[0001] This invention relates to improvements in the manufacture of carbon fiber from polyacrylonitrile
polymers. This invention, more particularly, relates to producing high quality and
performance carbon fiber at significant cost savings through enhancing throughputs
of precursor materials used in making such carbon fiber. This invention, still more
particularly, relates to the discovery and exploitation of a limited temperature range
wherein a multitude of filaments of the polyacrylonitrile polymer, such multitude
often called "carbon fiber (polyacrylonitrile) precursor" or "precursor" for short,
may be safely stretched up to four or more times its original length after formation
but prior to the oxidation used in making the carbon fiber.
[0002] PAN-based carbon fiber (for purposes of describing this invention hereafter called
"carbon fiber") is a well-known material that is over 85% by weight elemental carbon.
Such carbon fiber is notable for enabling manufacture of light weight composite materials
and other articles of manufacture of exceptional tensile strength and modulus.
[0003] Increased useage coupled with incremental improvements in the processes which manufacture
carbon fiber have dramatically reduced its cost compared to when it was first introduced
several years ago. Moreover, the attractiveness of light weight structures comprising
carbon fiber has increased significantly due to recent marked improvements in the
material properties of the carbon fiber and resin materials used in making the structures.
[0004] Of late, however, despite even wider potential useage of carbon fiber through advances
in material properties, continued significant decreases in its price, at one time
dramatic and routine, have not proceeded as expected. One reason is that reliable
manufacture of high quality carbon fiber remains an art; skillful control of process
conditions used in making it and repeated testing for assuring quality remain a manufacturing
requisite. Furthermore, recent advances in material property performance have been
achieved through use of finer denier precursor, i.e., small diameter filaments, and
such finer denier precursor requires the same or greater amount of precursor process
control in making it but at generally lower throughputs. Accordingly, while the processing
quality and performance characteristics of carbon fiber have been maintained and even
improved over the years, the cost of making such high quality carbon fiber has not
been reduced to the degree possibly anticipated, particularly with respect to newer
carbon fibers made with finer denier precursor.
[0005] It is evident that increases in the line speeds of the precursor and carbon fiber
manufacturing processes reduce cost per weight of the final carbon fiber. However,
further increases in line speeds, especially in precursor manufacturing speeds, increase
the risk of lowering the quality of the resultant carbon fiber, particularly since
precursor line speeds have generally approached their maximum limits with conventional
equipment.
[0006] The cost of making carbon fiber under current procedures can be divided into two
categories. First, there is the cost of making the precursor, e.g. material costs
of acrylonitrile, other monomers and solvent used in making the polyacrylonitrile
polymer, costs associated with spinning the precursor, costs associated with treating
the spun filaments such as stretching in cold and hot water and steam, and costs associated
with process control and testing. Other costs in making carbon fiber include the costs
of oxidizing and then carbonizing the precursor, costs associated with the process
control of such oxidation and carbonization and testing costs. Since only about half
by weight of the precursor becomes carbon fiber, it can be seen that reduction per
pound of precursor manufacturing costs results in about twice that reduction per pound
in carbon fiber.
[0007] Exemplary description of making precursors useful for producing carbon fiber appear
in UK 1,324,772, U.S. Patents 4,100,004; 4,001,382; 4,009,248; 4,113,847; 4,397,831;
4,448,740; 4,452,860 and Japanese Applications 53-24427 and 59-272341. These publications
describe making precursors wherein polyacrylonitrile filaments are stretched in hot
water, steam and air prior to oxidation. For example, in the "Example of Application
1" of Japanese Application 59-272341, wet spun polyacrylonitrile filaments are said
to have been stretched over five (5) times over a hot water bath, washed and dried
and then drawn 1.3 times at 170°C using dry heat prior to oxidation. U.S. Patent 4,104,004,
on the other hand, discloses stretching up to 75% between 100°C and 160°C, e.g. 130°C.
[0008] Now, in accordance with this invention, a limited temperature range has been discovered
whereby the precursor may be stretched to four or more times its original length in
air, steam or other fluid medium. As a result, greater throughput of precursor can
be achieved under the same process control procedures used at less than half the throughputs
while at the same time, only marginally increasing the cost of producing carbon fiber
through such stretching. Furthermore, since the stretching achieved in this limited
temperature range can be quite high, certain stretching during manufacture of the
precursor may be reduced or even eliminated thereby allowing still further increase
in throughputs and reductions in precursor manufacturing costs.
[0009] This invention provides a process for making carbon fiber in the form of a tow or
bundle comprising a multitude of high strength carbon fiber filaments, said process
comprising (a) forming a spinning solution comprising a polyacrylonitrile polymer
in a solvent for such polymer, (b) extruding said polymer through a die to provide
a multitude of continuous filaments, (c) drawing these filaments to a longer length
in making a precursor tow, and (d) oxidizing and then carbonizing said precursor tow
in a series of ovens and furnaces to provide said carbon fiber, which comprises: (i)
selecting precursor tow that is capable of being stretched at a limited temperature
range of 140°C to below the temperature causing oxidation of said precursor tow; (ii)
heating said precursor tow to a temperature within a limited temperature range above
140°C and below the temperature causing oxidation of said precursor tow; and (iii)
stretching said precursor tow heated to said temperature so that its length after
stretching is at least twice its length prior to stretching. Preferably, the precursor
is stretched in the limited temperature range in air. Moreover, after the polyacrylonitrile
polymer is extruded through the die, stretching prior to oxidation preferably consists
essentially of stretching in the limited temperature range preceded by stretching
at temperatures below boiling water temperature. Also, such stretching prior to stretching
in the limited temperature range preferably comprises stretching under circumstances
that plasticize the filaments.
[0010] Figure 1 illustrates the thermal response curve for a preferred precursor of this
invention.
[0011] Figure 2 illustrates diagramatically a device that is useful in practice of this
invention.
[0012] Figures 3, 4 and 5 illustrate properties of precursors heated to a temperature in
a range useful for practice of this invention.
[0013] The polyacrylonitrile precursor useful in making carbon fiber in accordance with
this invention comprises a polymer made by addition polymerization, either in solution
or otherwise, of ethenic monomers (i.e. monomers that are ethylenically unsaturated),
at least about 80 mole percent of which comprise acrylonitrile. The preferred polyacrylonitrile
precursor polymers are copolymers of acrylonitrile and one or more other monofunctional
ethenic monomers. Available ethenic monomers are diverse and include, for example,
acrylates and methacrylates; unsaturated ketones; and acrylic and methacrylic acid,
maleic acid, itaconic acid and their salts. Preferred comonomers comprise acrylic
or methacrylic acids or their salts, and the preferred molar amounts of the comonomer
ranges between 1.5 and 3.5%. (See U.S. Patent 4,001,382 and U.S. Patent 4,397,831
.)
[0014] The polyacrylonitrile precursor polymers suitable for making carbon fiber hereof
are soluble in organic and/or inorganic solvents such as dimethylsulfoxide, dimethyl
formamide, zinc chloride or sodium thiocyanate solutions. In a preferred practice
of making a polyacrylonitrile precursor for use in making the carbon fibers hereof,
a solution is formed from water, polyacrylonitrile polymer and sodium thiocyanate
at exemplary respective weight ratios of about 60:10:30. This solution is concentrated
through evaporation and filtered to provide a spinning solution. The spinning solution
preferably comprises about 15% by weight of the polyacrylonitrile polymer.
[0015] The spinning solution is passed through spinnerets using dry, dry/wet or wet spinning
to form the polyacrylonitrile precursor. The preferred polyacrylonitrile precursor
is made using a dry/wet spinning wherein a multitude of filaments are formed from
the spinning solution and pass from the spinneret through an air gap or other gap
between the spinneret and a coagulant preferably comprising aqueous sodium thiocyanate.
After exiting from the coagulant bath, the spun filaments are washed and then stretched
again to several times their original length in hot water and steam. (See U.S. Patent
4,452,860 and Japanese Application 53-24427 [1978].) In addition, the polyacrylonitrile
precursor is treated with sizing agents such as silane compounds (see U.S. Patent
4,009,248).
[0016] The polyacrylonitrile precursor (preferably silane sized) is in the form of tows
in bundles comprising a multitude of filaments (e.g. 1,000, 10,000 or more). The tows
or bundles may be a combination of two or more tows or bundles, each formed in a separate
spinning operation.
[0017] A thermal response curve in air of a preferred polyacrylonitrile precursor suitable
for use in making the carbon fibers of this invention is shown in Figure 1. This precursor
is made from a monomer composition comprising about ninety eight mole percent (98%)
acrylonitrile and about two mole percent (2%) methacrylic acid.
[0018] The tex (denier) per filament of the polyacrylonitrile precursors desirably ranges
between 0.07 (0.6) and 0.7 (6.0) or higher. The particular denier of the polyacrylonitrile
precursor chosen influences subsequent processing of the precursor into carbon fiber
hereof. For example, larger tex (denier) precursor, e.g. 0.148 tex (1.33 denier) per
filament or above precursor is preferably stretched at temperatures below 200°C (e.g.
about 150 - 160°C) to reduce its tex (denier) to less than 0.09 (0.8) prior to significant
oxidation. Greater stretching in the limited temperature range reduces the need for
such stretching in later, e.g., during oxidation, manufacturing steps in making the
carbon fiber.
[0019] Through stretching at temperatures between 145 and 165°C, the resultant precursor
is up to 4.0 times or more its original length; and due to the minimal reaction at
temperatures within this range may be in amounts selectively calculated in advance
to provide the denier desired for subsequent oxidation and stabilization. For example,
a 0.24 tex (2.2 denier) per filament precursor may be stretched to twice its original
length to yield a 0.12 tex (1.1 denier) per filament material by a Stretch Ratio (S.R.)
of 2 according to the following formula:

where L
o is length out, L
i is length in (i.e. original length), d
S is original tex (denier) and d
N is new tex (denier). Desired stretch ratio (S.R.) may be achieved by drawing the
Desired stretch ratio (S.R.) may be achieved by drawing the precursor faster through
the desired heated zone (e.g. temperature between 150°C and 160°C) that it is permitted
to enter this zone.
[0020] Figure 2 illustrates in schematic form the design of stretching device 20 useful
in practice of this invention. Device 20 of Figure 2 comprises supports 22 which carry
platform 24 on which inlet roll stack 26, steam heated roll stack 28, steam heated
tube 30 and outlet roll stacks 32 and 34 are mounted.
[0021] Steam heated tube 30 is heated by steam passing through a jacket surrounding the
tube walls. In addition, gas inlet tube 36 is mounted to the downstream end of steam
heated tube 30 and provides for entry of heated air or other gas when countercurrent
gas heating is used in heat-up of the precursor traveling between about inlet and
outlet roll stacks 26, 34. Control 38 monitors inlet and outlet counter-rolls 40,
42 which can also measure tension and line speed as read out in control 38. Access
port 44 permits stringing precursor through steam heated roll stack 28.
[0022] Steam heated roll stack 28 is optionally used in providing preliminary heat transfer
to the precursor as it travels around the steam heated rolls 28. This preliminary
heat transfer permits shorter heated lengths of steam heated tube 30, if desired.
[0023] Features of the Device 20 of Figure 2 such as length of steam heated tube 30, use
or non-use of steam heated roll stack 28 and gas flow velocity, direction and placement
of inlet tube 36 as well as temperatures used for heating thereof are selected as
a matter of design choice so as to provide rapid heat-up of the precursor as well
as compatibility with the oxidation and carbonization line speeds in the carbon fiber
process. Initial tow spacing that ranges preferably between 2 and 4.5 tows per 2.54
centimeter for 12000 filament tows are preferred for flow of heat transfer medium,
such spacing advantageously inherently increasing as stretching proceeds.
[0024] The polyacrylonitrile precursor after stretching in the limited temperature range
according to this invention, is oxidized in one or more ovens preferably maintained
at temperatures between 200°C and 300°C. A variety of oven geometries are known to
provide appropriate oxidation in making carbon fiber and any of these ovens may be
suitably employed in accordance with this invention. Preferably, however, a series
of ovens (or series of passes through a single oven) are employed according to this
invention with the precursor that is undergoing oxidation optionally stretched to
a longer length than the length it has upon entering the oxidation oven. After exit
from the oxidation oven or ovens, the oxidized (and stabilized) precursor is passed
to one or more furnaces for carbonization in an inert atmosphere. Preferably, at least
two furnaces are employed respectively at temperatures between 400°C and 800°C and
between 1000°C and 1400°C. Still higher modulus carbon fiber is made through using
still another furnace having temperatures above 1800°C, e.g. between 2000°C and 2800°C.
The fiber undergoing carbonization is desirably stretched or at least not allowed
to shrink in the temperature range between 400°C and 800°C and 2000°C and 2800°C.
[0025] After exit from the high temperature furnace the carbonized fiber is surface treated.
A variety of surface treatments are known in the art. Preferred surface treatment
is an electrolytic surface treatment and the degree of surface treatment is ordinarily
a function of the carbonization temperatures used in making the fiber. The preferred
electrolytic surface treatment comprises passing the fiber through a bath containing
an aqueous ammonium bicarbonate or sodium hydroxide solution (e.g. 0.5 - 3% by weight).
The current is applied to the fiber at between about 0.1 and 5 coulumbs/2,54 cm (inch)
of fiber per 12,000 filaments. The resulting surface treated fiber is then preferably
sized with an epoxy compatible sizing agent such as Shell epoxy Epon 834.
[0026] The following examples are intended to illustrate this invention and not to limit
its broader scope as set forth in the appended claims. In these examples, all temperatures
are in degrees Centrigade (°C) and all parts are parts by weight unless otherwise
noted.
Example 1 (reference example)
[0027] Polyacrylonitrile precursors were made using an air gap wet spinning process. The
polymer of the precursor had an intrinsic viscosity between 1.9 and 2.1 deciliters
per gram using a concentrated sodium thiocyanate solution as the solvent. The spinning
solution and coagulants comprised an aqueous solution of sodium thiocyanate. The polymer
was made from a monomer composition that was about 98 mole % acrylonitrile and 2 mole
% methacrylic acid. The precursors were stretched so that their length in tow form
was about six times greater after steam stretching compared to their length after
extrusion from the spinnerets. Table A shows the characteristics of the resulting
precursor which were nominal 0.14 and 0.09 tpf (tex per filament) (1.3 and 0.8 dpf
(denier per filament)).
TABLE A
Precursor Properties |
TPF DPF (NOMINAL) |
0.14 (1.3) |
0.09 (0.8) |
Precursor Properties |
|
|
Tow Tex (g/1000m) |
1.784 |
1.063 |
Tow Denier (g/9000m) |
(16.053) |
(9.570) |
Tow Tenacity cN/dtex (g/d) |
4.3 (4.9) |
4.9 (5.6) |
Tow Modulus cN/dtex (g/d) |
85 (96) |
90.1 (102) |
DHT cN/dtex (g/d) |
0.125 (0.142) |
0.147 (0.166) |
Boil-off Shrinkage (%) |
5.5 |
5.7 |
US Content (%) |
0.60 |
0.88 |
Sodium Content (ppm) |
580 |
568 |
Residual Solvent (%) |
- |
0.0073 |
Moisture Content (%) |
0.92 |
0.60 |
Filament Diameter Cv (%) |
4.1 |
4.4 |
Monster Filaments |
0 |
0 |
[0028] The precursors were then stretched at a temperature of 158°C with a residence time
of about six (6) minutes at that temperature. After stretching, the stretched precursor
was oxidized in stages generally at 234°C and then 249°C. The oxidized fiber was then
passed through a low temperature furnace with a non-oxidizing atmosphere (nitrogen)
at a temperature between 600°C and 800°C (tar removal) and then passed to a high-temperature
furnace having a temperature between 1200°C and 1400°C and a non-oxidizing atmosphere
(nitrogen). During passage through the low and high temperature furnaces the fiber
undergoing carbonization in these furnaces was either allowed to shrink or was stretched
across the length of the furnaces.
[0029] Tables B and C, set forth below, show the stretch of the fiber undergoing carbonization
as it passes through the tar removal (TR) and high temperature (Cl) furnaces along
with the calculated dpf of the filament based on the stretch imparted at 158°C. Under
each level of stretch in these tables the tensile strength and modulus properties
are listed for the fiber having the calculated tpf (dpf) and stretch during passage
through the TR and Cl furnaces. (Table B shows results from using the 0.14 tpf (1.3
dpf) precursor of Table A; Table C shows the result of using the 0.09 tpf (0.8 dpf)
precursor of Table A.) The first value in columns 4 through 9 of Table B and C is
tensile strength of the resultant carbon fiber in Mega Pascal (MPa) times 1000 (psi
times 1000) and the second value is modulus in MPa times 1 000 000 (psi times 1,000,000).
Modulus and tensile strength measurements were made using strand and tow test (Impregnated
Strand) procedures.
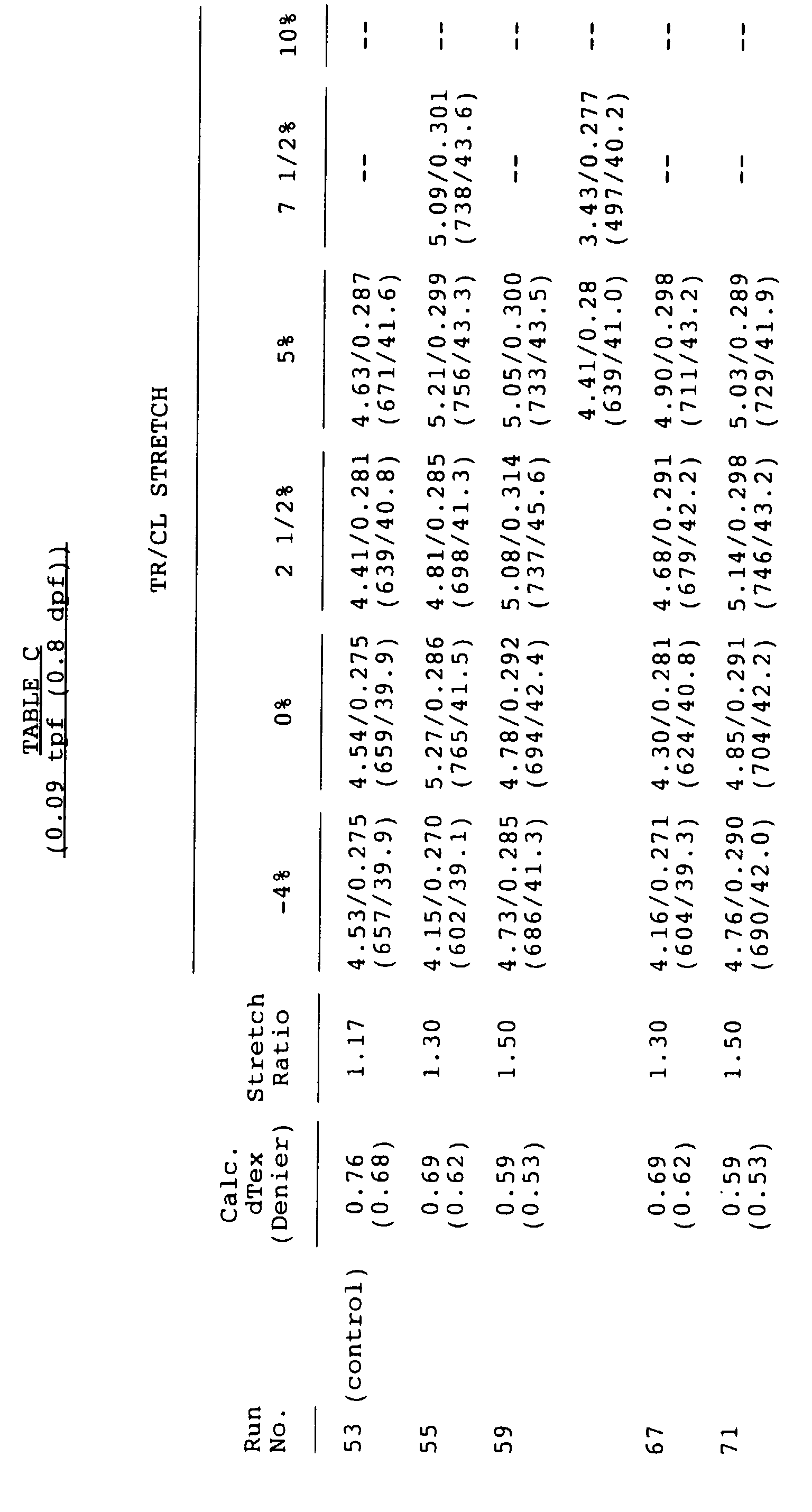
Example 2
[0030] Polyacrylonitrile precursor was made generally according to the conditions previously
described except that it had no steam stretching and its denier was 0.13 tpf (1.2
dpf). The 0.13 tpf (1.2 dpf) polyacrylonitrile precursor fiber was stretched to twice
its original length (i.e. s. r. equals 2) at a temperature of 158°C and wound around
a spool and stored.
[0031] The precursor was then oxidized by passing it through air circulation ovens at temperatures
for the times shown in the following Table D.
TABLE D
Temperatures |
Time (minutes) |
158°C |
2.05 |
240°C |
17.73 |
245°C |
14.43 |
248°C |
17.72 |
250°C |
17.72 |
250°C |
4.43 |
[0032] The oxidized precursor passed from the last oxidation oven through a low temperature
(tar removal) furnace. Then the partially carbonized fiber passed through a first
low temperature furnace held at 1425°C and then a second high temperature furnace
held at 2500°C.
[0033] The stretch in each of the low temperature, first high and second high temperature
furnaces are shown below (values are %) for four distinct runs in Table E below.
TABLE E
Run |
Overall |
TR |
C1 |
C2 |
135-1 |
0.1 |
4.5 |
-5.3 |
0.9 |
135-2 |
2.4 |
6.9 |
-5.1 |
0.9 |
135-3 |
4.9 |
9.3 |
-5.0 |
1.0 |
135-4 |
6.9 |
11.3 |
-4.1 |
0.2 |
[0034] Table F, below, shows the properties of carbon fiber made according to the procedures
of this Example.
TABLE F
Run |
Modulusa |
Tensile Strengthb Density |
135.1 |
0.401 (58.2) |
4.18 (606) |
135.2 |
0.414 (60.1) |
4.24 (615) |
135-3 |
0.424 (61.5) |
4.33 (628) |
135-4 |
0.423 (61.4) |
3.85 (558) |
a 106 MPa (106 psi) |
b 103 MPa (103 psi) |
Example 3
[0035] In this Example, precursor was made under conditions generally described heretofore.
The precursor had a 0.186 tpf (1.67 dpf) (12,000 filaments per tow) and had not been
stretched under steam. The precursor was passed through a device like that shown in
Figure 2 and stretched four (4) times its original length (i.e. S.R. equals 4) after
a residence of 0.8 minutes at about 158°C. In similar studies, a precursor run at
the same temperature but at a residence time of 0.25 minutes broke prior to achieving
a stretch that was equivalent to making it 2.3 times longer than its original length.
When the residence time was increased to 0.33 minutes at 158°C, the tows broke unacceptably
after a stretch that made them 3.3 their original length. However, the precursor had
reduced cosmetics at stretch ratios (S.R.) which equaled 2.0 and 2.3 at these respective
0.25 minutes and 0.33 minutes residences at 158°C.
Example 4
[0036] In this Example the precursor used was made from a polyacrylonitrile polymer using
sodium thiocyanate as solvent and coagulant and an air gap spinning process, as described
heretofore. The fiber was only stretched in water and had a 0.297 tpf (2.67 dpf) and
12,000 filaments per tow. Methacrylic acid was used in making the polyacrylonitrile
polymer.
[0037] The 0.297 tpf (2.67 dpf) precursor was stretched in a prototype device like that
shown in Figure 2, also described hereinbefore. Hot air at 158°C was circulated in
counter-current flow in tube 30 around the tows which were spaced about 1.8 toss per
centimeter.Steam at 0.49 MPa (71 psig) was passed into the jacket of tube 30 and into
the rolls of roll stack 28. The line speed was gradually increased with the stretch
ratio held at 3.9 (i.e. precursor was 3.9 times as long after stretching as compared
to length prior to stretching). Tensions of the precursor were measured in the rolls
stacks 26, 34.
[0038] Results of this Example are shown in Table G, below.
TABLE G
Effect of Increasing Speed on Break Stretch Ratio |
Stretch Ratio |
Line Speed |
No. of Tows |
Tension (gpd) at Pin Position |
|
|
|
1 |
4 |
10 |
3.9X |
25(x30.48cm (ft)/min.) |
10 |
0.347 |
0.335 |
0.333 |
3.9X |
25.8 |
10 |
0.347 |
0.335 |
0.333 |
3.9X |
26.6 |
10 |
0.347 |
0.335 |
0.333 |
3.9X |
27.5 |
10 |
0.347 |
0.335 |
0.333 |
3.9X |
28.3 |
10 |
0.349 |
0.335 |
0.335 |
3.9X |
29.1 |
10 |
0.349 |
0.335 |
0.335 |
3.9X |
30.0 |
10 |
0.349 |
0.335 |
0.335 |
Fiber broke during 9.2 m (30 ft)/min. run. |
Run used 0.297 tpf (2.67 dpf)/12K precursor, hot air at 158°C, steam tube and rolls
at 0.49 MPa (71 psig). 1 gpd = 0.883 cN/dtex
[0039] Table H below shows the results of making a nominal 0.09 tpf (0.8 dpf) precursor
from the aforedescribed 0.297 (2.67) precursor described above using the procedures
of this invention.
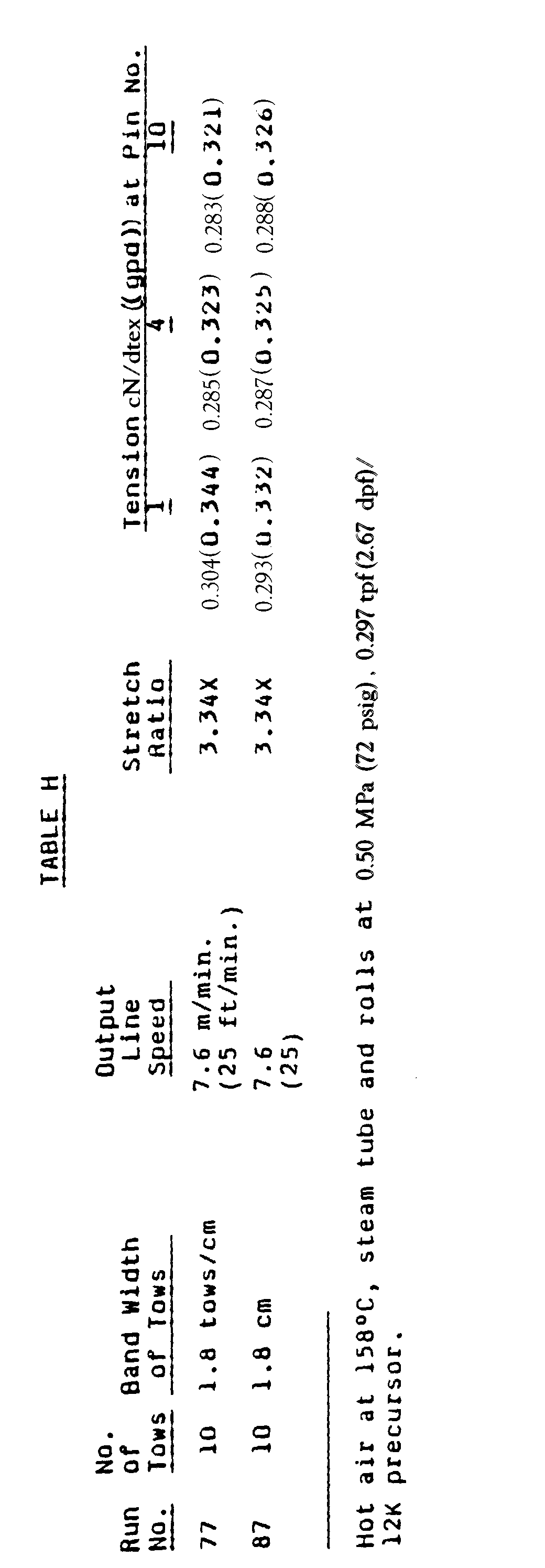
[0040] A standard steam stretched precursor stream (See Table A) having a 0.09 tpf (0.8
dpf) was used as a control in making carbon fiber and compared against carbon fiber
made from a 0.09 tpf (0.8 dpf) (calculated) precursor which was made using the procedures
of this invention. The results are shown in Table I below. As can be seen, nearly
equivalent properties are obtained using the procedures of this invention even though
the amount of stretching in oxidation is less.
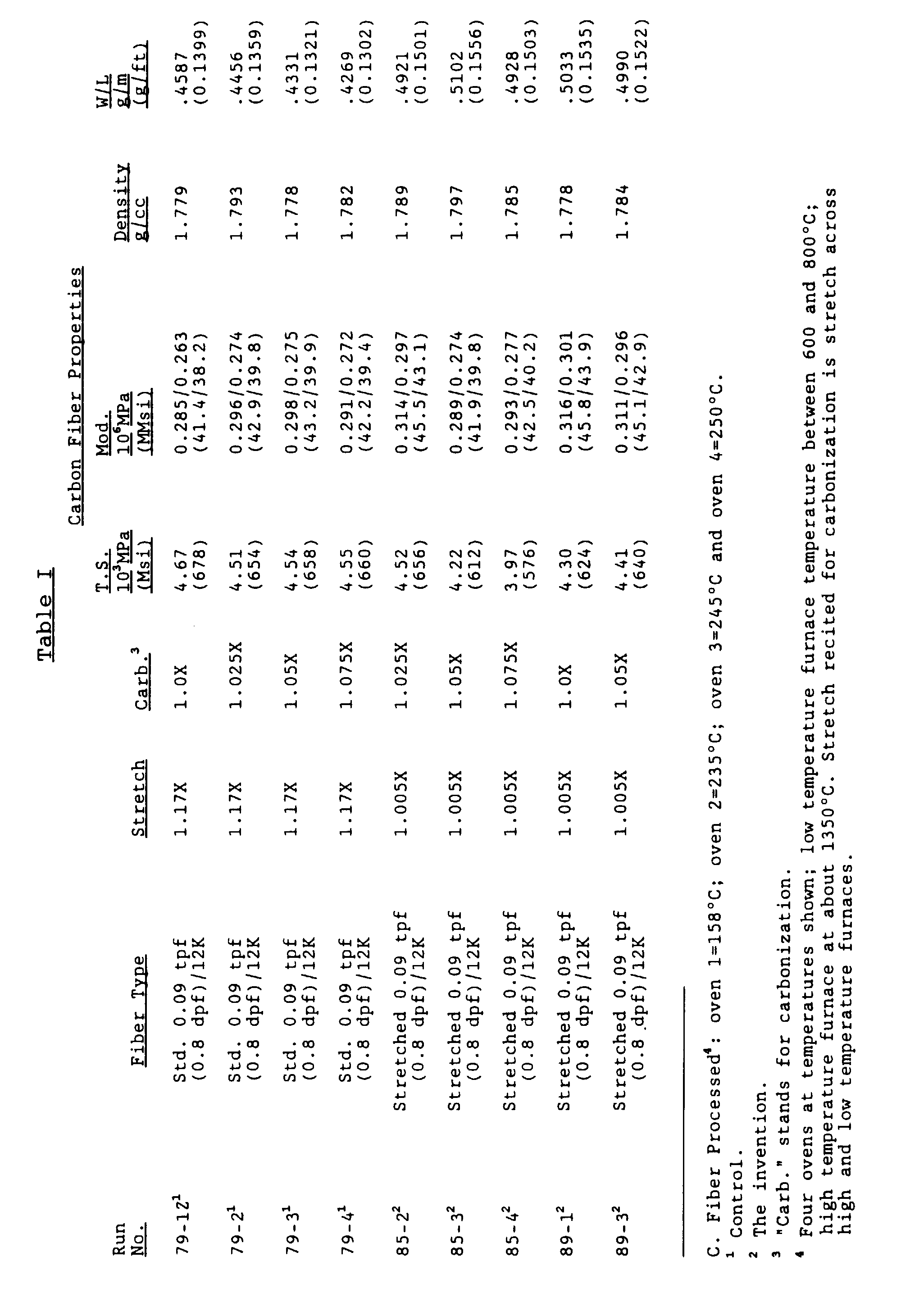
Example 5
[0041] The tension developed at increasing temperatures and 0% stretch (i.e. constant length)
for various precursors was measured. The tension measured versus the temperature to
which each precursor was heated at this 0% stretch is shown in Figure 3 for four polyacrylonitrile
materials. The monomer composition for the precursor of Curve A in Figure 3 included
acrylonitrile, methacrylic acid and methylacrylate. The monomer composition used in
making the precursor of Curve B in Figure 3 included acrylonitrile and methacrylic
acid. The monomer composition used in making the precursor of Curve C included acrylonitrile,
itaconic acid and methylacrylate. Precursors of various compositions were heated to
various temperatures and the break stretch ratio (i.e. stretch ratio (SR) when the
precursor filaments broke) determine for that temperature for each precursor composition.
Curve A, Figure 4, shows a plot of break stretch ratio, or stretch ratio at the time
the filaments of the precursor broke, for a precursor made from ingredients noted
above in connection with Figure 3. Likewise, Curves B and C of Figure 4 show results
for precursors having compositions indicated above with respect to Figure 3.
[0042] Figure 5 shows the results of stretching different denier precursors until breaking
at various temperatures. The monomer composition used in making each of the precursors
in Figure 5 was 98 mole % acrylonitrile and 2 mole % methacrylic acid. Precursors
D, E and F were not stretched in steam and have therefore somewhat less previous stretch
imparted than precursors G and H (which were steam stretched).
[0043] In Figure 3, the conversion 1 gdp = 0.883 cN/dte applies.
1. A process for making carbon fiber in the form of a tow or bundle comprising a multitude
of high strength carbon fiber filaments, said process comprising:
(a) forming a spinning solution comprising a polyacrylonitrile polymer in a solvent
for such polymer;
(b) extruding said polymer through a die to provide a multitude of continuous filaments;
(c) drawing these filaments to a longer length in making a precursor tow; and
(d) oxidizing and then carbonizing said precursor tow in a series of ovens and furnaces
to provide said carbon fiber, which comprises:
(i) selecting precursor tow that is capable of being stretched at a limited temperature
range of 140°C to below the temperature causing oxidation of said precursor tow;
(ii) heating said precursor tow to a temperature within a limited temperature range
above 140°C and below the temperature causing oxidation of said precursor tow; and
(iii) stretching said precursor tow heated to said temperature so that its length
after stretching is at least twice its length prior to stretching.
2. The process in accordance with Claim 1, wherein said heating of step (ii) comprises
heating in a gaseous medium.
3. The process in accordance with Claim 1, wherein said heating of step (ii) comprises
heating through contact with heated rollers.
4. The process in accordance with Claim 1, wherein said limited temperature range is
between 150°C and 160°C.
5. The process in accordance with Claim 1, wherein said polyacrylonitrile is made from
a monomer composition comprising 98 mole % acrylonitrile and 2 mole % methacrylic
acid.
6. The process in accordance with Claim 1, wherein said precursor tow that is stretched
in step (iii) is passed in a heated condition to an oxidation oven.
7. The process in accordance with Claim 1, wherein said drawing of step c consists essentially
of drawing at a temperature below 100°C.
8. The process in accordance with Claim 1, wherein said polyacrylonitrile is heated to
a temperature between 142°C and 180°C so as to permit said precursor tow to be stretched
at least to a length that is four times its original length prior to said stretching
and then stretching said precursor tow at said temperature so it would be four times
longer after said stretching than prior to said stretching at said temperature.
9. A method of making a precursor suitable for a process for manufacturing a high quality
carbon fiber in accordance with Claim 1, said method comprising polymerizing acrylonitrile
and one or more other monomers in a solvent for the resultant polymer, extruding said
polymer through a spinneret comprising a multitude of apertures to provide a precursor
tow comprising a multitude of filaments and stretching said precursor tow wherein
said stretching consists essentially of first and second stretching operations wherein
said first stretching operation is at a temperature below 100°C and said second stretching
operation consists of stretching at a temperature between 142°C and a temperature
wherein said filaments begin to oxidize.
1. Verfahren zur Herstellung von Kohlenstoffasern in Form eines Kabels oder Bündels umfassend
eine Mehrzahl von Kohlenstoffaserfilamenten mit hoher Festigkeit, wobei das Verfahren
umfaßt, daß man
(a) eine Spinnlösung bildet, die ein Polyacrylnitrilpolymer in einem Lösungsmittel
für ein solches Polymer umfaßt;
(b) das Polymer durch eine Düse extrudiert, um eine Vielzahl von kontinuierlichen
Filamenten zu schaffen;
(c) diese Filamente auf eine größere Länge zieht zur Herstellung eines Vorläuferkabels
(d) dieses Vorläuferkabel in einer Reihe von Öfen und Brennöfen oxidiert und dann
carbonisiert, um die Kohlenstoffaser zu liefern, was umfaßt, daß man:
(i) ein Vorläuferkabel auswählt, das in einem begrenzten Temperaturbereich von 140°C
bis unterhalb der Temperatur, die eine Oxidation des Vorläuferkabels verursacht, gestreckt
werden kann;
(ii) das Vorläuferkabel auf eine Temperatur innerhalb eines beschränkten Temperaturbereiches
von mehr als 140°C bis unterhalb der Temperatur die die Oxidation des Vorläuferkabels
verursacht, erwärmt und
(iii) das Vorläuferkabel, das auf diese Temperatur erhitzt wurde, so streckt, daß
seine Länge nach dem Strecken mindestens das 2-fache seiner Länge vor dem Strecken
ist.
2. Verfahren nach Anspruch 1, worin das Erhitzen von Stufe (ii) ein Erhitzen in einem
gasförmigem Medium umfaßt.
3. Verfahren nach Anspruch 1, worin das Erhitzen von Stufe (ii) das Erhitzen durch Kontakt
mit beheizten Walzen umfaßt.
4. Verfahren nach Anspruch 1, worin der begrenzte Temperaturbereich zwischen 150 und
160°C liegt.
5. Verfahren nach Anspruch 1, worin das Polyacrylnitril aus einer Monomerzusammensetzung
hergestellt wird, die 98 mol% Acrylnitril und 2 mol% Methacrylsäure umfaßt.
6. Verfahren nach Anspruch 1, worin das Vorläuferkabel, das in Stufe (iii) gestreckt
wird, in erhitztem Zustand in einen Oxidationsofen geleitet wird.
7. Verfahren nach Anspruch 1, worin das Ziehen in Stufe c im wesentlichen daraus besteht,
bei einer Temperatur unter 100°C zu ziehen.
8. Verfahren nach Anspruch 1, worin das Polyacrylnitril auf eine Temperatur zwischen
142°C und 180°C erhitzt wird, damit das Vorläuferkabel mindestens auf eine Länge gestreckt
werden kann, die das 4-fache ihrer ursprünglichen Länge vor dem Strecken ist und dann
das Vorläuferkabel bei dieser Temperatur gestreckt wird, sodaß es 4 mal länger nach
dem Strecken ist als vor dem Strecken bei dieser Temperatur.
9. Verfahren zur Herstellung eines Vorläufers, der für ein Verfahren zur Herstellung
einer Kohlenstoffaser hoher Qualität gemäß Anspruch 1 geeignet ist, wobei das Verfahren
umfaßt, daß man Acrylnitril und ein oder mehrere andere Monomere in einem Lösungsmittel
für das entstehende Polymer polymerisiert, das Polymer durch eine Spinndüse, die eine
Vielzahl von Öffnungen umfaßt, extrudiert, um ein Vorläuferkabel mit einer Vielzahl
von Filamenten zu schaffen und das Vorläuferkabel streckt, wobei das Strecken im wesentlichen
aus einem ersten und einem zweiten Streckarbeitsgang besteht, wobei der erste Streckarbeitsgang
bei einer Temperatur unter 100°C erfolgt und der zweite Streckarbeitsgang aus einem
Strekken bei einer Temperatur zwischen 142°C und einer Temperatur, bei der die Filamente
zu oxidieren beginnen, besteht.
1. Procédé de fabrication de fibres de carbone se présentant sous la forme d'une mèche
ou d'un faisceau, comportant un très grand nombre de filaments de fibres de carbone
à haute résistance, ledit procédé comportant les étapes consistant à:
(a) former une solution de filage comportant un polymère de polyacrylonitrile dans
un solvant de ce polymère,
(b) extruder ledit polymère à travers une filière pour fournir un très grand nombre
de filaments continus,
(c) étirer ces filaments à une longueur plus élevée en fabriquant une mèche de précurseur,
et
(d) oxyder et ensuite carboniser ladite mèche de précurseur dans une série de fours,
pour fournir lesdites fibres de carbone, lequel procédé comporte les étapes consistant
à
(i) sélectionner une mèche de précurseur apte à être étirée dans une plage de températures
limitée de 140° C à une température inférieure à celle qui provoque l'oxydation de
ladite mèche de précurseur;
(ii) chauffer ladite mèche de précurseur à une température située dans une plage de
températures limitée supérieure à 140° C et inférieure à la température qui provoque
l'oxydation de ladite mèche de précurseur; et
(iii) étirer ladite mèche de précurseur chauffée à ladite température de telle sorte
qu'après étirage, sa longueur soit au moins le double de sa longueur avant l'étirage.
2. Procédé selon la revendication 1, dans lequel ledit chauffage de l'étape (ii) comporte
un chauffage dans un fluide gazeux.
3. Procédé selon la revendication 1, dans lequel ledit chauffage de l'étape (ii) comporte
un chauffage par contact avec des bobines chauffées.
4. Procédé selon la revendication 1, dans lequel ladite classe de températures limitée
est comprise entre 150° C et 160° C.
5. Procédé selon la revendication 1, dans lequel ledit polyacrylonitrile est préparé
à partir d'une composition de monomères comportant 98% en moles d'acrylonitrile et
2% en moles d'acide méthacrylique.
6. Procédé selon la revendication 1, dans lequel ladite mèche de précurseur qui est étirée
au cours de l'étape (iii) est passée à chaud dans un four d'oxydation.
7. Procédé selon la revendication 1, dans lequel ledit étirage de l'étape c consiste
essentiellement en un étirage à une température inférieure à 100° C.
8. Procédé selon la revendication 1, dans lequel ledit polyacrylonitrile est chauffé
à une température comprise entre 142° C et 180° C de manière à permettre l'étirage
de la mèche de précurseur à une longueur qui vaut au moins quatre fois sa longueur
initiale avant ledit étirage, et on étire ensuite ladite mèche de précurseur à ladite
température de telle sorte qu'après ledit étirage, elle soit quatre fois plus longue
qu'avant ledit étirage à ladite température.
9. Procédé de préparation d'un précurseur convenant pour une opération de fabrication
d'une fibre de carbone de haute qualité selon la revendication 1, ledit procédé comportant
les étapes consistant à polymériser de l'acrylonitrile et d'un ou plusieurs autres
monomères dans un solvant du polymère à obtenir, à extruder ledit polymère à travers
une filière comportant un grand nombre d'ouvertures pour obtenir une mèche de précurseur
comportant un grand nombre de filaments, et à étirer ladite mèche de précurseur, ledit
étirage étant essentiellement constitué d'une première et d'une deuxième opération
d'étirage, ladite première opération d'étirage s'effectuant à une température inférieure
à 100° C et ladite deuxième opération étirage consistant en un étirage à une température
qui est comprise entre 142° C et une température à laquelle lesdits filaments commencent
à s'oxyder.