TECHNICAL FIELD
[0001] This disclosure relates to an engine system.
BACKGROUND ART
[0003] For example, Patent Document 1 discloses a large-scale reciprocating piston combustion
engine having a crosshead. The large-scale reciprocating piston combustion engine
disclosed in Patent Document 1 is a dual fuel engine that can be operated using both
a liquid fuel such as heavy oil and a gas fuel such as natural gas. In the large-scale
reciprocating piston combustion engine disclosed in Patent Document 1, in order to
correspond to both a compression ratio suitable for an operation using the liquid
fuel and a compression ratio suitable for an operation using the gas fuel, a crosshead
part has an adjustment mechanism that changes the compression ratio by using hydraulic
pressure to move a piston rod.
Citation List
Patent Document
[0004] [Patent Document 1] Japanese Unexamined Patent Application, First Publication No.
2014-20375
DISCLOSURE OF INVENTION
Technical Problem
[0005] An engine system having a compression adjustment device that changes the compression
ratio as described above changes a bottom dead center position and a top dead center
position of a piston by changing a position in a movement direction of the piston
rod. In this manner, the compression ratio is adjusted. However, according to the
engine system in the related art, a supply timing of a lubricating fluid in the piston
is fixed even when the piston rod is moved. Therefore, a supply position of the lubricating
fluid supplied to the piston varies when the compression ratio is low and when the
compression ratio is high. Consequently, there is a possibility that the lubricating
fluid may not be sufficiently supplied into a cylinder.
[0006] This disclosure is made in view of the above-described circumstances and aims to
sufficiently supply the lubricating fluid into the cylinder in the engine system including
a variable compression mechanism.
Solution to Problem
[0007] According to a first aspect of this disclosure, an engine system is provided including
a variable compression device having a fluid chamber to which a pressurized working
fluid is supplied so that a piston rod connected to a piston is moved in a high compression
ratio direction, a supply device that supplies a lubricating fluid to a cylinder portion
on which the piston slides, a detection device that outputs a signal including position
information of the piston, and a control device that controls the supply device, based
on the signal.
[0008] According to a second aspect of this disclosure, in the first aspect, the control
device may be configured to change a supply timing of the lubricating fluid of the
supply device, when the piston rod is moved in the high compression ratio direction.
[0009] According to a third aspect of this disclosure, in the second aspect, the control
device may be configured to adjust a supply amount per unit time of the lubricating
fluid in accordance with a preset compression ratio, when the piston rod is moved
in the high compression ratio direction.
[0010] According to a fourth aspect of this disclosure, in the second or third aspect, the
control device may be configured to increase a supply amount per one time of the lubricating
fluid.
[0011] According to a fifth aspect of this disclosure, in any one of the first to fourth
aspects, the detection device may be disposed in the cylinder portion, and may be
configured to output the signal including the position information of the piston.
[0012] According to a sixth aspect of this disclosure, in any one of the first to fourth
aspects, the detection device may be configured to have a sensor unit that detects
a movement of a detection target fixed to the piston rod in a non-contact manner.
Advantageous Effects of Invention
[0013] According to this disclosure, the control device changes the supply timing of the
lubricating fluid, based on the position of the piston rod or the piston. In this
manner, the lubricating fluid can always be supplied to the piston at a constant position
by changing a lubricating timing when the position of the piston is changed by the
variable compression mechanism. Therefore, the lubricating fluid can be sufficiently
supplied into the cylinder.
BRIEF DESCRIPTION OF DRAWINGS
[0014]
FIG. 1 is a sectional view of an engine system according to an embodiment of this
disclosure.
FIG. 2 is a schematic sectional view illustrating part of the engine system according
to the embodiment of this disclosure.
FIG. 3 is an enlarged sectional view illustrating part of the engine system according
to the embodiment of this disclosure.
FIG. 4 is an enlarged sectional view illustrating part of the engine system according
to the embodiment of this disclosure.
FIG. 5 is an enlarged sectional view illustrating part of the engine system according
to the embodiment of this disclosure.
FIG. 6 is a perspective view illustrating a position detection unit of the engine
system according to the embodiment of this disclosure.
FIG. 7 is a sectional view illustrating the position detection unit of the engine
system according to the embodiment of this disclosure.
BEST MODE FOR CARRYING OUT THE INVENTION
[0015] Hereinafter, an embodiment of an engine system 100 according to this disclosure will
be described with reference to the drawings.
[First Embodiment]
[0016] The engine system 100 according to the present embodiment is mounted on a ship such
as a large tanker, for example, and has an engine 1, a supercharger 200, and a control
unit 300 (control device) as illustrated in FIG. 1. In the present embodiment, the
supercharger 200 is regarded as an auxiliary machine, and will be described separately
from the engine 1 (main machine). However, the supercharger 200 can be configured
to serve as part of the engine 1. The supercharger 200 is not an essential configuration
element of the engine system 100 according to the present embodiment and does not
have to be disposed in the engine system 100. FIG. 1 is a longitudinal sectional view
taken along a center axis of a cylindrical cylinder liner 3a (to be described later)
disposed in the engine system 100. In FIG. 1, a side having an exhaust valve unit
5 (to be described later) may be referred to as an upper side, and a side having a
crankshaft 11 (to be described later) may be referred to as a lower side, in some
cases. A direction intersecting the center axis of the cylinder liner 3a may be referred
to as a radial direction, in some cases. A drawing viewed in a direction of the center
axis of the cylinder liner 3a may be referred to as a plan view, in some cases.
[0017] The engine 1 is a multi-cylinder uniflow scavenging diesel engine and is a dual fuel
engine that can perform a gas operation mode for combusting both a gas fuel such as
natural gas and a liquid fuel such as heavy oil and a diesel operation mode for combusting
the liquid fuel such as the heavy oil. In the gas operation mode, only the gas fuel
may be combusted. The engine 1 has a frame 2, a cylinder portion 3, a piston 4, an
exhaust valve unit 5, a piston rod 6, a crosshead 7, a hydraulic unit 8, a connecting
rod 9, a crank angle sensor 10, a crankshaft 11, a scavenging reservoir 12, an exhaust
reservoir 13, an air cooler 14, and a lubricating device 15 (supply device). In addition,
a cylinder is configured to include the cylinder portion 3, the piston 4, the exhaust
valve unit 5, and the piston rod 6.
[0018] The frame 2 is a strength member that supports the engine 1 as a whole and accommodates
the crosshead 7, the hydraulic unit 8, and the connecting rod 9. In addition, a crosshead
pin 7a (to be described later) of the crosshead 7 can reciprocate inside the frame
2.
[0019] The cylinder portion 3 has a cylindrical cylinder liner 3a, a cylinder head 3b, and
a cylinder jacket 3c. The cylinder liner 3a is a cylindrical member, and a sliding
surface for the piston 4 is formed inside the cylinder liner 3a. A space surrounded
by an inner peripheral surface of the cylinder liner 3a and the piston 4 is a combustion
chamber R1. In addition, a plurality of scavenging ports S are formed in a lower portion
of the cylinder liner 3a. The scavenging ports S are openings arranged along a peripheral
surface of the cylinder liner 3a, and allow a scavenging chamber R2 inside the cylinder
jacket 3c and the inside of the cylinder liner 3a to communicate with each other.
The cylinder head 3b is a lid member disposed in an upper end portion of the cylinder
liner 3a. The cylinder head 3b has an exhaust port H formed in a central portion in
a plan view, and is connected to the exhaust reservoir 13. In addition, the cylinder
head 3b has a fuel injection valve (not illustrated). Furthermore, a cylinder internal
pressure sensor 30 (detection device) is disposed in the vicinity of the fuel injection
valve of the cylinder head 3b. The cylinder internal pressure sensor 30 detects the
pressure inside the combustion chamber R1 and transmits a detection result to the
control unit 300. The cylinder jacket 3c is disposed between the frame 2 and the cylinder
liner 3a and is a cylindrical member into which a lower end portion of the cylinder
liner 3a is inserted. The scavenging chamber R2 is formed inside the cylinder jacket
3c. In addition, the scavenging chamber R2 of the cylinder jacket 3c is connected
to the scavenging reservoir 12.
[0020] The piston 4 has a substantially columnar shape, is connected to the piston rod 6
(to be described later) and is disposed inside the cylinder liner 3a. In addition,
a piston ring 4a is disposed on an outer peripheral surface of the piston 4, and the
piston ring 4a seals a gap between the piston 4 and the cylinder liner 3a. The piston
4 slides inside the cylinder liner 3a together with the piston rod 6 by using pressure
fluctuations in the combustion chamber R1.
[0021] The exhaust valve unit 5 has an exhaust valve 5a, an exhaust valve housing 5b, and
an exhaust valve driving unit 5c. The exhaust valve 5a is disposed inside the cylinder
head 3b, and the exhaust valve driving unit 5c closes the exhaust port H inside the
cylinder portion 3. The exhaust valve housing 5b is a cylindrical housing that houses
an end portion of the exhaust valve 5a. The exhaust valve driving unit 5c is an actuator
that moves the exhaust valve 5a in a direction along a stroke direction of the piston
4.
[0022] The piston rod 6 is an elongated member having one end connected to the piston 4
and the other end connected to the crosshead pin 7a. An end portion of the piston
rod 6 is inserted into the crosshead pin 7a and is connected so that the connecting
rod 9 is rotatable. In addition, the piston rod 6 has a large diameter portion in
which a partial diameter of an end portion on the crosshead pin 7a side is formed
to have a large diameter.
[0023] As illustrated in FIGS. 1 and 2, the crosshead 7 has the crosshead pin 7a, a guide
shoe 7b, and a lid member 7c. The crosshead pin 7a is a columnar member that movably
connects the piston rod 6 and the connecting rod 9 to each other, and an insertion
space into which an end portion of the piston rod 6 is inserted has a hydraulic chamber
R3 (fluid chamber) which working oil (working fluid) is supplied to and discharged
from. An exit hole O penetrating the crosshead pin 7a along an axial direction is
formed on a lower side from a center in the crosshead pin 7a. The exit hole O is an
opening from which cooling oil passing through a cooling flow path (not illustrated)
of the piston rod 6 is discharged. The crosshead pin 7a has a supply flow path R4
that connects the hydraulic chamber R3 and a plunger pump 8c (to be described later)
to each other, and a relief flow path R5 that connects the hydraulic chamber R3 and
a relief valve 8f (to be described later) to each other.
[0024] The guide shoe 7b is a member that pivotally supports the crosshead pin 7a and moves
on a guide rail (not illustrated) along the stroke direction of the piston 4 together
with the crosshead pin 7a. Since the guide shoe 7b moves along the guide rail, the
crosshead pin 7a is restricted in a rotational motion and a movement in a direction
other than a linear direction along the stroke direction of the piston 4. The lid
member 7c is an annular member which is fixed to an upper portion of the crosshead
pin 7a and into which an end portion of the piston rod 6 is inserted. The crosshead
7 transmits a linear motion of the piston 4 to the connecting rod 9.
[0025] As illustrated in FIG. 2, the hydraulic unit 8 includes a supply pump 8a, an oscillation
pipe 8b, a plunger pump 8c, a first check valve 8d and a second check valve 8e which
belong to the plunger pump 8c, and a relief valve 8f. In addition, the piston rod
6, the crosshead 7, the hydraulic unit 8, and the control unit 300 function as a variable
compression device according to this disclosure.
[0026] The supply pump 8a pressurizes the working oil supplied from a working oil tank (not
illustrated) and supplies the working oil to the plunger pump 8c based on an instruction
output from the control unit 300. The supply pump 8a is driven using battery power
of a ship and can be operated before the liquid fuel is supplied to the combustion
chamber R1. The oscillation pipe 8b connects the supply pump 8a and the plunger pump
8c of each cylinder and can oscillate between the plunger pump 8c moving together
with the crosshead pin 7a and the fixed supply pump 8a.
[0027] The plunger pump 8c is fixed to the crosshead pin 7a and has a rod-shaped plunger
8c1, a cylindrical cylinder 8c2 that slidably accommodates the plunger 8c1, and a
plunger driving unit 8c3. The plunger 8c1 is connected to the plunger driving unit
8c3. In this manner, the plunger pump 8c slides inside the cylinder 8c2, pressurizes
the working oil, and supplies the working oil to the hydraulic chamber R3. In addition,
the cylinder 8c2 has the first check valve 8d disposed in a working oil discharge
side opening disposed in an end portion and has the second check valve 8e in a suction
side opening disposed on a side peripheral surface. The plunger driving unit 8c3 is
connected to the plunger 8c1 and causes the plunger 8c1 to reciprocate based on an
instruction output from the control unit 300.
[0028] The first check valve 8d has a structure in which a valve body is biased inward of
the cylinder 8c2 to close the valve and prevents the working oil supplied to the hydraulic
chamber R3 from flowing back to the cylinder 8c2. In addition, when the pressure of
the working oil inside the cylinder 8c2 is equal to or greater than a biasing force
(valve opening pressure) of a biasing member of the first check valve 8d, the first
check valve 8d is opened since the valve body is pressed by the working oil. The second
check valve 8e is biased outward of the cylinder 8c2 and prevents the working oil
supplied to the cylinder 8c2 from flowing back to the supply pump 8a. In addition,
when the pressure of the working oil supplied from the supply pump 8a is equal to
or greater than a biasing force (valve opening pressure) of a biasing member of the
second check valve 8e, the second check valve 8e is opened since the valve body is
pressed by the working oil. The valve opening pressure of the first check valve 8d
is higher than the valve opening pressure of the second check valve 8e. When the first
check valve 8d is normally operated at a preset compression ratio, the first check
valve 8d is not opened by the pressure of the working oil supplied from the supply
pump 8a.
[0029] The relief valve 8f is disposed in the crosshead pin 7a and has a main body 8f1 and
a relief valve driving unit 8f2. The main body 8f1 is a valve connected to the hydraulic
chamber R3 and the working oil tank (not illustrated). The relief valve driving unit
8f2 is connected to the valve body of the main body 8f1 and opens and closes the main
body 8f1 based on an instruction output from the control unit 300. The relief valve
8f is opened by the relief valve driving unit 8f2, thereby causing the working oil
stored in the hydraulic chamber R3 to return to the working oil tank.
[0030] As illustrated in FIG. 1, the connecting rod 9 is an elongated member connected to
the crosshead pin 7a and connected to the crankshaft 11. The connecting rod 9 converts
the linear motion of the piston 4 which is transmitted to the crosshead pin 7a into
the rotational motion. The crank angle sensor 10 is a sensor for measuring a crank
angle of the crankshaft 11 and transmits a crank pulse signal for calculating the
crank angle to the control unit 300.
[0031] The crankshaft 11 is an elongated member connected to the connecting rod 9 disposed
in the cylinder and is rotated by the rotational motion transmitted by the connecting
rod 9, thereby transmitting power to a screw, for example. The scavenging reservoir
12 is disposed between the cylinder jacket 3c and the supercharger 200, and air compressed
by the supercharger 200 flows into the scavenging reservoir 12. In addition, the air
cooler 14 is disposed inside the scavenging reservoir 12. The exhaust reservoir 13
is a tubular member connected to the exhaust port H of each cylinder and connected
to the supercharger 200. The gas discharged from the exhaust port H is temporarily
stored in the exhaust reservoir 13 and is supplied to the supercharger 200 in a state
where pulsation is suppressed. The air cooler 14 is a device that cools the air inside
the scavenging reservoir 12.
[0032] The lubricating device 15 is disposed in an outer periphery on the exhaust port
H side of the cylinder liner 3a, and supplies lubricating oil (lubricating fluid)
toward the inside (combustion chamber R1) of the cylinder liner 3a by using a lubricating
hole through which the inside and the outside of the cylinder liner 3a communicate
with each other. The lubricating device 15 can change a lubricating amount and a lubricating
timing based on an instruction output from the control unit 300.
[0033] The supercharger 200 is a device that supplies compressed air to the combustion chamber
R1 after compressing air suctioned from an intake port (not illustrated) by using
a turbine rotated by gas exhausted from the exhaust port H.
[0034] The control unit 300 changes a compression ratio in the combustion chamber R1 by
controlling the hydraulic unit 8. Specifically, the control unit 300 acquires position
information of the piston rod 6 based on a signal output from the cylinder internal
pressure sensor 30, controls the plunger pump 8c, the supply pump 8a, and the relief
valve 8f, and adjusts the amount of the working oil in the hydraulic chamber R3. In
this manner, the control unit 300 changes the compression ratio by changing the position
of the piston rod 6. Furthermore, the control unit 300 changes the lubricating amount
and the lubricating timing of the lubricating device 15 based on the position information
of the piston rod 6.
[0035] The engine system 100 ignites and explodes the fuel injected into the combustion
chamber R1 from a fuel injection valve (not illustrated) so that the piston 4 slides
inside the cylinder liner 3a and the crankshaft 11 is rotated. Specifically, the fuel
supplied to the combustion chamber R1 is mixed with the air flowing from the scavenging
port S. Thereafter, the fuel is compressed by the piston 4 moving in a direction toward
the top dead center. In this manner, the temperature of the fuel rises and the fuel
is spontaneously ignited. In addition, in a case of the liquid fuel, the liquid fuel
evaporates by the temperature rise in the combustion chamber R1 and is spontaneously
ignited.
[0036] Then, the fuel inside the combustion chamber R1 rapidly expands due to spontaneous
ignition, and the pressure is applied to the piston 4 in a direction toward the bottom
dead center. In this manner, the piston 4 moves in the direction toward the bottom
dead center, the piston rod 6 moves together with the piston 4, and the crankshaft
11 is rotated via the connecting rod 9. Furthermore, since the piston 4 is moved to
the bottom dead center, the compressed air flows into the combustion chamber R1 from
the scavenging port S. Since the exhaust valve unit 5 is driven, the exhaust port
H is opened, and the exhaust gas inside the combustion chamber R1 is pushed out to
the exhaust reservoir 13 by the compressed air.
[0037] In a case where the compression ratio increases, the supply pump 8a is driven by
the control unit 300, and the working oil is supplied to the plunger pump 8c. Then,
the control unit 300 drives the plunger driving unit 8c3, pressurizes the working
oil until the working oil has the pressure which enables the piston rod 6 to be lifted,
and supplies the working oil to the hydraulic chamber R3. Due to the pressure of the
working oil in the hydraulic chamber R3, the end portion of the piston rod 6 is lifted,
and accordingly, the top dead center position of the piston 4 is moved upward (to
the exhaust port H side).
[0038] In a case where the compression ratio decreases, the relief valve driving unit 8f2
is driven by the control unit 300 so as to drive the relief valve 8f. The hydraulic
chamber R3 and the working oil tank (not illustrated) are brought into a communicable
state. Then, a load of the piston rod 6 is applied to the working oil in the hydraulic
chamber R3, and the working oil inside the hydraulic chamber R3 is pushed out to the
working oil tank via the relief valve 8f. In this manner, the working oil in the hydraulic
chamber R3 decreases, and the piston rod 6 is moved downward (to the crankshaft 11
side). Accordingly, the top dead center position of the piston 4 is moved downward.
[0039] Subsequently, the lubricating timing of the engine system 100 according to the present
embodiment will be described.
[0040] As illustrated in FIGS. 3 to 5, the lubricating device 15 supplies the lubricating
oil into the cylinder liner 3a three times, that is, before the piston 4 passes through
a lubrication hole, when the piston ring 4a of the piston 4 passes through the lubrication
hole, and after the piston ring 4a of the piston 4 passes through the lubricating
hole.
[0041] For example, the lubricating device 15 performs the lubricating at an interval of
approximately once every two cycles. In this manner, the piston ring 4a of the piston
4 does not scrape all of the lubricating oil, and the lubricating oil spreads to the
upper end (exhaust port H side) of the cylinder liner 3a.
[0042] When the lubricating timing is controlled, the piston rod position acquisition unit
310 calculates a position of the piston rod 6 in a height direction, based on an input
from the cylinder internal pressure sensor 30. Specifically, the position of the piston
rod 6 in the height direction is calculated by the following procedure.
[0043] In a case where the cylinder internal pressure when the piston 4 is located at the
bottom dead center is defined as P
0 and the cylinder internal pressure when the piston 4 is located at the top dead center
is defined as P
1, a compression ratio ε is expressed by Equation 1 below. The κ indicates a polytropic
index.
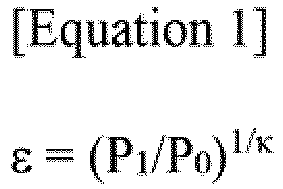
[0044] Based on Equation 1 above, the piston rod position acquisition unit 310 calculates
the compression ratio in the cylinder portion 3 from an electric signal (signal including
the position information of the piston rod 6) output from the cylinder internal pressure
sensor 30. Furthermore, the piston rod position acquisition unit 310 calculates the
position of the piston rod 6 in the height direction based on the compression ratio.
[0045] The control unit 300 monitors the position on a real time basis by acquiring the
position of the piston rod 6 in the height direction which is calculated using the
above-described method from the piston rod position acquisition unit 310. When the
control unit 300 detects that the piston rod 6 is moved in an upward direction (high
compression ratio direction) based on the position of the piston rod 6 in the height
direction, the control unit 300 instructs the lubricating device 15 so that three
lubricating timings are respectively earlier than the lubricating timings when the
compression ratio is low. Furthermore, while the piston rod 6 is moved in the upward
direction, the control unit 300 instructs the lubricating device 15 to increase (adjust)
the lubricating amount per one time based on a map indicating a correlation between
the preset compression ratio and the lubricating amount. The control unit 300 gradually
changes the lubricating timing in accordance with the position of the piston rod 6
in the height direction and causes the lubricating device 15 to perform the lubricating
so that the lubricating timings are always as illustrated in FIGS. 3 to 5. That is,
based on the position of the piston rod 6 in the height direction, the control unit
300 causes the lubricating device 15 to perform the lubricating using the lubricating
oil, before the piston 4 passes through the lubricating hole, when the piston ring
4a of the piston 4 passes through the lubricating hole, and after the piston ring
4a of the piston 4 passes through the lubricating hole. When the piston rod 6 is moved
in a low compression ratio direction, the lubricating timing is delayed from the lubricating
timing when the compression ratio is high. The piston rod position acquisition unit
310 may be disposed adjacent to the control unit 300 as illustrated in FIG. 1, or
may be disposed separately from the control unit 300. In any case, the piston rod
position acquisition unit 310 is communicably connected to the control unit 300. The
piston rod position acquisition unit 310 may have a configuration conforming to the
control unit 300. The piston rod position acquisition unit 310 may be part of the
control unit 300. Here, the control unit 300 is a computer that controls a supply
amount or the like of the fuel, based on an operation or the like performed by a ship's
operator. That is, the control unit 300 may be a known computer including a CPU, a
RAM, and a ROM which can perform the above-described control. Details of the control
performed by the control unit 300 may be defined by software that can be optionally
changed or updated by a user. As illustrated in FIG. 1 or 2, the control unit 300
is electrically or electronically connected. Alternatively, the control unit 300 receives
a feedback of the pressure inside the combustion chamber R1 from the cylinder internal
pressure sensor 30 connected so that a signal can be communicated by wireless or wire
communication, and a crank pulse signal from the crank angle sensor 10. Based on the
feedback and the signal, if necessary, the control unit 300 appropriately controls
the supply pump 8a, the plunger driving unit 8c3, the relief valve driving unit 8f2,
the exhaust valve driving unit 5c, the lubricating device 15, and the hydraulic unit
8.
[0046] According to the engine system 100 in the present embodiment, the control unit 300
changes the lubricating timing of the lubricating device 15, based on the position
of the piston rod 6 in the height direction. Therefore, the lubricating can be performed
at a timing at which a relative position between the lubricating device 15 and the
piston 4 is always constant. In this manner, the lubricating oil can be supplied to
the upper end side of the cylinder liner 3a, and lubricating ability can be maintained
inside the cylinder liner 3a.
[0047] In addition, the fuel (heavy oil) used for the operation at the high compression
ratio is highly corrosive, and the cylinder liner 3a needs to be sufficiently lubricated.
According to the engine system 100 in the present embodiment, when the piston rod
6 is moved upward, the control unit 300 causes the lubricating device 15 to increase
the lubricating amount per one time based on the position of the piston rod 6 in the
height direction. In this manner, the lubricating ability can be sufficiently maintained
even during the operation at the high compression ratio.
[Second Embodiment]
[0048] A modification example of the above-described first embodiment will be described
as a second embodiment. The same reference numerals will be given to members having
the same configuration as that according to the above-described first embodiment,
and description thereof will be omitted.
[0049] The engine system 100 according to the present embodiment has a position detection
unit 400 (detection device). As illustrated in FIG. 6, the position detection unit
400 has a magnetic sensor 410 (sensor unit), a rod portion 420, and a communication
unit 430. The magnetic sensor 410 is a sensor which is fixed to the lid member 7c
and generates an electric signal (signal including position information of the piston
rod 6) by using a change in a magnetic field which is caused by the movement of the
rod 421 (to be described later).
[0050] The rod portion 420 has a rod 421, a holding portion 422, a biasing spring 423, and
a magnetic member 424. The rod 421 is a rod-shaped member having a flange that holds
the biasing spring 423 in the vicinity of an end portion. The rod 421 is inserted
into a through-hole formed in the lid member 7c together with the holding portion
422 and is disposed along the extending direction of the piston rod 6. The rod 421
is pressed against and fixed to a large diameter portion of the end portion of the
piston rod 6 by the biasing spring 423. The holding portion 422 is a cylindrical member
fixed to the lid member 7c and into which the rod 421 is inserted. The rod 421 can
reciprocate inside the holding portion 422. The biasing spring 423 is disposed between
the flange of the rod 421 and the large diameter portion of the piston rod 6 and biases
the rod 421 toward the large diameter portion of the piston rod 6. The magnetic member
424 is a member in which a plurality of magnets are arranged at an equal interval
and is disposed on a peripheral surface of the rod 421 along the extending direction
of the rod 421.
[0051] The communication unit 430 is a telemeter that transmits the electric signal detected
by the magnetic sensor 410 to the control unit 300 by wireless communication.
[0052] When the rod 421 is moved due to the movement of the piston rod 6 in the position
detection unit 400, the magnetic member 424 is moved. Accordingly, the magnetic field
detected by the magnetic sensor 410 is changed. The magnetic sensor 410 outputs the
change in the magnetic field as the electric signal. In the present embodiment, the
control unit 300 calculates the position of the piston rod 6 in the height direction
based on an input from the position detection unit 400.
[0053] According to the engine system 100 in the present embodiment, the control unit 300
changes the lubricating timing of the lubricating device 15 based on the position
of the piston rod 6 in the height direction. Therefore, the lubricating can be performed
at the timing at which the relative position between the lubricating device 15 and
the piston 4 is always constant. In this manner, the lubricating oil can be supplied
to the upper end side of the cylinder liner 3a, and lubricating ability can be maintained
inside the cylinder liner 3a. Furthermore, according to the present embodiment, the
position of the piston rod 6 in the height direction can be directly detected. Therefore,
the position of the piston rod 6 in the height direction can be more accurately recognized.
The piston rod 6, the crosshead 7, the hydraulic unit 8, the control unit 300, and
the position detection unit 400 function as the variable compression device according
to this disclosure.
[Third Embodiment]
[0054] The engine system 100 according to the present embodiment has a position detection
unit 500 (detection device) instead of the position detection unit 400. As illustrated
in FIG. 7, the position detection unit 500 has a sensor unit 510 and a detection target
520. The sensor unit 510 is embedded in and fixed to a lower end side of the inner
peripheral surface of the cylinder liner 3a, which is located farther away from the
combustion chamber R1 than the scavenging port S. The sensor unit 510 is a sensor
which generates an electric signal (signal including the position information of the
piston rod 6) by using a change in a distance from a surface of the detection target
520 which is caused by the movement of the two detection targets 520.
[0055] The detection targets 520 are disposed on a lower end side of a sliding surface of
the piston 4 and are respectively configured to include a plurality of irregularities
formed at an equal interval in a sliding direction of the piston 4. The detection
target 520 is disposed below (on the piston rod 6 side) the piston ring 4a (not illustrated)
disposed in the piston 4. In this manner, the detection target 520 is less likely
to be affected by the lubricating oil on the sliding surface of the piston 4.
[0056] In the position detection unit 500, when the piston 4 is moved due to the movement
of the piston rod 6, the irregularities of the detection target 520 are moved relative
to the sensor unit 510. Accordingly, the distance from the detection target 520 to
the sensor unit 510 detected by the sensor unit 510 is changed. The sensor unit 510
outputs the change in the irregularities, that is, a change in the relative distance
from the surface of the detection target 520 to the sensor unit 510 to the control
unit 300 as the electric signal. According to the present embodiment, the control
unit 300 calculates the position of the piston rod 6 in the height direction based
on an input from the position detection unit 500.
[0057] According to the engine system 100 in the present embodiment, the control unit 300
changes the lubricating timing of the lubricating device 15 based on the position
of the piston rod 6 in the height direction. Therefore, the lubricating can be performed
at the timing at which the relative position between the lubricating device 15 and
the piston 4 is always constant. In this manner, the lubricating oil can be supplied
to the upper end side of the cylinder liner 3a, and lubricating ability can be maintained
inside the cylinder liner 3a.
[0058] Furthermore, the sensor unit 510 is embedded in the cylinder liner 3a fixed to the
frame 2. In this manner, the sensor unit 510 and the control unit 300 can be easily
connected to each other by wire communication. Therefore, the sensor unit 510 is easily
installed without needing to provide the communication unit or the like.
[0059] Hitherto, the preferred embodiments according to this disclosure have been described
with reference to the drawings. However, this disclosure is not limited to the above-described
embodiments. Various shapes or combinations of respective components illustrated in
the above-described embodiments are merely examples and can be modified in various
ways based on design requirements within the scope not departing from the concept
of this disclosure.
[0060] In the above-described embodiments, the lubricating timing is provided three times.
However, this disclosure is not limited thereto. The number of the lubricating timings
or the lubricating timing can be changed depending on a shape of the piston 4 or a
characteristic of the engine.
[0061] In addition, the detection device which detects the position of the piston rod 6
in the height direction is not limited to the form disclosed in the above-described
embodiments. For example, the position of the piston rod 6 or the piston 4 may be
measured by a laser distance meter provided as the detection device.
[0062] In addition, in the above-described embodiments, the control unit 300 increases
the lubricating amount when the piston rod 6 is moved in the high compression ratio
direction. However, this disclosure is not limited thereto. Based on a map indicating
a correlation between the compression ratio and the lubricating amount, the lubricating
amount may be decreased or remain unchanged. In addition, in the above-described embodiments,
when the piston rod 6 is moved in the high compression ratio direction, the control
unit 300 may adjust the supply amount per unit time of the lubricating fluid in accordance
with the preset compression ratio.
Industrial Applicability
[0063] According to this disclosure, the engine system including the variable compression
mechanism can sufficiently supply the lubricating fluid into the cylinder.
Reference Signs List
[0064]
- 1:
- engine
- 2:
- frame
- 3:
- cylinder portion
- 3a:
- cylinder liner
- 3b:
- cylinder head
- 3c:
- cylinder jacket
- 4:
- piston
- 4a:
- piston ring
- 5:
- exhaust valve unit
- 5a:
- exhaust valve
- 5b:
- exhaust valve housing
- 5c:
- exhaust valve driving unit
- 6:
- piston rod
- 7:
- crosshead
- 7a:
- crosshead pin
- 7b:
- guide shoe
- 7c:
- lid member
- 8:
- hydraulic unit
- 8a:
- supply pump
- 8b:
- oscillation pipe
- 8c:
- plunger pump
- 8c1:
- plunger
- 8c2:
- cylinder
- 8c3:
- plunger driving unit
- 8d:
- first check valve
- 8e:
- second check valve
- 8f:
- relief valve
- 8f1:
- main body
- 8f2:
- relief valve driving unit
- 9:
- connecting rod
- 10:
- crank angle sensor
- 11:
- crankshaft
- 12:
- scavenging reservoir
- 13:
- exhaust reservoir
- 14:
- air cooler
- 15:
- lubricating device
- 30:
- cylinder internal pressure sensor
- 100:
- engine system
- 200:
- supercharger
- 300:
- control unit
- 310:
- piston rod position acquisition unit
- 400:
- position detection unit
- 410:
- magnetic sensor
- 420:
- rod portion
- 421:
- rod
- 422:
- holding portion
- 423:
- biasing spring
- 424:
- magnetic member
- 430:
- communication unit
- 500:
- position detection unit
- 510:
- sensor unit
- 520:
- detection target
- H:
- exhaust port
- O:
- exit hole
- R1:
- combustion chamber
- R2:
- scavenging chamber
- R3:
- hydraulic chamber
- R4:
- supply flow path
- R5:
- relief flow path
- S:
- scavenging port