FIELD
[0001] The present invention relates to a lubricating oil composition, especially suitable
for use in an automobile transmission. More specifically, the present invention relates
to a lubricating oil composition for a non-stage transmission.
BACKGROUND
[0002] Lubricating oil compositions are widely used in the automotive field for internal
combustion engines, automatic transmission, gear oil, etc. The demand for low-viscosity
lubricating oil compositions has recently increased, in order to achieve fuel efficiency.
In addition, as a non-stage transmission (CTV) has been replacing stepped automatic
transmission and becoming widely used, metal belt CVT, in which a metal belt and a
pulley are used for power transmission, has become generally used.
[0003] One method of improving the fuel economy of non-stage transmission automobiles is
expanding the operating conditions of the lock-up clutch, and it requires extension
of the lock-up clutch shudder prevention lifespan. Nevertheless, if the quantity of
the friction conditioner is increased, in order to extend the shudder prevention lifespan,
the intermetallic friction coefficient between the metal belt and the pulley decreases,
the belt grip performance decreases, and the torque transmission ability decreases.
Considering such a trade-off between the shudder prevention and the intermetallic
friction coefficient, compatibility of both sufficient torque and shudder prevention
performance at a high level has been sought after. When the viscosity of a lubricating
oil composition for transmission is lowered, satisfactory intermetallic friction coefficient
cannot be achieved, nor can sufficiently large torque be secured.
[0004] Examples of conventional lubricating oil compositions for a non-stage transmission
are described in Patent Literatures 1 to 5. Patent Literature 1 describes a lubricating
oil composition which comprises a specific boron-free succinimide compound and a phosphorus
compound, and does not comprise a zinc dialkyl dithiophosphate, which significantly
increases the friction coefficient between the metal belt or chain and the pulley,
is capable of maintaining a high friction coefficient over a long period of time,
and does not cause clogging of the clutch plates. Patent Literature 2 describes a
lubricant composition comprising a sulfonate-based detergent, a salicylate-based detergent
and a boron-containing succinimide-based additive at specific quantities and specific
quantity ratios, which maintains satisfactory torque transmission capacity and transmission
properties and excels in its shudder prevention performance. Patent Literature 3 describes
a lubricating oil composition comprising specific quantities of a boronated alkylsuccinimide
and/or boronated alkenylsuccinimide having a specific weight-average molecular weight
and a metallic detergent having a linear alkyl group, which has a high intermetallic
friction coefficient and excellent transmission properties and shudder prevention
performance. Patent Literature 4 describes a lubricating oil composition comprising
specific quantities of at least one selected from a specific sulfolane derivative,
calcium sulfonate and calcium phenate, and a specific viscosity index improver, which
has both a high intermetallic friction coefficient and combines fuel efficiency, due
to low viscosity, and component durability. Patent Literature 5 describes that by
combining at least 4 additives, namely calcium salicylate, phosphorus anti-wear agent,
friction conditioner and dispersion-type viscosity index improving agent, as essential
components, both a high intermetallic friction coefficient and shudder prevention
can be achieved.
[CITATION LIST]
[PATENT LITERATURE]
SUMMARY
[TECHNICAL PROBLEM]
[0006] In light of the above circumstances, the first purpose of the present invention is
to provide a lubricating oil composition, whose intermetallic friction coefficient
does not decrease and which has extended shudder prevention lifespan, even if the
viscosity thereof is lowered.
[SOLUTION TO PROBLEM]
[0007] As a result of painstaking research, the inventors arrived at the present invention
after discovering that the shudder prevention lifespan can be extended without decreasing
the intermetallic friction coefficient, even at low viscosity, if two types of succinimide
compounds having specific weight-average molecular weights are combined as an ashless
dispersant and used together with a specific friction modifier.
[0008] That is, the present invention is a lubricating oil composition comprising
(A) a lubricant base oil,
(C) (C-1) a succinimide compound or boronated succinimide compound having a weight-average
molecular weight of 4,000 to 7,000, and (C-2) a succinimide compound or boronated
succinimide compound having a weight-average molecular weight of more than 7,000 and
not more than 10,000, and
(D) (D-1) an amide friction modifier.
[0009] Moreover, in order to improve fuel economy, maintaining the viscosity at an elevated
temperature (for example, 100°C) while decreasing the viscosity at a low temperature
(for example, 40°C), which has an effect on the fuel economy, that is, a high viscosity
index is required, but in conventional lubricating oil compositions for a non-stage
transmission, the polymer chains of the base oil and the viscosity index improver
are broken by the mechanical shear, and as a result the high temperature viscosity
unfavorably decreases with operation.
[0010] The inventors discovered that by further specifying the compositions of the lubricant
base oil (A) and the viscosity index improver in the above lubricating oil composition,
the shear stability can be improved, in addition to an effect of extending the shudder
prevention lifespan without decreasing the intermetallic friction coefficient.
[0011] The lubricating oil composition of the present invention preferably further comprises,
as a part or all of component (A), 5 to 30 percent by weight, based on a total weight
of the lubricating oil composition, of a poly-α-olefin or α-olefin copolymer having
a kinematic viscosity at 100°C of 6 to 80 mm
2/s, and further comprising (B) a polymethacrylate having a weight-average molecular
weight of 15,000 to 40,000.
[0012] In addition, preferable embodiments of the lubricating oil composition of the present
invention have at least one following featues (1) to (11).
- (1) It further comprises (D-2) a friction modifiercomposed of a reaction product of
boric acid or boron oxide with an epoxide.
- (2) A part or all of component (C-1) and component (C-2) is a boronated succinimide
compound.
- (3) Each of component (C-1) and/or component (C-2) contains 0.1 to 3 percent by weight
of boron based on a weight of component (C-1) or component (C-2).
- (4) A weight ratio of component (C-1) to component (C-2), i.e., (C-2)/(C-1), is 1
to 10.
- (5) The lubricating oil composition has a kinematic viscosity at 100°C of 3 to 10
mm2/s.
- (6) The lubricating oil composition has a viscosity index of not less than 150.
- (7) Component (D-1) is at least one selected from amide compounds derived from fatty
acids having an alkyl or alkenyl group having 6 to 30 carbon atoms.
- (8) Component (D-2) is at least one selected from reaction products of an epoxide
represented by the following formula:

wherein R1, R2, R3, and R4 each independently represent a hydrogen atom or a hydrocarbon
group having 1 to 30 carbon atoms, and at least one of R1, R2, R3, and R4 is a hydrocarbon
group,
with boric acid or boron oxide, or ring-opened products thereof.
- (9) The lubricating oil composition further comprises (E) a metallic detergent.
- (10) The lubricating oil composition further comprises (F) an ether sulfolane compound.
- (11) The lubricating oil composition is for a non-stage transmission.
[0013] In particular, the lubricating oil composition preferably comprises, as a part or
all of component (A), 5 to 30 percent by weight, based on a total weight of the lubricating
oil composition, of a poly-α-olefin or α-olefin copolymer having a kinematic viscosity
at 100°C of 6 to 80 mm
2/s, and (E) an ether sulfolane compound. Compared with mineral oil, synthetic base
oil has low affinity to the oil seal rubber called packing and gasket, and the affinity
is lower as the base oil has a higher molecular weight, i.e., higher viscosity. When
the affinity is low, the swelling property of the seal rubber decreases, and conversely
it is easy to shrink. This causes the sealing to decrease and oil spill to occur.
The lubricating oil composition of the present invention ensures that the seal rubber
can sufficiently swell.
[0014] Moreover, the lubricating oil composition is characterized in that it has superior
initial anti-shudder properties, if it further comprises (D-2) a friction modifiercomposed
of a reaction product of boric acid or boron oxide with an epoxide.
[ADVANTAGEOUS EFFECTS OF INVENTION]
[0015] The lubricating oil composition of the present invention is capable of extending
the shudder prevention lifespan without decreasing the intermetallic friction coefficient.
This effect can be achieved even when the kinematic viscosity at 100°C of the lubricating
oil composition is lowered to about 5.0. In addition to the above effect, the present
invention can provide a lubricating oil composition having increased shear stability.
Furthermore, it ensures that the seal rubber can sufficiently swell. Moreover, it
can improve the initial anti-shudder properties. The lubricating oil composition of
the present invention can be suitably used especially as a lubricating oil composition
for a non-stage transmission.
DESCRIPTION OF EMBODIMENTS
[0016] Each component will now be described.
(A) Lubricant base oil
[0017] Conventional and commonly-known lubricant base oils can be used as the lubricant
base oil in the present invention. The lubricant base oil includes a mineral oil,
a synthetic oil or a mixture thereof. In particular, the lubricating oil composition
preferably comprises, as a part or all of the lubricant base oil, 5 to 30 percent
by weight, based on a total weight of the lubricating oil composition, of a poly-α-olefin
or α-olefin copolymer having a kinematic viscosity at 100°C of 6 to 80 mm
2/s. The lower limit of the content of the poly-α-olefin or α-olefin copolymer is more
preferably 6 percent by weight and still more preferably 8 percent by weight, and
the upper limit is more preferably 25 percent by weight, and still more preferably
20 percent by weight. If the content of the above base oil is below the above lower
limit, there is a possibility that a satisfactory viscosity index, i.e., a combination
of fuel efficiency and protection of the machine elements, cannot be achieved, and
if it exceeds the above upper limit, there is a possibility that the shear stability
may decrease and the rubber adaptability may deteriorate, i.e., the rubber shrinks.
[0018] The poly-α-olefin or α-olefin copolymer has a kinematic viscosity at 100°C of 6
to 80 mm
2/s, preferably 8 to 80 mm
2/s, more preferably 8 to 60 mm
2/s, and still more preferably 9 to 40 mm
2/s. If the kinematic viscosity at 100°C is below the above lower limit, a satisfactory
viscosity index, i.e., a combination of fuel efficiency and protection of the machine
elements, cannot be achieved, and if the kinematic viscosity at 100°C exceeds the
above upper limit, the shear stability decreases and the rubber adaptability deteriorates,
i.e., the rubber shrinks.
[0019] The poly-α-olefin or α-olefin copolymer is a (co)polymer or a (co)oligomer of α-olefin.
Conventional and commonly-known poly-α-olefin or α-olefin copolymers may be used as
the lubricant base oil, as long as they have the above kinematic viscosity. The α-olefin
is selected, for example, from a C2-14, preferably C4-12, linear or branched olefinic
hydrocarbon. Examples of the poly-α-olefin or α-olefin copolymer include 1-octene
oligomer, 1-decene oligomer, ethylene-propylene oligomer, isobutene oligomer, and
hydrogenated products thereof. Moreover, the poly-α-olefin or α-olefin copolymer may
be manufactured using a metallocene catalyst. The weight-average molecular weight
of the (co)polymer or (co)oligomer should only be such that the kinematic viscosity
at 100°C is within the above range. Its weight-average molecular weight may be, for
example, 1,000 to 10,000, preferably 1,100 to 7,000. One type of poly-α-olefin or
α-olefin copolymer may be used, or two or more types thereof may be used together.
[0020] The lubricating oil composition of the present invention may comprise other lubricant
base oils in combination with the above poly-α-olefin or α-olefin copolymer. The other
lubricant base oils include, but are not limited to, conventional commonly-used mineral
oil-based base oils and synthetic base oils other than the above poly-α-olefin or
α-olefin copolymer.
[0021] Examples of the mineral oil-based base oil include paraffinic or naphthenic lubricant
base oils, obtained by distilling a crude oil at a normal atmospheric pressure and
under vacuum to prepare a lubricating oil fraction and subjecting the lubricating
oil fraction to a suitable combination of purification treatments such as solvent
deasphalting, solvent extraction, hydrogenolysis, solvent dewaxing, catalytic dewaxing,
hydrorefining, sulfuric acid treatment and clay treatment, and lubricant base oils
obtained by isomerizing a wax obtained by solvent dewaxing and dewaxing the isomerized
product. The kinematic viscosity of the mineral oil-based base oil is preferably,
but is not limited to, 1 to 5 mm
2/s in order to obtained a low-viscosity lubricating oil composition.
[0022] Examples of the synthetic base oil include isoparaffins, alkylbenzenes, alkylnaphthalenes,
monoesters, diesters, polyol esters, polyoxyalkylenglycols, dialkyldiphenyl ethers,
polyphenyl ethers, and GTL base oils. No particular restrictions are placed on the
kinematic viscosity of the synthetic base oil. Furthermore, a poly-α-olefin or α-olefin
copolymer having a kinematic viscosity at 100°C of less than 6 mm
2/s or more than 80 mm
2/s can also be used. In order to obtained a low-viscosity lubricating oil composition,
the kinematic viscosity of the synthetic base oil is preferably 1 to 6 mm
2/s.
[0023] The other base oils used in combination with the poly-α-olefin or α-olefin copolymer
may be used alone or two or more types thereof may be used together. When two or more
types thereof are used, two or more types of mineral oil-based base oils may be used,
two or more types of synthetic base oils may be used, or a combination of a mineral
oil-based base oil and a synthetic base oil may be used. Among them, the use of a
single mineral oil-based base oil, the use of two or more types of mineral oil-based
base oils, the use of a single synthetic base oil having a kinematic viscosity at
100°C of not less than 1 mm
2/s and less than 6 mm
2/s, and the use of two or more types of synthetic base oils having a kinematic viscosity
at 100°C of not less than 1 mm
2/s and less than 6 mm
2/s are preferable.
[0024] Moreover, in order to obtain a low-viscosity lubricating oil composition, the whole
lubricant base oil preferably has a kinematic viscosity at 100°C of 2 to 7 mm
2/s, more preferably 2.3 to 6 mm
2/s, and more preferably 2.5 to 5.6 mm
2/s.
(B) Viscosity index improver
[0025] The lubricating oil composition of the present invention may also comprise conventional
commonly-known viscosity index improver. The lubricating oil composition preferably
comprises a polymethacrylate having a weight-average molecular weight of 15,000 to
40,000 as the viscosity index improver. The lower limit of the weight-average molecular
weight is preferably 17,000 and more preferably 18,000. The upper limit of the weight-average
molecular weight is preferably 38,000 and more preferably 36,000. If the weight-average
molecular weight is less than the above lower limit, the effect of the viscosity index
improver is insufficient, and if the weight-average molecular weight is more than
the above upper limit, the effect of viscosity index improvement is achieved, but
the shear stability deteriorates. The content of the polymethacrylate is preferably,
but is not limited to, 0.1 to 20 percent by weight, more preferably 0.1 to 15 percent
by weight, and still more preferably 2 to 10 percent by weight, based on the lubricating
oil composition.
[0026] One type of the polymethacrylate may be used alone or two or more types thereof may
be used in combination.
[0027] The lubricating oil composition of the present invention may also comprise other
viscosity index improvers in combination with the polymethacrylate. Examples of other
viscosity index improvers include a polymethacrylate having a weight-average molecular
weight of less than 15,000, a polymethacrylate having a weight-average molecular weight
of more than 40,000, a polyisobutylene and hydrogenated products thereof, a hydrogenated
styrene-diene copolymer, a styrene-maleic anhydride ester copolymer, and a polyalkylstyrene.
If other viscosity index improvers are contained, the content thereof is preferably
0.1 to 15 percent by weight based on the lubricating oil composition.
(C) Succinimide compound
[0028] The lubricating oil composition of the present invention is characterized in that
it comprises, as an ashless dispersant, two types of specific succinimide compounds.
In other words, the lubricating oil composition is characterized in that it comprises
(C-1) a succinimide compound having a weight-average molecular weight of 4,000 to
7,000, preferably 5,000 to 7,000, and (C-2) a succinimide compound having a weight-average
molecular weight of more than 7,000 and not more than 10,000, preferably 7,100 to
9,600. Hereinafter, above component (C-1) is also referred to as "the 1st succinimide
compound" and above component (C-2) is also referred to as "the 2nd succinimide compound."
[0029] A part or all of component (C-1) and component (C-2) may be, but not limited to,
a boronated succinimide compound.
[0030] The content of component (C) in the composition is preferably 0.5 to 3.0 percent
by weight, more preferably 0.6 to 2.5 percent by weight, and still more preferably
0.9 to 2.0 percent by weight, based on the total weight of the composition. If its
content is less than the above lower limit, the shudder prevention may not be secured.
If it is more than the above upper limit, the viscosity may increase at a low temperature.
[0031] The weight ratio of component (C-1) to component (C-2), i.e., (C-2)/(C-1), is preferably,
but not limited to, 1 to 10, more preferably 1.5 to 8, and still more preferably 2
to 6. When the weight ratio is within the above range, both a favorable friction coefficient
and favorable anti-shudder properties can be achieved. If the quantity of (C-1) is
insufficient, the shudder prevention becomes insufficient at a low temperature, e.g.,
at 40°C, which is evident early in endurance testing. If the quantity of (C-2) is
insufficient, the shudder prevention becomes insufficient at a high temperature, e.g.,
at 120°C, which is evident early in endurance testing.
[0032] The 1st and 2nd succinimide compounds the present invention may be a succinimide
compound known publicly as an ashless dispersant.
[0033] More specifically, the succinimide compound is a compound obtained by adding succinic
anhydride to polyamine. There are monotype succinimide compounds and bis-type succinimide
compounds, and either can be used. The monotype succinimide compound can be represented
by formula (1) below. The bis-type succinimide compound can be represented by formula
(2) below.
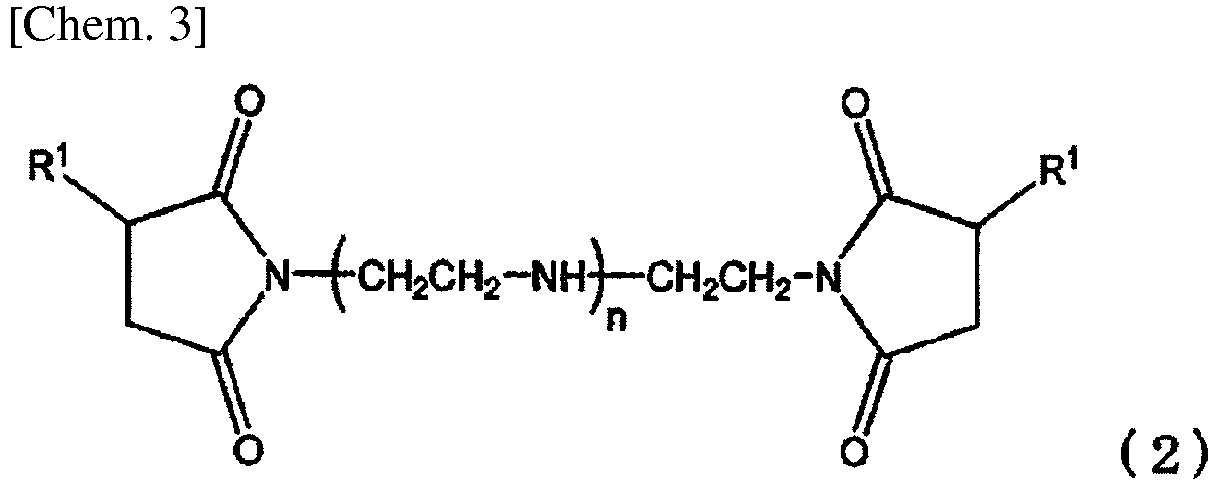
wherein R
1 is each independently an alkyl or alkenyl group having 40 to 400 carbon atoms, m
is an integer of 1 to 20, and n is an integer of 0 to 20. Bistype succinimide compounds
are especially preferable. As boronated succinimide compounds, a monotype succinimide
compound and a bis-type succinimide compound may be used in combination, or two or
more monotype succinimide compounds may be used in combination, or two or more bis-type
succinimide compounds may be used in combination. The nitrogen content in the succinimide
compound is preferably, but not limited to, 0.3 to 10 percent by weight, more preferably
0.5 to 5 percent by weight, and still more preferably 0.8 to 2.5 percent by weight,
based on the weight of the compound.
[0034] The optional boronated succinimide compound is more specifically a compound obtained
by reacting a succinimide compound represented by the above formula with a boron compound.
Examples of a boron compound include boric acid, boric anhydride, an ester of boric
acid, boron oxide, boron halide, etc. Moreover, an example of a boronated succinimide
compound is a product obtained by modifying (boronating) a succinimide compound containing
in its molecule at least one alkyl or alkenyl group with boric acid, borate, or the
like. Examples of the alkyl or alkenyl group include monovalent groups derived from
an oligomer of an olefin such as propylene, 1-butene, and isobutylene, a co-oligomer
of ethylene and propylene, or the like.
[0035] The 1st succinimide compound (C1) has a weight-average molecular weight of 4,000
to 7,000. The weight-average molecular weight is preferably 5,000 to 7,000 and more
preferably 5,200 to 6,800. If the molecular weight of the 1st succinimide compound
is less than the above lower limit, the anti-shudder properties deteriorate.
[0036] In the present invention, the weight-average molecular weight of the 1st succinimide
compound is measured using an RI (differential refractometry) detector, with a solvent
of THF (tetrahydrofuran), a packed column of styrene-divinyl benzene copolymer, a
set temperature of 40°C, and a set flow rate of 1.0 mL/min, and is expressed in polystyrene-converted
value.
[0037] When a boronated succinimide compound is used as the 1st succinimide compound, the
boron content is preferably, but not limited to, 0.1 to 3 percent by weight, more
preferably 0.2 to 2.5 percent by weight, still more preferably 0.2 to 2 percent by
weight, and most preferably 0.2 to 1.5 percent by weight, based on the weight of the
compound.
[0038] The content of the 1st succinimide compound in the lubricating oil composition is
preferably, but not limited to, 0.05 to 2.00 percent by weight, more preferably 0.08
to 1.80 percent by weight, and still more preferably 0.10 to 1.50 percent by weight,
based on the total weight of the lubricating oil composition. If the content is less
than the above lower limit, there is a possibility that sufficient washability may
not be secured, and if it is more than the above upper limit, there is a possibility
that sludge may be generated.
[0039] The 1st succinimide compound can be at least one selected from a succinimide compound
which is not boronated and a boronated succinimide compound. Therefore, it may be
selected from a single succinimide compound which is not boronated, and two or more
succinimide compounds which are not boronated, a single boronated succinimide compound,
two or more boronated succinimide compounds, and a combination of at least one succinimide
compound which is not boronated and at least one boronated succinimide compound.
[0040] The 2nd succinimide compound (C-2) has a weight-average molecular weight of more
than 7,000 and not more than 10,000. The weight-average molecular weight is preferably
7,100 to 9,600, and more preferably 7,500 to 9,200. If the molecular weight of the
2nd succinimide compound is more than the above upper limit, the low-temperature viscosity
of the compound becomes inconveniently high.
[0041] In the present invention, the weight-average molecular weight of the 2nd succinimide
compound is measured using an RI (differential refractometry) detector, with a solvent
of THF (tetrahydrofuran), a packed column of styrenedivinyl benzene copolymer, and
a set temperature of 40°C set flow rate of 1.0 mL/min, and is expressed in polystyrene-converted
value.
[0042] When a boronated succinimide compound is used as the 2nd succinimide compound, the
boron content is preferably, but not limited to, 0.1 to 3 percent by weight, more
preferably 0.2 to 2.5 percent by weight, still more preferably 0.2 to 2 percent by
weight, and most preferably 0.2 to 1.5 percent by weight, based on the weight of the
compound. The nitrogen content in the succinimide compound is preferably, but not
limited to, 0.2 to 5.0 percent by weight, more preferably 0.3 to 2.5 percent by weight,
and still more preferably 0.5 to 2.0 percent by weight.
[0043] The content of the 2nd succinimide compound in the lubricating oil composition is
preferably, but not limited to, 0.2 to 3.0 percent by weight, more preferably 0.4
to 2.5 percent by weight, and still more preferably 0.6 to 2.0 percent by weight,
based on the total weight of the lubricating oil composition. If the content is less
than the above lower limit, there is a possibility that sufficient washability may
not be secured, and if it is more than the above upper limit, the low-temperature
viscosity of the composition becomes inconveniently high.
[0044] The 2nd succinimide compound can be at least one selected from a succinimide compound
which is not boronated and a boronated succinimide compound. Therefore, it may be
selected from a single succinimide compound which is not boronated, two or more succinimide
compounds which are not boronated, a single boronated succinimide compound, two or
more boronated succinimide compounds, and a combination of at least one succinimide
compound which is not boronated and at least one boronated succinimide compound.
[0045] The lubricating oil composition of the present invention may further comprise other
ashless dispersants in combination with above component (C-1) and above component
(C-2). A typical example of the other ashless dispersant includes a succinamide compound.
[0046] The lubricating oil composition of the present invention further comprises (D)(D-1)
an amide friction modifier as an indispensable component, and optionally (D-2) a friction
modifiercomposed of a reaction product of boric acid or boron oxide with an epoxide
in addition to above components (A) to (C).
(D) Friction modifiers
[0047] As a friction modifier, an amide friction modifier (D-1) is an essential component,
and a friction modifiercomposed of a reaction product of boric acid or boron oxide
with an epoxide (D-2) is optionally used.
[0048] Preferable amide friction modifier (D-1) include, but is not limited to, fatty acid
amide compounds. In particular, amides of a linear fatty acid and an aliphatic monoamine
or aliphatic polyamine can be used. Among them, fatty acid amide compounds having
an C6-30 alkyl or alkenyl group having 6 to 30 carbon atoms can be preferably used.
Concrete preferable examples thereof include lauramide, lauric acid diethanolamide,
lauric acid monopropanol amide, myristamide, myristic acid diethanolamide, myristic
acid monopropanol amide, palmitamide, palmitic acid diethanolamide, palmitic acid
monopropanol amide, stearamide, isostearamide, stearic acid dimethanolamide, isostearic
acid dimethanolamide, stearic acid diethanolamide, isostearic acid diethanolamide,
stearic acid monopropanol amide, isostearic acid monopropanol amide, isostearic acid
tris(hydroxymethol)methylene amide, oleamide, oleic acid dimthanolamide, oleic acid
diethanolamide, oleic acid monopropanol amide, coconut oil fatty acid amide, coconut
oil fatty acid diethanolamide, coconut oil fatty acid monopropanol amide, C
12-13 synthetic mixed fatty amides, C
12-13 synthetic mixed fatty acid diethanolamides, C
12-13 synthetic mixed fatty acid monopropanol amides, and mixtures thereof.
[0049] This amide friction modifier (D-1) is an essential component.
[0050] While the lubricating oil composition of the present invention must comprise an amide
friction modifier (D-1) as an essential component, it may also comprise other friction
modifiers. It may comprise, for example, other ester friction modifiers, amine friction
modifiers, alcohol friction modifiers, molybdate friction modifiers and other optional
friction modifiers.
[0051] Of these, a friction modifier composed of a reaction product of boric acid or boron
oxide with an epoxide (D-2) is preferably used, since the initial anti-shudder properties
is improved by using it.
(D-2) a friction modifier composed of a reaction product of boric acid or boron oxide
with an epoxide.
[0052] Friction modifiers composed of said reaction products are commonly known, and are
disclosed, for example, in
JP 2000-87068 A. Examples of boric acid include various types of boric acid (including metaboric
acid, HBO
2, orthoboric acid, H
3BO
3 and tetraboric acid H
2B
4O
7), and alkyl borates represented by the formula (RO)xB(OH)y where x is 1 to 3, y is
0 to 2, the total of x and y is 3 and R is an alkyl group having 1 to 6 carbon atoms.
Examples of the epoxide include epoxides themselves, and equivalents thereof from
the reaction viewpoint, for example, diols and halohydrins. As described in detail
in United States Patent No.
4,584,115, it is generally prepared by reacting an epoxide (preferably hydrocarbyl epoxide)
with boric acid or boron trioxide. An epoxide can be represented by the following
formula:
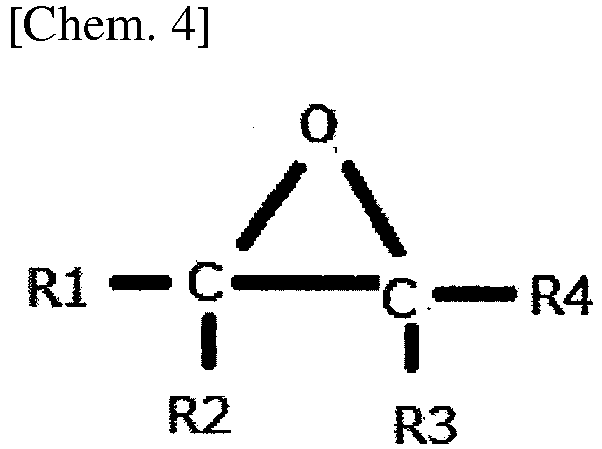
wherein R1, R2, R3 and R4 each independently represent a hydrogen atom or a hydrocarbon
group having 1 to 30 carbon atoms, and at least one of R1, R2, R3 and R4 is a hydrocarbon
group. Any two of R1, R2, R3 and R4 may form a cyclic group, which may be alicyclic
or heterocyclic, together with the same bonding atom.
[0053] It is preferable that one of R1, R2, R3 and R4 is a hydrocarbon group having 6 to
30 carbon atoms, and the rest are hydrogen atoms, to which they are not limited. The
hydrocarbon group having 1 to 30 carbon atoms include, but is not limited to, an alkyl
group, alkenyl group, alkynyl group, and aryl group, as well as saturated or unsaturated
fatty acid residues.
[0054] Examples of saturated fatty acid residues include a caproic acid residue, caprylic
acid residue, capric acid residue, lauric acid residue, myristic acid residue, palmitic
acid residue, stearic acid residue and isostearic acid residue.
[0055] Examples of unsaturated fatty acid residues include linoleic acid residue, α-linolenic
acid residue, γ-linolenic acid residue, arachidonic acid residue, docosapentaenoic
acid residue, palmitoleic acid residue, vaccenoic acid residue, paullinic acid residue,
oleic acid residue (oleyl group), elaidic acid residue, erucic acid residue and nervonic
acid residue.
[0056] Such epoxides can be commercially available mixtures of C14-16 or C14-18 epoxides,
which are available from ELF-Atochem or UnionCarbide, or prepared from the corresponding
olefins using commonly-known methods. The reaction product can be prepared by mixing
boric acid or boron oxide (hereinafter referred to collectively as "boric acid") and
an epoxide or an equivalent thereof (hereinafter referred to collectively as "epoxide")
and heating them at an appropriate temperature (typically 80°C to 250°C). The molar
ratio of boric acid to an epoxide is generally 4:1 to 1:4, preferably 1:1 to 1:3,
more preferably 1:2. When conducting the reaction, an inert liquid may be used as
the reaction media. Examples of such a liquid include toluene, xylene, chlorobenzene
and dimethyl formamide. Water forms during the reaction and is typically evaporated
during the reaction process. Hydroxide may be used in order to facilitate the reaction.
In the reaction product, the epoxide ring may have been opened. A preparation method
of the reaction product is disclosed also in
JP S57-200496 A.
[0057] The thus-obtained compound may be effectively used as a friction modifier and provides
excellent anti-shudder properties.
[0058] Preferable examples of component (D-2) include, but are not limited to, a borate
chloride of a fatty acid epoxy ester or a ring-opened product thereof. Specific examples
thereof include a borate chloride of glycidyl caprate, borate chloride of glycidyl
caproate, borate chloride of glycidyl myristate, borate chloride of glycidyl palmitate,
borate chloride of glycidyl oleate, borate chloride of ethyleneoxide oleate, borate
chloride of glycidyl stearate, borate chloride of glycidyl isostearate and borate
chloride of glycidyl laurate.
[0059] The added quantity of component (D-1) is preferably, but not limited to, be 0.01
to 5 percent by weight, more preferably 0.02 to 4 percent by weight, and still more
preferably 0.1 to 3 percent by weight, based on the total weight of the lubricating
oil composition.
[0060] Component (D-2) is not essential, but when it is added, the added quantity thereof
is preferably 0.01 to 5 percent by weight, more preferably 0.02 to 4 percent by weight,
and still more preferably 0.1 to 3 percent by weight, based on the total weight of
the lubricating oil composition.
[0061] It is preferable that the lubricating oil composition of the present invention further
comprises (E) a metallic detergent and/or (F) an ether sulfolane compound in addition
to above components (A) to (D).
(E) Metallic detergent
[0062] A metallic detergent includes a detergent containing an alkali metal or alkaline
earth metal. Examples thereof include, but are not limited to, sulfonates containing
an alkali metal or alkaline earth metal, salicylates containing an alkali metal or
alkaline earth metal, and phenates containing an alkali metal or alkaline earth metal.
Examples of an alkali metal or alkaline earth metal include, but are not limited to,
magnesium, barium, sodium and calcium.
[0063] Preferable examples of a sulfonate containing an alkali metal or alkaline earth metal
include, but are not limited to, calcium sulfonate and magnesium sulfonate.
[0064] Preferable examples of a salicylate containing an alkali metal or alkaline earth
metal include, but are not limited to, calcium salicylate and magnesium salicylate.
[0065] Preferable examples of a phenate containing an alkali metal or alkaline earth metal
include, but are not limited to, calcium phenate and magnesium phenate.
[0066] The quantity of the alkali metal or alkaline earth metal in the metallic detergent
is preferably, but not limited to, 0.1 to 20 percent by weight, more preferably 0.5
to 15 percent by weight, and still more preferably 1.0 to 15 percent by weight, based
on the weight of the metallic detergent.
[0067] The metallic detergent has a total base number of preferably, but not limited to,
10 to 500 mgKOH/g, more preferably 50 to 400 mgKOH/g, still more preferably 150 to
400 mgKOH/g, still more preferably 200 to 400 mgKOH/g, still more preferably 300 to
400 mgKOH/g, and most preferably 310 to 400 mgKOH/g. When the total base number is
within the above range, the washability effect is high and sludge generation can be
prevented.
[0068] The metallic detergent may be contained at any ratio in the lubricating oil composition.
The content thereof is, for example, 0 to 5 percent by weight, preferably 0.1 to 2
percent by weight, and still more preferably 0.2 to 1 percent by weight, based on
the total weight of the lubricating oil composition.
[0069] A single metallic detergent may be used alone, or two or more metallic detergents
may be used in combination. When two or more metallic detergents are used in combination,
examples of the combination include, but are not limited to, a combination of two
or more sulfonate compounds, a combination of two or more salicylate compounds, a
combination of two or more phenate compounds, a combination of at least one sulfonate
compound and at least one salicylate compound, a combination of at least one sulfonate
compound and at least one phenate compound, and a combination of at least one salicylate
compound and at least one phenate compound.
(F) Ether sulfolane compound
[0070] By comprising an ether sulfolane compound, the lubricating oil composition of the
present invention can secure moderate seal rubber swelling properties. The ether sulfolane
compound is a compound represented by the following formula:

wherein R is an alkyl group having 1 to 20 carbon atoms, preferably an alkyl group
having 8 to 16 carbon atoms.
[0071] The content of the ether sulfolane compound is preferably 0 to 5 percent by weight,
more preferably 0.1 to 2 percent by weight, and still more preferably 0.2 to 1 percent
by weight, based on the total weight of the lubricating oil composition.
[0072] The lubricating oil composition of the present invention may further comprise additives
other than above components (B) to (F). Examples of the other additive include oiliness
agents, anti-wear agents, extreme pressure agents, rust-preventive agents, friction
modifiers other than the above friction modifiers, antioxidants, corrosion inhibitors,
metal deactivators, pour point depressants, antifoaming agents, coloring agents, and
package additives for automatic transmission fluid. Package additives for lubricating
oil containing at least one of the above additives can be added.
[0073] The extreme pressure agent includes, but is not limited to, a phosphorus-based extreme
pressure agent. The phosphorus-based extreme pressure agent is preferably at least
one selected from acidic phosphate, acidic phosphate phosphite, phosphate, phosphite,
amine salts thereof, phosphoric acid, and phosphorous acid.
[0074] Moreover, an unlimited preferable example of the extreme pressure agent is a combination
of at least one selected from acidic phosphate, acidic phosphate phosphite, phosphate,
phosphite, and amine salts thereof, and at least one selected from phosphoric acid
and phosphorus acid.
[0075] Moreover, an unlimited preferable example of the extreme pressure agent is a combination
of at least one selected from acidic phosphate, acidic phosphate phosphite, phosphate,
phosphite, amine salts thereof, and at least one selected from phosphoric acid and
phosphorus acid.
[0076] In addition, a combination of an acidic phosphate and at least one compound selected
from phosphoric acid and phosphorous acid is also preferable. Preferable examples
of an acidic phosphate include acidic butyl phosphate, acidic hexyl phosphate, acidic
octyl phosphate, and acidic dodecyl phosphate.
[0077] The quantity of the phosphorus-based extreme pressure agent is preferably, but not
limited to, 0.01 to 2.5 percent by weight, more preferably 0.02 to 1.5 percent by
weight, and still more preferably 0.02 to 1.0 percent by weight, based on the total
weight of the lubricating oil composition.
[0078] The kinematic viscosity at 100°C of the lubricating oil composition of the present
invention is preferably, but not limited to, 3 to 10 mm
2/s, more preferably 3 to 8 mm
2/s, still more preferably 4 to 7.5 mm
2/s, and most preferably 4 to 6 mm
2/s. When the kinematic viscosity at 100°C of the lubricating oil composition is less
than the above lower limit, it may not be possible to secure the friction coefficient.
When it is more than the above upper limit, the anti-shudder properties may deteriorate.
[0079] The viscosity index of the lubricating oil composition of the present invention is
preferably, but not limited to, not less than 150, more preferably not less than 160.
When the viscosity index of the lubricating oil composition is less than the above
lower limit, it may not be possible to sufficiently secure the fuel cost at 40°C.
The upper limit thereof is preferably, but not limited to, 250.
[0080] In spite of its low viscosity, the lubricating oil composition of the present invention
has not only a sufficiently high intermetallic friction coefficient but also anti-shudder
properties. In addition, as described above, by specifying the constitutions of the
base oil and the viscosity index improver in accordance with the present invention,
the shear stability can also be secured. Furthermore, by comprising an ether sulfolane
compound, it can secure moderate seal rubber swelling properties. In addition, by
using a metallic detergent having a total base number of 200 to 400 mgKOH/g, it can
favorably secure washability while preventing sludge generation. The lubricating oil
composition of the present invention can be suitably used for a non-stage transmission.
EXAMPLES
[0081] The present invention will now be described in greater detail by means of examples
and comparative examples, but the present invention is not limited to these examples.
[0082] The components used in the examples and comparative examples are as follows. Lubricating
oil compositions were prepared by mixing the components shown below at the amounts
shown in Table 1 or Table 2. Hereinafter, KV100 means a kinematic viscosity at 100°C,
VI means the viscosity index, and PMA means polymethacrylate.
(A) Lubricant base oil
[0083]
* Mineral oil 1: highly hydrorefined paraffinic base oil (KV100 = 3.1 mm2/s, VI = 112)
* Mineral oil 2: highly hydrorefined paraffinic base oil (KV100 = 4.2 mm2/s, VI = 122)
* Mineral oil 3: highly hydrorefined paraffinic base oil (KV100 = 4.2 mm2/s, VI = 134)
* Mineral oil 4: hydrorefined paraffinic base oil (KV100 = 2.2 mm2/s, VI = 109)
* Mineral oil 5: hydrorefined paraffinic base oil (KV100 = 2.5 mm2/s, VI = 99)
* Synthetic base oil 1: poly-α-olefin (KV100 = 10 mm2/s, VI = 137)
* Synthetic base oil 2: poly-α-olefin (KV100 = 40 mm2/s, VI = 147)
* Synthetic base oil 3: ethylene-α-olefin copolymer (KV100 = 10 mm2/s, VI = 150)
* Synthetic base oil 4: ethylene-α-olefin copolymer (KV100 = 40 mm2/s, VI = 155)
(B) Viscosity index improver
[0084] * PMA-based viscosity index improver 1 having an Mw of 30,000 and a structure of
- (CH
2-C(CH
3)(COOR))
n-
(C) Boronated succinimide compound
[0085]
(C-1)
* Boronated succinimide compound 1 (Mw = 5,600, B: 0.34 percent by weight, N = 1.58
percent by weight, a mixture of compounds represented by above formula (2), wherein
R1 is a polyisobutenyl group, and n is 4 to 12)
* Boronated succinimide compound 3 (Mw = 4,600, B: 1.8 percent by weight, N = 2.35
percent by weight, a mixture of compounds represented by above formula (2), wherein
R1 is a polyisobutenyl group, and n is 4 to 12)
(C-2)
* Boronated succinimide compound 2 (Mw = 8,500, B: 0.23 percent by weight, N = 0.88
percent by weight, a mixture of compounds represented by above formula (2), wherein
R1 is a polyisobutenyl group, and n is 4 to 12)
(D) Friction modifiers
[0086]
(D-1) Amide friction modifier
* (D-1a) Reaction product of isostearic acid and tris(hydroxymethyl)aminomethane
* (D-1b) Isostearic acid diethanolamide
* (D-1c) Stearic acid diethanolamide
* (D-1d) Oleic acid diethanolamide
* (D-1e) Lauric acid diethanolamide
(D-2) Friction modifier composed of a borate of epoxide or a ring-opened product thereof
* (D-2a) Borate of ethylene oxide oleate
* (D-2b) Borate of ethylene oxide stearate
* (D-2c) Borate of glycidyl oleate
* (D-2d) Borate of glycidyl laurate
(E) Metallic detergent
[0087]
* Ca sulfonate (total base number: 350 mgKOH/g)
* Ca salicylate (total base number: 300 mgKOH/g)
* Mg salicylate (total base number: 400 mgKOH/g)
(F) Ether sulfolane compound
[0088] * LUBRIZOL 730 (a compound represented by the following formula, wherein R
1 is C
10H
21)

(F) Other additives
[0089] Anti-wear agent, friction modifier, antioxidant, antifoaming agent, metal deactivator,
and coloring agent.
[Table 1-1]
[0090]
Table 1-1
|
|
Example 1 |
Example 2 |
Example 3 |
Example 4 |
Example 5 |
Example 6 |
Example 7 |
Example 8 |
(A) Base oil |
Mineral oil 1 |
70.39 |
70.39 |
83.08 |
83.08 |
|
|
|
70.99 |
Mineral oil 2 |
|
|
|
|
34.28 |
|
|
|
Mineral oil 3 |
|
|
|
|
|
25.13 |
|
|
Mineral oil 4 |
|
|
|
|
36.11 |
|
|
|
Mineral oil 5 |
|
|
|
|
|
45.26 |
71.82 |
|
Synthetic base oil 1 |
20.95 |
|
|
|
20.95 |
20.95 |
20.95 |
20.95 |
Synthetic base oil 2 |
|
|
|
8.26 |
|
|
|
|
Synthetic base oil 3 |
|
20.95 |
|
|
|
|
|
|
Synthetic base oil 4 |
|
|
8.26 |
|
|
|
|
|
(B) Viscosity index improver |
PMA-based viscosity index improver |
3.08 |
3.08 |
3.08 |
3.08 |
3.08 |
3.08 |
1.65 |
3.08 |
(c) Ashless dispersant |
Boron-containing succinimide compound 1 |
1.49 |
1.49 |
1.49 |
1.49 |
1.49 |
1.49 |
1.49 |
1.49 |
Boron-containing succinimide compound 2 |
0.33 |
0.33 |
0.33 |
0.33 |
0.33 |
0.33 |
0.33 |
0.33 |
Boron-containing succinimide compound 3 |
|
|
|
|
|
|
|
|
Metallic detergent |
Calcium sulfonate |
0.16 |
0.16 |
0.16 |
0.16 |
0.16 |
0.16 |
0.16 |
0.16 |
Calcium salicylate |
|
|
|
|
|
|
|
|
Magnesium salicylate |
|
|
|
|
|
|
|
|
[Table 1-2]
[0091]
Table 1-2
|
|
Example 1 |
Example 2 |
Example 3 |
Example 4 |
Example 5 |
Example 6 |
Example 7 |
Example 8 |
(D) Friction modifier (D-1) Amide friction modifier |
(D-1a) Reaction product of isostearic acid and tris(hydroxymethyl) aminomethane |
0.75 |
0.75 |
0.75 |
0.75 |
0.75 |
0.75 |
0.75 |
0.75 |
(D-1b) Isostearic acid diethanolamide |
|
|
|
|
|
|
|
|
(D-1c) Stearic acid diethanolamide |
|
|
|
|
|
|
|
|
(D-1d) Oleic acid diethanolamide |
|
|
|
|
|
|
|
|
(D-1e) Lauric acid diethanolamide |
|
|
|
|
|
|
|
|
(D) Friction modifier (D-2) Friction modifier composed of a borate of epoxide or a
ring-opened product thereof |
(D-2a) Borate of ethylene oxide oleate |
0.20 |
0.20 |
0.20 |
0.20 |
0.20 |
0.20 |
0.20 |
0.20 |
(D-2b) Borate of ethylene oxide stearate |
|
|
|
|
|
|
|
|
(D-2c) Borate of glycidyl oleate |
|
|
|
|
|
|
|
|
(D-2d) Borate of glycidyl laurate |
|
|
|
|
|
|
|
|
(D) Friction modifiers (other than the above friction modifiers) |
Glycerin monooleate |
|
|
|
|
|
|
|
|
N-(2-hydroxyhexadecyl) diethanolamine |
|
|
|
|
|
|
|
|
[Table 1-3]
[0092]
Table 1-3
|
|
Example 1 |
Example 2 |
Example 3 |
Example 4 |
Example 5 |
Example 6 |
Example 7 |
Example 8 |
Rubber swelling agent |
Ether-containing sulfolane |
0.60 |
0.60 |
0.60 |
0.60 |
0.60 |
0.60 |
0.60 |
|
Additive package |
Other additives (Anti-wear agent, friction modifier, antioxidant, antifoaming agent,
metal deactivator, and coloring agent) |
2.05 |
2.05 |
2.05 |
2.05 |
2.05 |
2.05 |
2.05 |
2.05 |
Base oil performance |
|
|
|
|
|
|
|
|
|
KV100 |
|
4.0 |
4.0 |
4.0 |
3.7 |
4.0 |
4.0 |
3.5 |
4.0 |
Composition performance |
|
|
|
|
|
|
|
|
|
[C2]/[C1] |
|
4.5 |
4.5 |
4.5 |
4.5 |
4.5 |
4.5 |
4.5 |
4.5 |
KV100 |
|
5.5 |
5.5 |
5.5 |
5.2 |
5.5 |
5.5 |
4.5 |
5.5 |
VI |
|
163 |
168 |
170 |
168 |
170 |
168 |
151 |
163 |
Shear stability |
|
4 |
4 |
4 |
4 |
4 |
4 |
4 |
4 |
Shudder |
|
450 |
450 |
450 |
450 |
450 |
450 |
450 |
450 |
Initial shudder |
|
1.3 |
1.3 |
1.3 |
1.3 |
1.3 |
1.3 |
1.3 |
1.3 |
Friction coefficient |
|
1.0 |
1.0 |
1.0 |
1.0 |
1.0 |
1.0 |
1.0 |
1.0 |
Swelling performance |
|
5 |
5 |
5 |
5 |
5 |
5 |
5 |
1 |
[Table 1-4]
[0093]
Table 1-4
|
|
Example 9 |
Example 10 |
Example 11 |
Example 12 |
Example 13 |
Example 14 |
Example 15 |
Example 16 |
Example 17 |
Example 18 |
(A) Base oil |
Mineral oil 1 |
70.39 |
70.39 |
70.39 |
70.39 |
70.39 |
70.39 |
70.39 |
70.39 |
70.39 |
70.39 |
Mineral oil 2 |
|
|
|
|
|
|
|
|
|
|
Mineral oil 3 |
|
|
|
|
|
|
|
|
|
|
Mineral oil 4 |
|
|
|
|
|
|
|
|
|
|
Mineral oil 5 |
|
|
|
|
|
|
|
|
|
|
Synthetic base oil 1 |
20.95 |
20.95 |
20.95 |
20.95 |
20.95 |
20.95 |
20.95 |
20.95 |
20.95 |
20.95 |
Synthetic base oil 2 |
|
|
|
|
|
|
|
|
|
|
Synthetic base oil 3 |
|
|
|
|
|
|
|
|
|
|
Synthetic base oil 4 |
|
|
|
|
|
|
|
|
|
|
(B) Viscosity index improver |
PMA-based viscosity index improver |
3.08 |
3.08 |
3.08 |
3.08 |
3.08 |
3.08 |
3.08 |
3.08 |
3.08 |
3.08 |
(c) Ashless dispersant |
Boron-containing succinimide compound 1 |
1.49 |
1.49 |
1.49 |
1.49 |
1.49 |
1.49 |
1.49 |
1.49 |
1.49 |
1.49 |
Boron-containing succinimide compound 2 |
0.33 |
0.33 |
0.33 |
0.33 |
0.33 |
0.33 |
0.33 |
0.33 |
0.33 |
0.33 |
Boron-containing succinimide compound 3 |
|
|
|
|
|
|
|
|
|
|
Metallic detergent |
Calcium sulfonate |
0.16 |
0.16 |
0.16 |
0.16 |
0.16 |
0.16 |
0.16 |
0.16 |
|
|
Calcium salicylate |
|
|
|
|
|
|
|
|
0.16 |
|
Magnesium salicylate |
|
|
|
|
|
|
|
|
|
0.16 |
[Table 1-5]
[0094]
Table 1-5
|
|
Example 9 |
Example 10 |
Example 11 |
Example 12 |
Example 13 |
Example 14 |
Example 15 |
Example 16 |
Example 17 |
Example 18 |
(D) Friction modifier (D-1) Amide friction modifier |
(D-1a) Reaction product of isostearic acid and tris(hydroxymethyl) aminomethane |
|
|
|
|
0.95 |
0.75 |
0.75 |
0.75 |
0.75 |
0.75 |
(D-1b) Isostearic acid diethanolamide |
0.75 |
|
|
|
|
|
|
|
|
|
(D-1c) Stearic acid diethanolamide |
|
0.75 |
|
|
|
|
|
|
|
|
(D-1d) Oleic acid diethanolamide |
|
|
0.75 |
|
|
|
|
|
|
|
(D-1e) Lauric acid diethanolamide |
|
|
|
0.75 |
|
|
|
|
|
|
(D) Friction modifier (D-2) Friction modifier composed of a borate of epoxide or a
ring-opened product thereof |
(D-2a) Borate of ethylene oxide oleate |
0.20 |
0.20 |
0.20 |
0.20 |
|
|
|
|
0.20 |
0.20 |
(D-2b) Borate of ethylene oxide stearate |
|
|
|
|
|
0.20 |
|
|
|
|
(D-2c) Borate of glycidyl oleate |
|
|
|
|
|
|
0.20 |
|
|
|
(D-2d) Borate of glycidyl laurate |
|
|
|
|
|
|
|
0.20 |
|
|
(D) Friction modifiers (other than the above friction modifiers) |
Glycerin monooleate |
|
|
|
|
|
|
|
|
|
|
N-(2-hydroxyhexadecyl) diethanolamine |
|
|
|
|
|
|
|
|
|
|
[Table 1-6]
[0095]
Table 1-6
|
|
Example 9 |
Example 10 |
Example 11 |
Example 12 |
Example 13 |
Example 14 |
Example 15 |
Example 16 |
Example 17 |
Example 18 |
Rubber swelling agent |
Ether-containing sulfolane |
0.60 |
0.60 |
0.60 |
0.60 |
0.60 |
0.60 |
0.60 |
0.60 |
0.60 |
0.60 |
Additive package |
Other additives (Anti-wear agent, friction modifier, antioxidant, antifoaming agent,
metal deactivator, and coloring agent) |
2.05 |
2.05 |
2.05 |
2.05 |
2.05 |
2.05 |
2.05 |
2.05 |
2.05 |
2.05 |
Base oil performance |
|
|
|
|
|
|
|
|
|
|
|
KV100 |
|
4.0 |
4.0 |
4.0 |
4.0 |
4.0 |
4.0 |
4.0 |
4.0 |
4.0 |
4.0 |
Composition performance |
|
|
|
|
|
|
|
|
|
|
|
[C2]/[C1] |
|
4.5 |
4.5 |
4.5 |
4.5 |
4.5 |
4.5 |
4.5 |
4.5 |
4.5 |
4.5 |
KV100 |
|
5.5 |
5.5 |
5.5 |
5.5 |
5.5 |
5.5 |
5.5 |
5.5 |
5.5 |
5.5 |
VI |
|
163 |
163 |
163 |
163 |
163 |
163 |
163 |
163 |
163 |
163 |
Shear stability |
|
4 |
4 |
4 |
4 |
4 |
4 |
4 |
4 |
4 |
4 |
Shudder |
|
400 |
300 |
300 |
250 |
450 |
450 |
450 |
450 |
450 |
450 |
Initial shudder |
|
1.3 |
1.3 |
1.3 |
1.3 |
0.3 |
1.3 |
1.3 |
1.3 |
1.3 |
1.3 |
Friction coefficient (TC ratio) |
|
1.02 |
1.03 |
1.03 |
1.04 |
1.01 |
1.00 |
1.00 |
1.00 |
1.00 |
1.00 |
Swelling performance |
|
5 |
5 |
5 |
5 |
5 |
5 |
5 |
5 |
5 |
5 |
[Table 2-1]
[0096]
Table 2-1
|
|
Comp. Example 1 |
Comp. Example 2 |
Comp. Example 3 |
Comp. Example 4 |
Comp. Example 5 |
Comp. Example 6 |
Comp. Example 7 |
(A) Base oil |
Mineral oil 1 |
70.39 |
70.39 |
70.39 |
70.20 |
70.39 |
70.39 |
70.39 |
Mineral oil 2 |
|
|
|
|
|
|
|
Mineral oil 3 |
|
|
|
|
|
|
|
Mineral oil 4 |
|
|
|
|
|
|
|
Mineral oil 5 |
|
|
|
|
|
|
|
Synthetic base oil 1 |
20.95 |
20.95 |
20.95 |
20.95 |
20.95 |
20.95 |
20.95 |
Synthetic base oil 2 |
|
|
|
|
|
|
|
Synthetic base oil 3 |
|
|
|
|
|
|
|
Synthetic base oil 4 |
|
|
|
|
|
|
|
(B) Viscosity index improver |
PMA-based viscosity index improver |
3.08 |
3.08 |
3.08 |
3.08 |
3.08 |
3.08 |
3.08 |
(c) Ashless dispersant |
Boron-containing succinimide compound 1 |
|
1.49 |
1.49 |
1.49 |
1.49 |
1.49 |
1.49 |
Boron-containing succinimide compound 2 |
0.33 |
0.33 |
0.33 |
0.33 |
0.33 |
0.33 |
0.33 |
Boron-containing succinimide compound 3 |
1.49 |
|
|
|
|
|
|
Metallic detergent |
Calcium sulfonate |
0.16 |
0.16 |
0.16 |
0.35 |
0.16 |
0.16 |
0.16 |
Calcium salicylate |
|
|
|
|
|
|
|
Magnesium salicylate |
|
|
|
|
|
|
|
[Table 2-2]
[0097]
Table 2-2
|
|
Comp. Example 1 |
Comp. Example 2 |
Comp. Example 3 |
Comp. Example 4 |
Comp. Example 5 |
Comp. Example 6 |
Comp. Example 7 |
(D) Friction modifier (D-1) Amide friction modifier |
(D-1a) Reaction product of isostearic acid and tris(hydroxymethyl) aminomethane |
0.75 |
|
|
|
|
|
|
(D-1b) Isostearic acid diethanolamide |
|
|
|
|
|
|
|
(D-1c) Stearic acid diethanolamide |
|
|
|
|
|
|
|
(D-1d) Oleic acid diethanolamide |
|
|
|
|
|
|
|
(D-1e) Lauric acid diethanolamide |
|
|
|
|
|
|
|
(D) Friction modifier (D-2) Friction modifier composed of a borate of epoxide or a
ring-opened product thereof |
(D-2a) Borate of ethylene oxide oleate |
0.20 |
0.95 |
|
|
|
|
|
(D-2b) Borate of ethylene oxide stearate |
|
|
0.95 |
|
|
|
|
(D-2c) Borate of glycidyl oleate |
|
|
|
0.95 |
|
|
|
(D-2d) Borate of glycidyl laurate |
|
|
|
|
0.95 |
|
|
(D) Friction modifiers (other than the above friction modifiers) |
Glycerin monooleate |
|
|
|
|
|
0.95 |
|
N-(2-hydroxyhexadecyl) diethanolamine |
|
|
|
|
|
|
0.95 |
[Table 2-3]
[0098]
Table 2-3
|
|
Comp. Example 1 |
Comp. Example 2 |
Comp. Example 3 |
Comp. Example 4 |
Comp. Example 5 |
Comp. Example 6 |
Comp. Example 7 |
Rubber swelling agent |
Ether-containing sulfolane |
0.60 |
0.60 |
0.60 |
0.60 |
0.60 |
0.60 |
0.60 |
Additive package |
Other additives (Anti-wear agent, friction modifier, antioxidant, antifoaming agent,
metal deactivator, and coloring agent) |
2.05 |
2.05 |
2.05 |
2.05 |
2.05 |
2.05 |
2.05 |
Base oil performance |
|
|
|
|
|
|
|
|
KV100 |
|
4.0 |
4.0 |
4.0 |
4.0 |
4.0 |
4.0 |
4.0 |
Composition performance |
|
|
|
|
|
|
|
|
[C2]/[C1] |
|
0 |
4.5 |
4.5 |
4.5 |
4.5 |
4.5 |
4.5 |
KV100 |
|
5.2 |
5.5 |
5.5 |
5.5 |
5.5 |
5.5 |
5.5 |
VI |
|
161 |
163 |
163 |
163 |
163 |
163 |
163 |
Shear stability |
|
4 |
4 |
4 |
4 |
4 |
4 |
4 |
Shudder |
|
20 |
200 |
200 |
200 |
200 |
50 |
50 |
Initial shudder |
|
-1.7 |
2.8 |
2.8 |
2.8 |
2.8 |
-1.1 |
-1.1 |
Friction coefficient |
|
1.0 |
0.96 |
0.96 |
0.96 |
0.96 |
0.94 |
0.94 |
Swelling performance |
|
5 |
5 |
5 |
5 |
5 |
5 |
5 |
[Table 2-4]
[0099]
Table 2-4
|
Comp. Example 8 |
KV100 |
7.2 |
VI |
201 |
Shear stability |
21 |
Shudder |
200 |
Initial shudder |
not measured |
Friction coefficient |
1.0 |
Swelling performance |
6 |