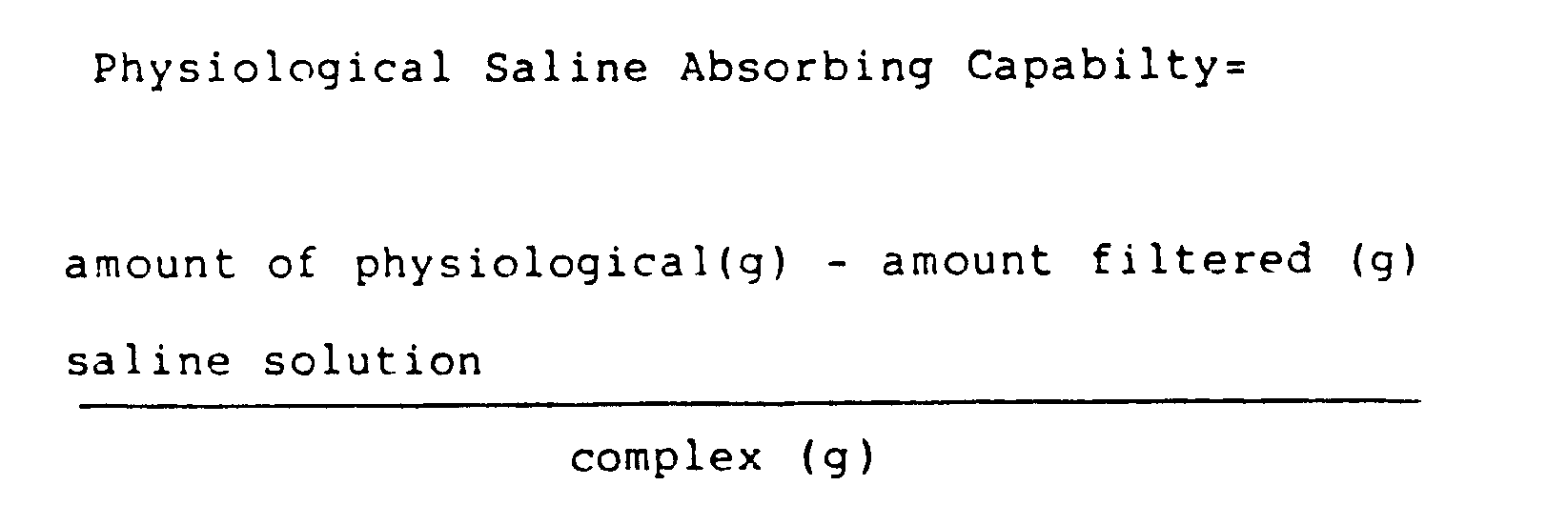
Example 2
1) Preparation of Web
[0035] A carded web was made of 80% of 8d x 51 mm hollow conjugated polyester fibers (made
by Mitsubishi Rayon Co., Ltd.) and 20% of 3d x 51 mm polyester heat-fusible fibers
(marketed by Uni-Chika Co., Ltd. under the reference Melty). This web was led continuously
into an oven wherein 250°C heated-air was circulated, and it was possible to obtain
a nonwoven fabric in which heat-fusible fibers were melted and the web- constituting
components bonded together. The porperties of the nonwoven fabric were as follows:
[0036]
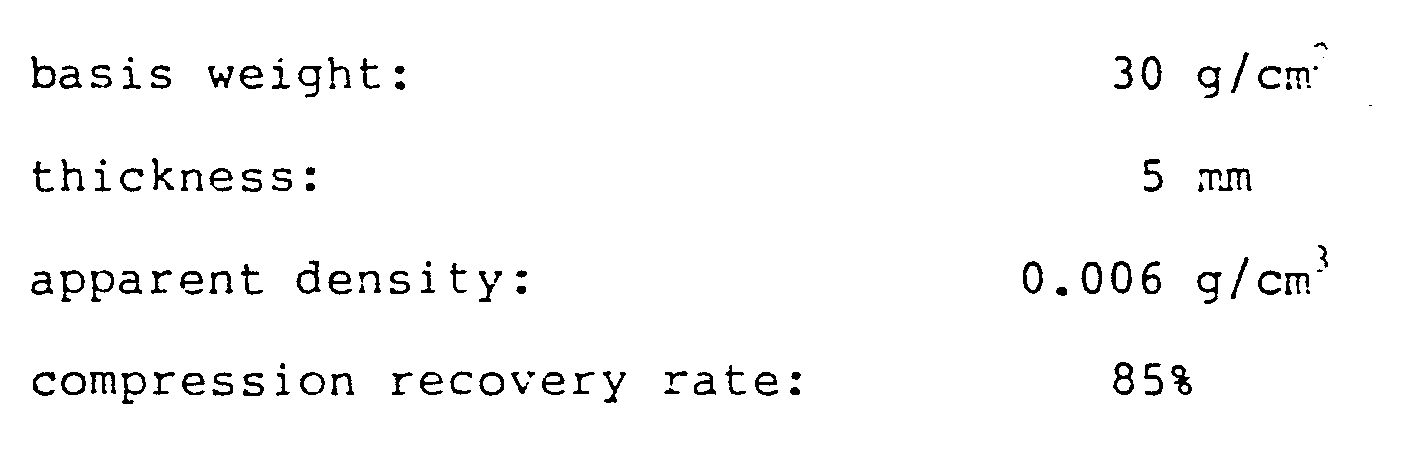
2) Preparation of Mixed Monomer Solution
[0037] A 70 wt.% aqueous potassium acrylate solution was prepared with the same apparatus
as the one used in Example 1 under cooling condition, employing sodium hydroxide.
The neutralization rate was 75%. N-methylene bis-acrylamide was then added to this
aqueous monomer solution so that its concentration would become 0.3% by weight of
the monomer. Then, as the oxidizing radical polymerization initiator hydrogen peroxide
was added to the mixed solution and was mixed so that its concentration would become
0.2% by weight of the pure monomer.
3) Adhesion of Mixed Monomer Solution to the Nonwoven Fabric
[0038] A mixed monomer solution was adhered to one side of the aforementioned nonwoven fabric
by the roll coater such that the pickup rate of about 500 wt.% was achieved.
4) Polymerization Reaction
[0039] The above-described monomer-adhered nonwoven fabric was passed in a falling state
through the reaction tank heated to 100 t. Subsequently, a 7% aqueous monoethanolamine
solution was sprayed perpendicularly on the monomer-coated surface of the nonwoven
fabric in the upper layer of the reaction tank, and the polymerization reaction was
completed in approximately 15 minutes.
Consequently, it was possible to obtain a highly water-absorbent complex having a
structure in which polymers having a larger particle size were distributed on one
side of the nonwoven fabric.
5) Performance of Complex
[0040] Physiological saline absorbing capacity: 48 residual monomers; trace
Example 3
[0041] 150g/m
2 wooden pulp mat (NBKP made by Rayonier Co., Ltd.) was bonded to both sides of the
complex obtained in Example 1 by applying water to the surface of the complex, and
pressing was effected for this structure. This structure was cut into dimensions of
25 cm (hight) x 33 cm (length). After removing the absorbent of a commercially available
paper diaper, the structure was inserted into said paper diaper and a consumer test
was carried out. It was found that the articles according to the present invention
have doubled its rate of water absorption in comprison with commercially available
ones. Thus, it was possible to obtain the absorbent in which the rate of occurrence
of leakage was extremely low even without replacement at night.