[0001] It is earlier known to manufacture sacks of embossed material. This has primarily
been done to increase the friction between filled sacks which are piled.
[0002] The embossing patterns, that hitherto have been used on sacks, have meant that the
sack material has shown bosses and, possibly, even recesses, relative to the original
plane of the material. The thought has been that, by the piling of filled sacks, the
bosses will be locked by the parts not embossed (alt. recesses) in the sack lying
closest underneath. A classification of embossing patterns earlier used for sacks,
is:
(i) raised ridges extending over the width of the paper, forming possibly a checked
pattern where only the edges of the chequers are raised. See e.g. US-A-3,904,465 and
3,283,992 and SE-A-12949/65.
(ii) out from the paper raised, delimited and, more or less large figure areas. See
e.g. FR-A-2,353,207 (76 15678), DE-A-34 37 414, US-A-2,917,223, US-A-3,495,761 and
US-A-3,411,698.
(iii) JP-A-112635/1986.
[0003] Several of these earlier known embossing patterns have in common, that they show
a plurality of, out from the plane of the paper raised, delimited figures, which are
identical. It has been found that there is a need for improvements for patterned sack
paper, i.a. regarding the friction between sacks which are piled. We have found, that
these requirements can be satisfied if the pattern, in addition, to the features shown
in, for example US-A-3 495 761 or US-A-2 917 223, (either of which could form the
basis for the preamble of claim 1), also shows the following features:
A. the patterns are straight-lined, from each other separated and over the paper plane
even distributed and provided with three, four or more sides and planar figure surface
which is parallel with and situated at a distance of 0.05-0.40 mm from the surrounding
paper surface and having a total figure area constituting ≦40% of the total paper
area and
B. the connection surface between figure surface and surrounding paper surface is
substantially perpendicular to the paper plane.
[0004] The pattern, according to the above, will even obtain a friction increasing effect
on wrapping paper when goods, that have been wrapped in the paper, are piled one above
the other.
[0005] With wrapping paper according to the invention is meant a paper, where the main part
of the fibre material (e.g. ≧70%, w/w) usually originates from a long-fibred wood,
such as spruce or pine. The fibre material is usually sulphate pulp and may be bleached
or unbleached. Recycled fibres may be present in a greater or lesser extent. Several
of the kinds of paper that are referred to, e.g. sack paper, may well be clopacked
(creped). Normally, fillers are not present in the paper, and if they to some degree
do, the amount usually is ≦10% (w/w), such as ≦5% (w/w). Among properties that are
especially important for sack paper according to the invention, may tensile energy
absorption index be mentioned, which, in the longitudinal direction of the paper ought
to be ≧0.4 kJ/kg, and in its cross direction ≧0.3 kJ/kg. The elongation in the longitudinal
direction usually is ≧1% (in case of wrapping paper of a somewhat better quality ≧2%)
and in the cross direction ≧2.0% (appreciably ≧3.5%). As upper limits for these four
properties, 7 kJ/kg, 6 kJ/kg, 20% respecively 15% are valid. High values of tensile
energy absorption index and elongation indicate high-qualitative products. It can
therefore not be excluded, that future development work may lead to, that the upper
limits will be exceeded without therefore going beyond what is regarded as sack paper
according to the present invention. Values for tensile energy absorption index and
elongation shall be determined according to ISO 1924/2-1985(E).
[0006] Henceforth, the terminology longitudinal direction = the machine direction of the
paper is current, which, in most cases, also is the main direction of the fibres.
Cross direction is perpendicular to longitudinal direction.
[0007] The figures of the embossing patterns may be straight-lined triangles (triangles),
quadrangles, pentagons etc., whereby quadrangles are preferred, and especially of
the kind in which there are sides parallel in pairs, like in parallelograms, for example
of the kind equilateral. Examples of preferred quadrangles are rhombs including squares,
rectangles and rhomboides (= a parallelogram which is neither equilateral or right-angled).
Usually, the pattern figures according to the invention show an even-numbered symmetry
axis, which, at the most, is four-numbered. In one and the same embossing pattern
it is preferred, that all the figures of the pattern are identical, even if, for some
patterns, may occur, that an improved friction paper to paper is achieved if 2, 3,
4 or more different kinds of figures exist.
[0008] The identical figures are evenly distributed over the patterned surface. The meaning
of that is that, if a straight line is drawn over the surface of the paper and is
allowed to intersect a plurality of figures in the same way, the distance between
beside each other lying identical figures that are intersected by the line, always
shall be the same. The corresponding distance for other similar lines must not, however,
be the same as for the line first mentioned.
[0009] The paper according to the invention may, along one or both of its longitudinal sides,
have an outer zone lacking the evenly distributed embossing figures. Alternatively,
the figures in these zones may be less distinct because they are not raised as much
out of the original paper plane as the more central parts, or because the angle between
figure plane and the connection surface to the original paper plane is greater than
90°. Outer zones of this kind are 1-2 dm, if they exist in the wrapping paper.
[0010] Normal pattern frequency usually is below 500, such as below 200 identical figures/dm²
As an example, 10-100 may be mentioned, such as 20-60 identical figures/dm². The total
pattern area is ≦40% and usually ≧0.5% (preferably above 1%) of the total pattern
area. It has been shown, that very good improvements in the friction paper to paper
may be achieved, if the total figure area is below 30%, such as below 20% or below
10% of the total pattern area.
[0011] By improved friction properties is meant, that the improvement is ≧1%, such as ≧5%,
relative to corresponding unembossed paper (the friction coefficient for paper to
paper measured in any direction). The way of measuring is given in the experimental
part.
[0012] If two identical papers according to the invention are placed with their upper sides
against each other, substantially most of the identical figures (≧90%) in one of the
papers, ought to be placed between corresponding figures in the other paper in that
way, that slipping will be made more difficult (the friction will be increased) because
the figures in one of the papers will hit the corresponding figures in the other.
The greatest distance between two sides in one and the same figure shall, therefore,
in many of the most preferred embodiments, be longer than the shortest distance to
the closest lying figure in the same paper. The mentioned longest distance always
is a distance corner-to-corner, which in a right-angled triangle always is a side
and in a right-angled polygon, always a diagonal.
[0013] The orientation of the pattern figures shall preferably be of that kind, that the
machine direction of the paper divides an angle in the figures in substantially two
(+/- 10°) equally large angles. If an acute angle exists in the figures it is preferably
such a one that is divided.
[0014] In the most preferred embodiment the figures consist of parallelogram. These are
shown in figure A and can be defined by the help of a checked pattern, which arises
if a first number of parallel, straight lines l₁, l₂, l₃....l
n are intersected by a second number of parallel, straight lines l'₁, l'₂, l'₃...l'
n at an angle β . The lines extend over the width of the paper. n and n are integers
which may be even or uneven and are always greater than 10. The exact number of lines
is determined by the distance between them, their slope in relation to the width and
the width of the sack paper. The perpendicular distance between the lines in one group
are alternating, and is
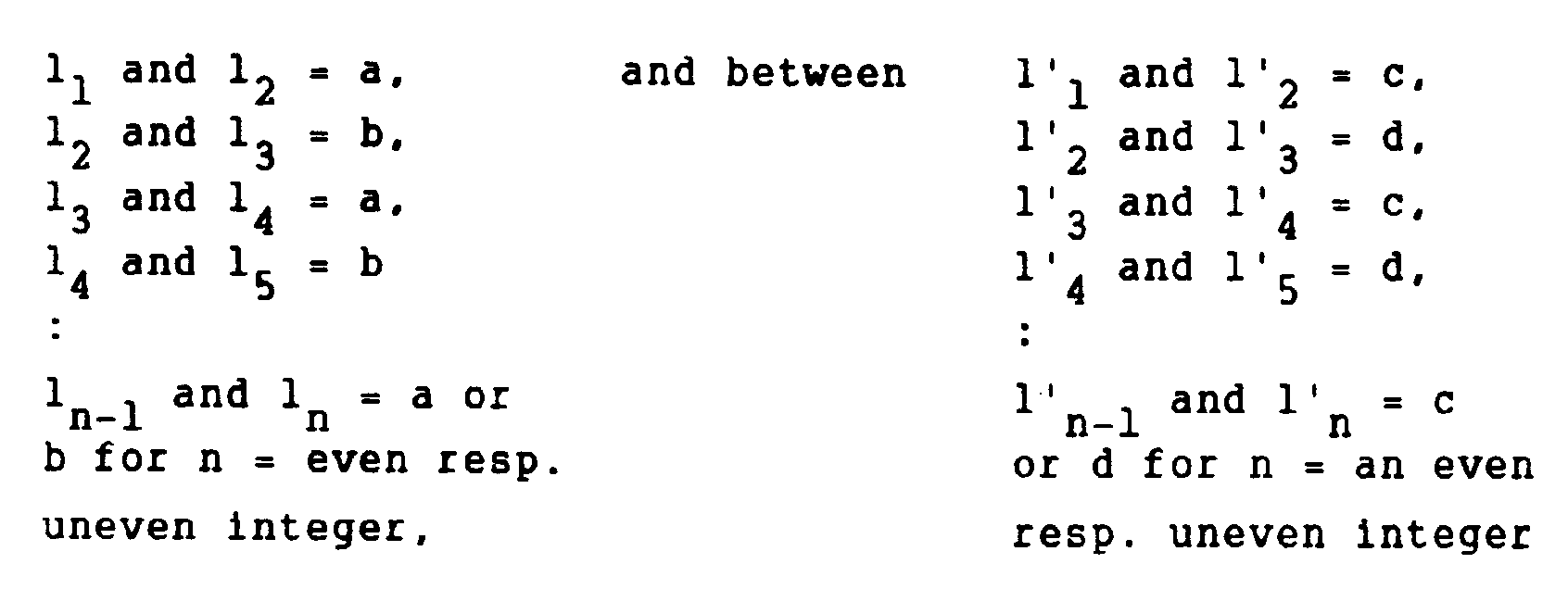
[0015] In general it is valid that the distances a, b, c and d ≦5 cm, preferably ≦3 cm,
and that a ≦ b, and c ≦ d. In one important embodiment is a = c and b = d, with preference
that a at the same time is ≦ b. The figures of the pattern are defined as the whole
checked pattern minus the area between lines present at the distances b and d from
each other. The most studied embodiments of the invention, on the priority day of
the application, have a, b, c and d always been ≧ 0.05 cm, such as ≧ 0.1 cm.
[0016] The angle β fulfills the condition 10° ≦ β ≦ 170°, such as 10° ≦ β ≦ 90° or 90° ≦
β ≦ 170°.
[0017] It is preferred that the lines l₁, l₂, l₃.....l
n have a positive slope and that the lines l'₁, l'₂, l'₃ ...l
n have a negative slope compared with the machine direction of the paper. The angle
β is readily divided in half by the machine direction.
[0018] The Figures 1-6 show examples of patterns in question seen from above. The machine
direction of the papers is indicated with a double-arrow [<-->].
[0019] Figure 1 shows a paper according to the invention where a=c≦b=d. The angle β is 60°
and the figure frequency is 39 pieces/dm². The symmetry axis is two-numbered. The
machine direction divides the angle β in half.
[0020] Figure 2 shows a paper patterned in a similar manner. a=c≦b=d. The angle β is 30°
and is divided in half by the machine direction. The figure frequency is 28 pieces/dm².
The symmetry axis of the figures is two-numbered.
[0021] Figure 3 also shows a paper according to the invention, where a=c≦b=d The angle β
is 30° and is divided in half by the machine direction. The symmetry axis of the pattern
is two-numbered. The figure frequency is 48 pieces/dm².
[0022] Figure 4 shows a paper where a=c≦b=d. The angle β is 90° and is divided by the machine
direction in one angle which is 0° and one which is 90°. The symmetry axis is four-numbered.
The figure frequency is 49 pieces/dm².
[0023] Figure 5 shows a paper whose pattern is rather like the one in the preceding figure,
but whith smaller squares and greater figure frequency.
[0024] Figure 6 shows a paper according to the invention where a ≦c ≦d ≦b. The angle β is
90° and is divided in half by the machine direction. The symmetry axis of the figures
is two-numbered. The figure frequency is 32 pieces/dm².
Manufacturing the paper of the invention and apparatus to be used by the manufacturing.
[0025] One aspect of the invention is a method for manufacturing a wrapping paper, preferably
sack paper, containing the pattern defined above, by way of embossing a web of sack
paper. The paper web as such is manufactured in a way for wrapping paper known
per se, and means in the preferred embodiments of the invention a clopacking stage. The
embossing is carried out by allowing the paper web, after a possibly clopacking, pass
through a roll nip, where one of the rolls is softer than the other (pressing- respectively
embossing roll).
[0026] The harder of the rolls (the embossing roll) has an envelope surface which suitably
is made of metal (e.g. steel or cast iron) or another hard material. Its envelope
surface shows for the wrapping paper of the invention said pattern provided with evenly
distributed, raised and identical figures with differences which are due to that the
envelope surface not is made of paper. Starting from the earlier mentioned description
of the pattern of the paper, thus what applies is, that "paper" shall be substituted
with "envelope" alternatively with "envelope surface" and "the machine direction of
the wrapping paper" with "the tangential direction of movement of the envelope surface
when the roll is rotating around its axle'. As a rule, the raise of the figures shall
be somewhat larger than the corresponding raise in the embossed paper. The interval,
which usually is suitable for the roll, therefore is 0.06-0.45 mm instead of 0.05-0.40
mm that is applied for the paper. The roll may well be constructed so it can be heated,
in order that the paper will dry as fast as possible after the embossing. The paper
will partly then more easily lift from the roll and the embossing pattern will partly
be freezed more effectively, which, at the same time, makes it more stable. The best,
therefore, is if the roll is constructed in a usual way as a drying cylinder in a
paper machine, i.e. hollow with an inlet for hot steam (approx. 125-190°C) and outlet
for condensate and so-called "spoiler bars" to improve the withdrawal of condensate
and to create turbulence in the condensate film which is obtained on the inner walls
of the cylinder. The roll is suitably made from a roll provided with a smooth envelope
surface by brooching out recesses corresponding to the surface between lines with
the distances b and d between each other (see the above). The depth of the recesses
lies in the above mentioned interval.
[0027] The pressing roll is made of elastic material which permits that the figures of the
embossing roll can be completely impacted in the material when the rolls are pressed
against each other. An excellent material is rubber, e.g. hard rubber. The pressing
roll is suitably cambered to permit an even line pressure along itself during the
embossing.
[0028] A suitable embossing pressure (kp/cm² depends on factors such as the raise of the
figures out of the envelope surface, the hardness of the pressing roll, the thickness
of the paper, choice of fibre material, speed in the head box etc. Suitably, the embossing
pressure is 1-10 kp/cm². In order to obtain an effective embossing, which results
in a stable pattern, the embossing most suitably should be carried out at a dry solids
content of 60-80%, preferably 65-70% (w/w). After the embossing the paper is dried
to a dry solids content of above 90% (w/w).
The sack of the invention and the manufacturing thereof
[0029] One aspect of the invention is a sack, which surface wholly or partially shows the
embossing pattern mentioned above. The sack material may wholly or partially be made
of plastic or paper. The pattern consists of a plurality of out of the surface of
the sack raised, delimited patterns which are identical. Characterizing features are;
A. the patterns are straight-lined, from each other separated and evenly distributed
over the patterned surface and are provided with three, four or more sides and a planar
figure surface which is parallel with, and situated at a distance of 0.05-0.40 mm
from the surrounding sack surface and with a total figure area that constitutes ≦40%
of the total paper area and
B. the connection surface between figure surface and the surrounding sack surface,
is substantially perpendicular to the sack surface.
[0030] Otherwise, the same is valid for the sack as for the embossing pattern of the paper
with regard to that the embossed surface does not need to be made of paper. In the
case that the embossed surface does not have any machine direction, with the machine
direction of the paper is meant the height direction of the sack. If only parts of
the sack surface are covered with the embossing pattern, it is suitably on the upper
or lower side of the sack, i.e. those sides of the sack that by piling lies against
other sacks.
[0031] The sack according to the invention is constructed in a manner known for sacks
per se, in which the sack material may consist of one to six different layers, so called
sheets, in which the outermost sheet, according to the invention, preferably is made
of paper. The embossing pattern is situated on the outer layer or, as an alternative,
is glued on in the form of embossed sheet of plastic or paper.
[0032] By the manufacturing of sacks, one is starting from one or more rolls of web formed
sack material, which are just as broad as the circumference of the sack including
that part (for example paste joints) which shall be used to form the web material
into a longitudinal tube. For each sheet a roll is used, by which that web material
which shall be in the outside of the sack (outer web) shall be embossed with any of
the patterns given above, or if it is not, it is moistened, embossed and dried in
connection to the unwinding. The different webs of material are stored, by the unwinding,
continuously one upon the other, whereafter the in that way obtained, possibly multiple
sheeted web material, continuously is formed and joined together (pasted together)
into a tube. This is later cut into suitable sack lengths, whereafter one of the ends
of the respective lengths, is joined together to form the bottom of the sack. Alternatively,
the web material is cut to sack length, which therafter is joined together into a
tube and is sealed in one end.
[0033] The scope of the invention is defined by the patent claims.
Experimental part
1. Abstract
[0034] Sack paper, taken from the paper machine at a dry solids content of approx. 65%,
has been embossed in a laboratory press under conditions intended, as far as possible,
to be equal to embossing in the paper machine.
[0035] The static friction paper to paper of the embossed papers, tensile strength, flexure,
tensile energy absorption, and air resistance were tested.
[0036] The friction increases while the tensile energy absorption decreases and the air
resistance increases by the embossing of the sack paper. According to the test result,
recommended are the patterns D, large squares, B, oblong sparse rhombes, C, oblong
dense rhombes and oblong rectangles in now said order.
2. Putting into practise
[0037]
2.a Embossing
Paper in the form of sheets were taken out from the paper machine at a dry solids
content of approx. 65% during change of quality. The sheets were stored in plastic
bags in order to prevent drying until the embossing had been carried out.
The paper sheets were embossed under static conditions in a laboratory press by the
help of a steel plate provided with a desired pattern. Patterns that were studied,
are evident from the figures 1-6. The embossing was carried out at the pressure 3
kp/cm² during the times 1 s and 5 s.
The sheets were thereafter dried against a drying cylinder between two rigid sheets
of blotting-paper, in that way, that they were kept stretched.
2.b Tensile strength, extension, tensile energy absorption were determined according
to ISO 1924/2-1985 (E) and air resistance according to ISO 3687-1976.
2.c Determination of friction coefficient
This was carried out according to TAPPI T:503, by means of an inclined plane from
Buchel van der Korpat, Holland. The friction, overside against overside, was determined
between two strips that had been cut out of the conditioned sheets in their longitudinal
respectively their cross direction. The tests were repeated five times for each pattern.
The mean value [Mv] of the obtained friction coefficients is evident from Table 1.
By cutting the strips in other directions and/or to match them together in other ways,
the friction coefficient may be determined also for other directions in the sack paper.
3. Results
[0038] The tensile strength is scarcely affected by the embossing while the extension seems
to decrease somewhat, which results in a tensile energy absorption decrease of up
to 20% in the longitudinal, and up to 16% in the cross direction.
[0039] The air resistance increases up to 12 units, from 29 to 41 s.
[0040] The friction increases up to 0.11 units from 0.63 to 0.74.
- Figure 1
- = Rhombs 4 x 6 mm, 39 pieces/dm²
- Figure 2
- = Rhombs 3 x 9 mm, 28 pieces/dm²
- Figure 3
- = Rhombs 3 x 9 mm, 48 pieces/dm²
- Figure 4
- = Squares 5 mm, 49 pieces/dm²
- Figure 5
- = Squares 3,5 mm, 49 pieces/dm²
- Figure 6
- = Rectangle, diagonally, 32 pieces/dm²
- Figure 0
- = Unembossed paper
1. Embossed wrapping paper, preferably sack paper, whose embossing pattern shows a plurality
of, delimited, identical figures which are raised out of the paper plane,
characterized in that
A. the patterns are straight-lined, separated from each other evenly distributed over
the paper plane and provided with three or more, preferably four sides and a planar
figure surface, which is parallel to and situated at a distance of 0.05-0.40 mm from
the surrounding paper surface and with a total figure area which constitutes ≦40%,
preferably ≦20%, of the total paper area that has been embossed, and in that
B. the connection surface between figure surface and surrounding paper surface is
substantially perpendicular to the paper plane.
2. Embossed wrapping paper according to claim 1,
characterized in that the figures consist of parallelograms defined as chequers in the checked
pattern that is obtained if a number of parallel lines (l₁, l₂, l₃, l₄, l₅,.....l
n) are intersected by a number of other parallel lines (l'₁, l'₂, l'₃, l'₄, l'₅, .........l'
n) under an angle β, where n and n are integers greater than 10 and where the perpendicular
distance between
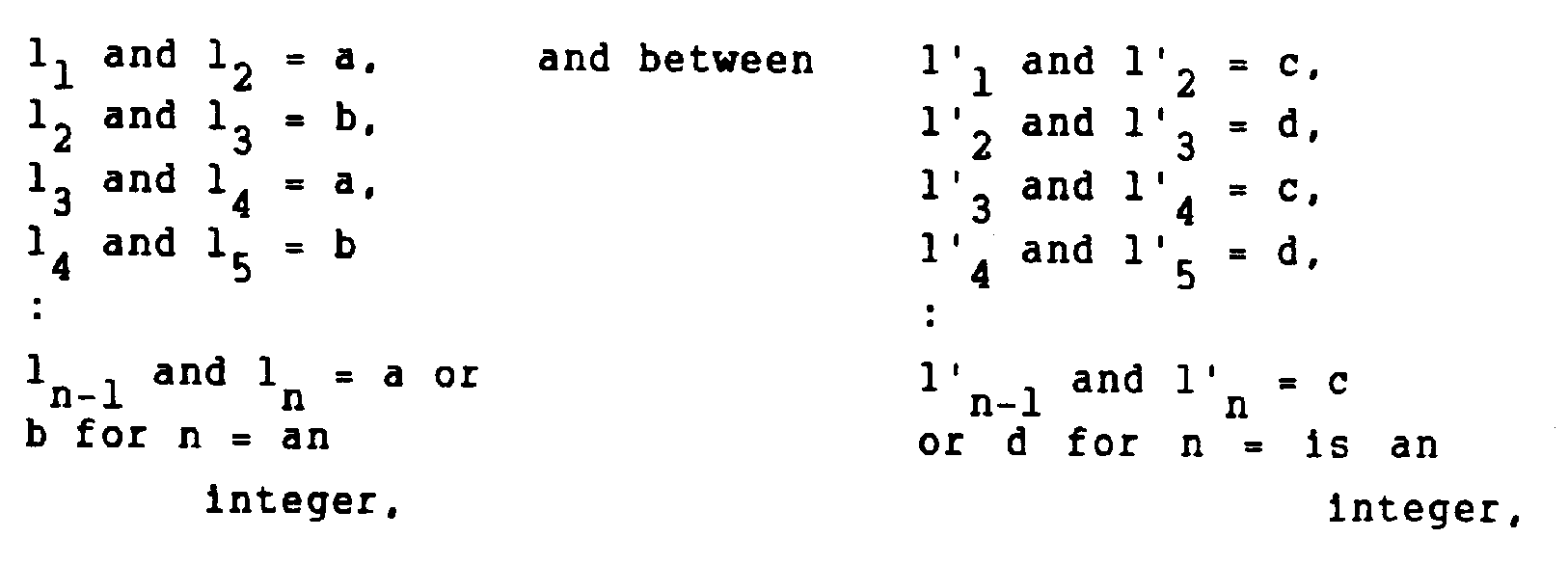
where the figures in the pattern are defined as the total area over which the lines
extend, minus the area between lines at the distance b respectively d from each other,
and where a, b, c, d are chosen so, that a≦b and c≦d.
3. Embossed wrapping paper according to claim 2, characterized in that a = c and b = d, preferably with a≦b.
4. Embossed wrapping paper according to any one of the claims 2-3, characterized in that the lines l₁, l₂ ....ln have a positive slope and the lines l'₁, l'₂ ...l'n have a negative slope against the machine direction of the paper, preferably with
the same absolute value and that the angle is 10° ≦ β ≦170°, preferably 10°≦ β ≦90°.
5. Embossed wrapping paper according to claim 1, characterized in that a corner-to-corner distance, in appropriate cases a diagonal distance, in
respective figure is longer than the shortest distance to the figure lying closest
nearby.
1. Geprägtes Packpapier, vorzugsweise Sackpapier, dessen Prägemuster eine Vielzahl abgegrenzter,
identischer Figuren zeigt, die aus der Papierebene herausgehoben sind, dadurch gekennzeichnet,
daß
A. die Muster geradlinig, voneinander getrennt, gleichmäßig über die Papierebene verteilt
und mit drei oder mehr, vorzugsweise vier Seiten und einer ebenen Figurenoberfläche
versehen sind, die parallel und in einem Abstand von 0,05 - 0,40 mm zu der umgebenden
Papieroberfläche angeordnet ist, und mit einer gesamten Figurenfläche, die ≦ 40%,
vorzugsweise ≦ 20% der gesamten geprägten Papierfläche ausmacht, und daß
B. die Verbindungsoberfläche zwischen Figurenoberfläche und umgebender Papieroberfläche
im wesentlichen senkrecht zur Papierebene liegt.
2. Geprägtes Packpapier nach Anspruch 1, dadurch gekennzeichnet, daß die Figuren aus
Parallelogrammen bestehen, die als Karomuster in dem Gittermuster hervortreten, das
erhalten wird, wenn eine Anzahl paralleler Linien (l₁, l₂, l₃, l₄, l₅,.....l
n) von einer Anzahl anderer paralleler Linien (l'₁, l'₂, l'₃, l'₄, l'₅,.....l'
n) unter einem Winkel β geschnitten werden, wobei n und n ganze Zahlen größer als 10
sind und wobei der im rechten Winkel gemessene Abstand zwischen
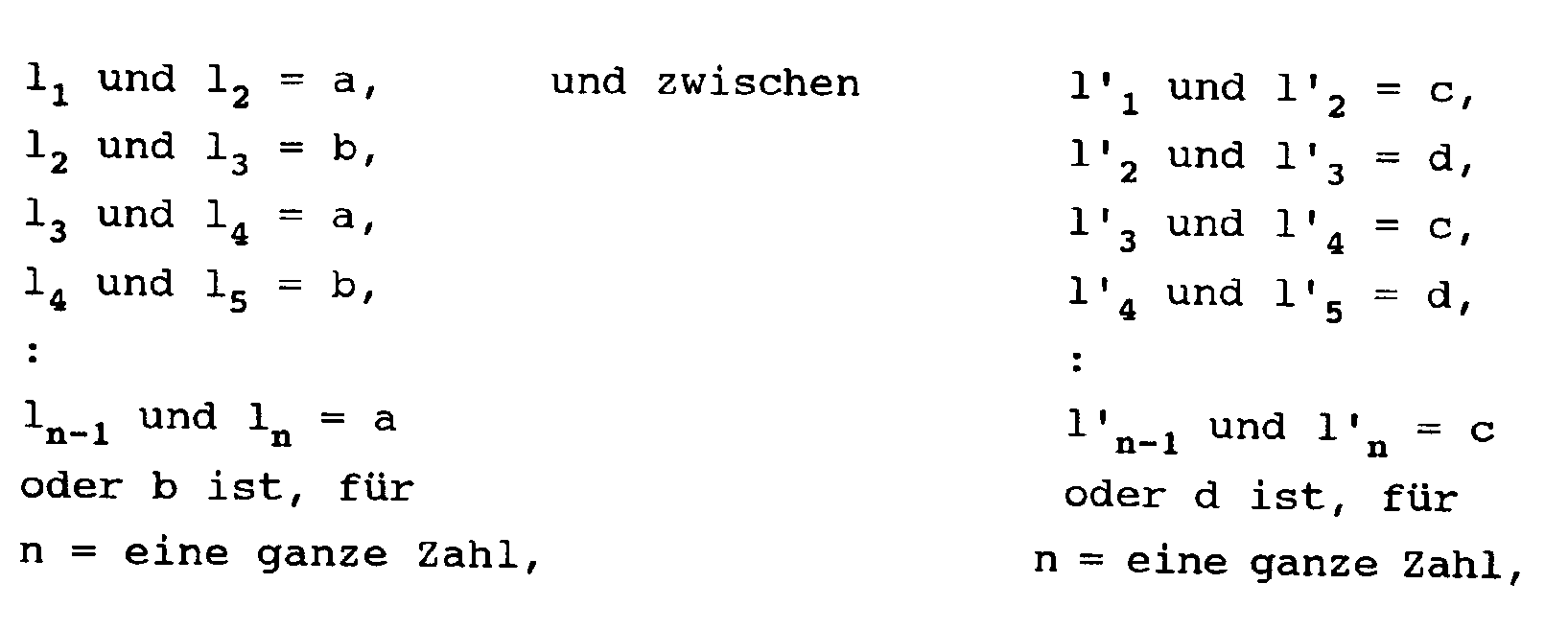
wobei die Figuren in den Mustern als Gesamtfläche definiert sind, über die sich die
Linien erstrecken, abzüglich der Fläche zwischen Linien mit einem Abstand b bzw. d
voneinander, und wobei a, b, c, d so gewählt sind, daß a ≦ b und c ≦ d ist.
3. Geprägtes Packpapier nach Anspruch 2, dadurch gekennzeichnet, daß a = c und b = d
ist, vorzugsweise mit a ≦ b.
4. Geprägtes Packpapier nach irgendeinem der Ansprüche 2 - 3, dadurch gekennzeichnet,
daß die Linien l₁, l₂ .....ln eine positive Neigung und die Linien l'₁, l'₂ .....l'n eine negative Neigung gegen die Maschinenrichtung des Papiers haben, vorzugsweise
mit dem gleichen absoluten Wert, und daß der Winkel 10° ≦ β ≦ 170°, vorzugsweise 10°
≦ β ≦ 90°, beträgt.
5. Geprägtes Packpapier nach Anspruch 1, dadurch gekennzeichnet, daß ein Eck-zu-Eck-Abstand,
in bestimmten Fällen ein diagonaler Abstand, in einer betroffenen Figur länger als
der kürzeste Abstand zu der nächstliegenden Figur ist.
1. Papier d'emballage gaufré, de préférence du papier pour sacs, dont le motif de gaufrage
est pourvu de plusieurs figures identiques, délimitées, qui sont saillantes hors du
plan du papier, caractérisé par le fait que:
A.- les motifs sont constitués par des lignes droites, séparés les uns des autres,
répartis uniformément sur la surface à motifs et sont pourvus de trois côtés ou plus,
de préférence quatre, et d'un même plan de surface pour les figures qui est parallèle
à la surface du papier qui les entoure et situé à une distance de 0,05-0,40 mm de
celle-ci, ainsi que d'une superficie totale des figures qui constitue ≦ 40%, de préférence
≦ 20%, de la superficie totale du papier qui a été gaufré; et par le fait que:
B.- la surface de liaison entre la surface des figures et la surface du papier les
entourant est sensiblement perpendiculaire au plan du papier.
2. Papier d'emballage gaufré selon la revendication 1, caractérisé par le fait que les
figures sont constituées par des parallélogrammes définis comme un quadrillage dans
le motif à carreaux qui est obtenu si un nombre de lignes parallèles (l1, l2, l3,
l4, l5,....ln) sont intersectées par un nombre d'autres lignes parallèles (l'1, l'2,
l'3, l'4, l'5,....l'n), selon un angle β, où n et n sont des nombres entiers supérieurs
à 10, et où la distance perpendiculaire entre
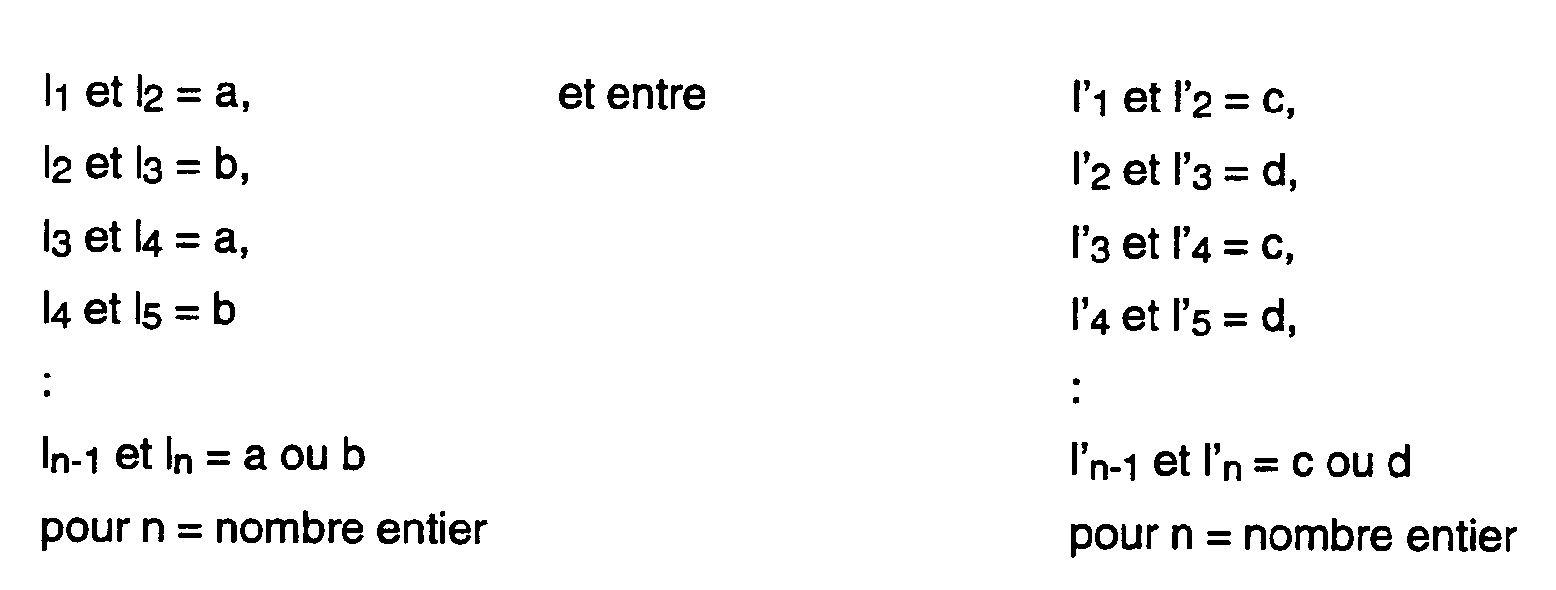
où les figures du motif sont définies comme étant la superficie totale sur laquelle
s'étendent les lignes, moins la superficie comprise entre les lignes se trouvant aux
distances b et d, respectivement, les unes des autres, et où a, b, c, d sont choisis
de manière telle que a ≦ b et c ≦ d.
3. Papier d'emballage gaufré selon la revendication 2, caractérisé par le fait que a
= c et b = d, avec de préférence a ≦ b.
4. Papier d'emballage gaufré selon l'une quelconque des revendications 2 à 3, caractérisé
par le fait que les lignes l'1, l'2,....l'n ont une inclinaison positive, et les lignes
l'1, l'2....l'n une inclinaison négative, par rapport au sens machine du papier, avec
de préférence la même valeur absolue, et par le fait que l'angle vaut:10° ≦ β ≦ 170°,
de préférence 10° ≦ β ≦ 90°.
5. Papier d'emballage gaufré selon la revendication 1, caractérisé par le fait qu'une
distance d'angle à angle dans une figure respective, dans des cas propres, une distance
en diagonale, est plus longue que la distance la plus courte à la figure la plus proche.